Smarter chemistry The well-being of our employees, customers, people in our supply chain, and the planet is a priority for Apple, which is why we’re committed to using safer materials to create safer products. This commitment requires diligent work — to build a comprehensive picture of chemicals across our supply chain, to insist on rigorous chemical management processes, to promote adoption of safer chemical alternatives, and to innovate through design smarter approaches to making our products. Using safer chemistry in our products also enables recycling and material recovery, so that our products can be the raw materials for the next generation. The pillars of our smarter chemistry strategy are: Mapping and engagement: Engage our supply chain partners to comprehensively identify the chemicals in the materials used to make our products, allowing us to drive change that goes beyond what is required for regulatory compliance. Assessment and management: Assess the potential human health and environmental risks of chemicals to evaluate compliance with our requirements and inform product design. Innovation: Drive the development and use of innovative materials that enable the creation of groundbreaking products and also support industrywide change. Mapping and engagement Our Full Material Disclosure (FMD) program maps the chemicals used in our products — an effort that includes tens of thousands of parts and assemblies. Then we look at how our products are manufactured. Our Chemical Safety Disclosure (CSD) program engages with supply chain partners to get the most recent information on which materials are in use. This information includes the volume of materials being consumed and how they’re being applied, stored, and handled — as well as the steps being taken to protect employees. We require each of our suppliers to participate in the CSD program, collectively sharing information on thousands of materials used to manufacture our products. More than 1000 supplier facilities have shared their chemical inventories as well as storage and safety Zero waste Across our corporate operations, we’re reducing the amount of waste we generate and directing more toward recycling programs. In fiscal year 2021, recycling and composting efforts allowed us to achieve a waste diversion rate of 68 percent, limiting landfill waste from our global operations to about 15,000 metric tons. 12 Our overall waste generated also remained low, in part due to COVID-related temporary closure of facilities. Last year, our Mesa, Arizona, data center became the second Apple facility to receive TRUE certification for zero waste, following the Prineville data center in 2020. 13 Apple works with the Alliance for Water Stewardship and others to promote water stewardship that protects the health of water basins, including the Kunshan watershed in China. 100+ Apple supplier facilities are zero waste verified 2M+ metric tons of waste redirected from landfill by supplier facilities as part of Apple’s Zero Waste Program Read more about our efforts to conserve resources in our 2022 Environmental Progress Report We’ve partnered with our suppliers, recyclers, and waste solution providers to eliminate waste from our manufacturing processes. At the close of fiscal year 2021, more than 100 facilities had been zero waste verified — nearly half of the supplier facilities that are part of our Zero Waste Program. 14 All participating facilities across 12 countries can access resources including guidance on how to reduce waste and then reuse, recycle, or compost the waste they do create. And we’re seeing results: In fiscal year 2021, suppliers redirected 491,000 metric tons of waste from landfills, bringing the total to over 2 million metric tons since the program’s inception — the equivalent of eliminating more than 2.5 million square meters of landfill space. Appendix Governance Communities Suppliers Customers Our People Environment Introduction Apple’s 2022 ESG Report 20
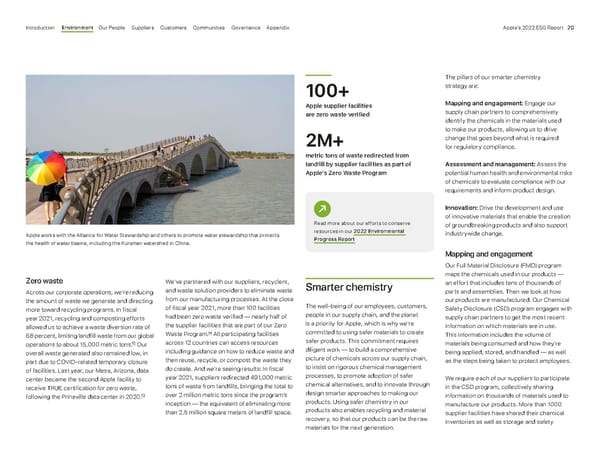