Customer Trust & Satisfaction We put customers at the center of everything we do and strive to deliver the highest possible levels of product quality. Our focus on product quality and our customers aligns the entire company behind the goal of exceeding customer expectations and providing them with the best overall experience. GM brands, products and services aim for benchmarks in studies measuring product quality and consumer satisfaction. Vehicle Development Process Our focus on the customer defines how we develop, engineer and manufacture our vehicles with quality and durability goals in mind, starting with the vehicle development process. We harness customer feedback from global markets to help shape our customers’ product experience, using our GM Compass customer survey to gather preferences on a variety of issues—from performance and efficiency to how people interact with their vehicles. The Global Vehicle Development Process is rooted in a cultural commitment to design, engineer and build quality vehicles. Building upon GM’s “Who We Are” and “How We Behave” foundational statements, employees are committed to a goal of delivering quality as a value supported by key initiatives and behaviors. This commitment involves three elements: Product Safety , which includes our Speak Up For Safety program, Safety Field Investigation processes, Prevent Repeat Defects process and Safety Incident Protocols. The Speak Up For Safety program and Safety Field Investigation processes help identify and investigate potential issues. Prevent Repeat Defects is one of the approaches we use to help confirm field learnings are captured in our standard work to prevent the issue from reoccurring. Systems Engineering , which uses a systems approach to translate our customers’ needs into industry-leading vehicle designs. IT-based systems help map, flow and trace requirements across engineering organizations to help ensure our products are safe, reliable and win in the marketplace. Quality Chain is an integrated approach to connecting quality tools and methods that enables cross-functional team collaboration to mitigate defects from reaching our customers. This is executed by connecting vehicle-level requirements to system, subsystem and component levels. This helps drive enterprisewide engagement so design and process issues can be mitigated across all systems and processes. We also emphasize systems engineering companywide. This includes requiring all people to practice the discipline of systems thinking, understanding how their individual roles contribute to the bigger picture, rather than thinking in silos. GM also has quality tools that work as interconnected processes and cross system and organizational boundaries. Using these tools together helps us build discipline into our process for identifying and addressing failure modes. These product development centric elements are foundational and complemented by our Launch Excellence initiative. The initiative uses affinity diagrams to help teams focus on what must be true in terms of process and discipline to successfully navigate vehicle development. Beginning with 2022 model year vehicles, a new warranty was announced in the United States and Canada that will provide coverage for any seatbelt or airbag system for six years or 72,000 miles, whichever comes first. Skip Navigation Introduction Reducing Emissions Design for Environment Technology Customers Safety Diverse Workforce Human Rights Supply Chain Communities Governance 2021 SUSTAINABILITY REPORT 49
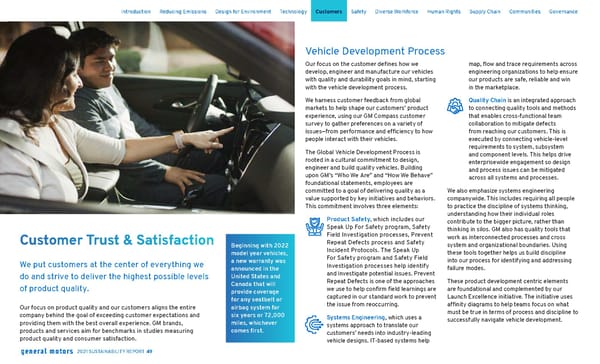