Devices Over the past year, devices became even more essential as they kept us connected, working, and learning through the pandemic. This year, higher-than-anticipated demand translated to higher sales and greater usage, which caused our absolute emissions to grow. We are committed to reducing the carbon intensity of our devices and our efforts have also grown this year. We have made significant investments to expand our data-driven lifecycle assessment (LCA) and telemetry approach to better measure, inform, and prioritize top reduction opportunities to reduce our device carbon intensity across the full lifecycle of our devices. These efforts include carbon-conscious design, reducing supply chain emissions, innovating energy-efficient hardware and software in use, and enabling product repairability, reusability, and recyclability. This will allow us to deliver the best product experience with lower carbon intensity, while also partnering with our users to minimize carbon footprint when using our products. Building a data-driven platform for product design In 2020, we began working on a platform to allow engineers to make real-time design and material selection decisions based on carbon impact, a key enabler in modeling and reducing our future device emissions. To generate our device carbon footprints, we conduct LCAs in accordance with ISO 14040 and ISO 14044 which enable us to estimate emissions from manufacturing our devices down to the individual component level. Further, we are upgrading our audit management sourcing tool to ensure supplier carbon reduction initiatives are fully reflected in these product carbon footprints. We pair this with improved product usage and distribution data. For example, the most recent iterations of the Xbox Series X|S have improved our awareness of full ecosystem energy usage from consoles, information which is critical to future energy efficiency improvements and emissions reductions. These investments allow us more control over our product emissions across their full lifecycle. Sustainable Product Lifecycle Experimenting with lower carbon design As informed by our LCAs, a significant lever in product development is the engineering of low-carbon design alternatives, such as using recycled materials and designing for a smaller manufacturing footprint. Reduced waste We designed our Surface Laptop Studio to allow for “stamping,” a lower-waste manufacturing technique that reduced our aluminum scrap rate for the product’s base by at least 25 percent, a key contributor to an overall product carbon reduction of 30 percent versus its predecessor, the Surface Book 3 13” . 6 Metals We are developing opportunities to reuse manufacturing scrap in aluminum production, allowing us to use lower- carbon, 100 percent post-industrial recycled closed loop aluminum for future Surface computer housings. For neodymium in magnets, a rare earth material, we are also exploring post-industrial scrap as a manufacturing feedstock, enabling us to produce 100 percent recycled neodymium in magnets for future products. Circuit boards In our labs, we are working to engineer a lower-carbon and reduced-waste flax-based wiring board and experimenting with 3D printing; we have started to explore 100 percent post-industrial recycled tin in our soldering paste; and we are aiming to reduce overall materials needed through new spacing guidelines that can shrink our circuit boards in size by up to 25 percent. 30% Reduction in total carbon emissions of 30 percent for Surface Laptop Studio versus its predecessor, Surface Book 3 13” . - Getting to carbon negative (continued) 27 Product design Raw materials sourcing Packaging and distribution Product use Product manufacturing End-of life Repair, refurbishment, and recycling -
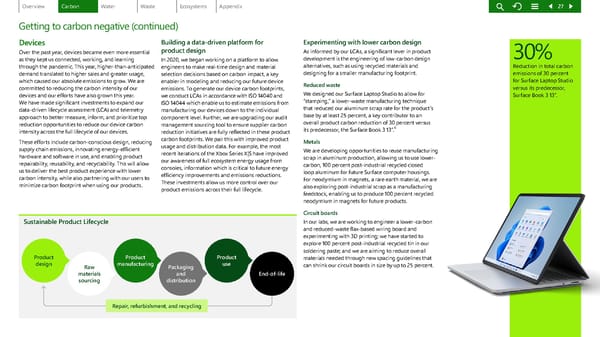