Safety Excellence and guidance from ORCHSE , a division of the U.S. National Safety Council (General Mills is an ORCSHE member). The new safety metric criteria at General Mills are company- specific and based on the globally recognized principles of the ASTM E2920 international standard for recording occupational injuries and illnesses . Fiscal 2021 was a baseline year for our new safety metrics. Like fiscal 2020, we gathered safety data from 198 tracked locations, 56 of which are production facilities and Innovation, Technology and Quality centers. Those 56 locations were the focus of our safety improvement work. Safety highlights from those locations in fiscal 2021 include: n Zero General Mills and contractor fatalities globally n 50% reduction in serious injuries vs. fiscal 2020 n 14 locations operated with zero reportable injuries this fiscal year n A new baseline injury/illness rate of 2.14 was established Beginning in fiscal 2021, our company safety incident totals and injury/ illness rate looks different because it is based on a subset of the former data. We now calculate rate based on 1,000,000 hours worked as compared to 200,000 under U.S. Occupational Safety and Health Administration (OSHA) Total Injury Rate (TIR) criteria. We continued reinforcing our safety programs in fiscal 2021: n Standards – We published our first-ever standard focused specifically on SIF prevention. n Measurement – We leveraged our fiscal 2020 safety metrics change and improved our capability to identify and reduce SIF potential globally (we identified and took action to address over 1,100 potential SIF incidents in fiscal 2021). We also deployed new company environmental metrics and began data capture related to significant environmental incidents. n Mitigation – We recalibrated the safety and environmental aspects of our capital expenditure process to prioritize funding and improve controls related to our critical safety and environmental risks. n Learning and culture – We introduced additional global learning experiences focused on critical risk management and SIF prevention. We also began development of our next safety culture offering, Safety Leadership 2.0, which is based on current human and organizational performance principles. Leadership and responsibility: n Our Global Safety Governance Board, composed of regional operating vice presidents, oversees safety leadership, structure, processes and actions. n Senior-level responsibility for workplace safety lies with the Director of Global Safety and Environment, who reports to the Chief Supply Chain Officer. n Our Corporate Safety Council is led by our Chairman and Chief Executive Officer, who is responsible for General Mills policy and safety culture. The council, which includes key members of the company’s executive leadership team, reviews safety progress and key initiatives. The Council’s focus is on growing safety culture in both manufacturing and nonmanufacturing locations. n Workplace health and safety is the responsibility of line management and each individual employee. All employees are expected to work safely by following policies, procedures and training. Leaders are accountable for understanding and removing barriers to safe work that may be system related. New safety metrics enable focus on critical risks: PREVIOUS SAFETY METRICS Based on U.S. OSHA TIR* Reasons for the change: n Previous criteria and metrics were not aligned with our current incident prevention strategy. n Metrics were adding increased cost/risk and compromising our safety culture. n New metrics and data were required to evolve in safety. NEW SAFETY METRICS Based on ASTM E2920 principles Benefits: n More globally relevant and aligned with our strategy. n Regions continue to report injuries and illnesses per their local regulatory requirements. n Enables integration of other complementary safety metrics within General Mills to advance serious injury and fatality (SIF) prevention. * U.S. Occupational Safety and Health Administration (OSHA) Total Injury Rate (TIR) **Global incident data includes all General Mills owned/operated facilities, including Yoki and Yoplait International, Häagen- Dazs shops, Blue Buffalo and global offices. Injury/illness rate ** FY13 FY17 FY15 FY19 FY14 FY18 FY16 FY20 0.5 0.0 1.5 1.0 2.5 2.0 1.63 1.34 1.22 1.20 0.85 0.77 0.98 0.85 FY21 0.0 1.0 2.0 3.0 New safety metric based on ASTM E2920 international standard (2021 baseline year). Previous injury/illness rate results based on U.S. OSHA TIR* (# of injuries/illnesses x 200,000) ÷ (# of hours worked) (# of injuries/ illnesses x 1,000,000) ÷ (# of hours worked) 2.14 ** 2.14 GENERAL MILLS GLOBAL RESPONSIBILITY 46 Food Planet People Community
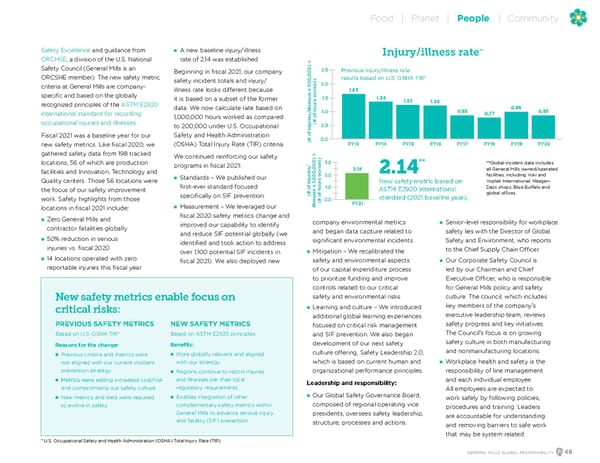