FY21 ESG Disclosures July 2022 Unaudited 48 HSE Auditing Auditing is a key component in verifying Jacobs’ HSE program implementation across the company and identifying areas for improvement. Audit schedules are developed by organizational HSE leads (for example, BU, regions, and global performance units) and approved by LOB HSE leads. Audit schedules are developed based on factors such as risk, negative trends, and accreditation requirements. Audit program implementation including selection of projects, auditor assignments, auditor training, and recordkeeping is defined in Jacobs’ HSE Audit Schedule procedure. Additional audit requirements based on geography, project type, client requirements and similar factors are included in LOB/BU and program, project, or office-specific HSE processes as needed. Management Review HSE performance is reviewed on a regular basis within the LOB/BU and other organizational groups. HSE performance is reviewed at least annually at the global and LOB level as detailed in Jacobs’ Management Review procedure. Management reviews for other organizational groups are performed to determine that the HSE Program is suitable, adequate, and effective. Identified corrective actions or improvements are facilitated by group leadership and the supporting HSE lead as detailed in Jacobs’ HSE Performance procedure. SOC.13 HSE – Products and Services Jacobs does not offer consumer products; we principally provide services and solutions to our clients. HSE in Design Jacobs undertakes a vast range of design services whereby our designers understand the risks associated with the lifecycle of the asset and how design decisions can influence how assets are built, operated, maintained and demolished. By considering the whole lifecycle of a project our designers can not only improve the HSE benefits of a design, but also improve the health and wellbeing of workers, and reduce potential environmental impacts, with greater efficiency of construction, operation and maintenance, leading to reductions in program length and cost savings. De5ign is Jacobs’ behavioral program driving a cultural shift in HSE in Design, which takes Jacobs beyond base legislative requirements to provide a consistent approach to HSE in design across our global business, maximizing HSE benefits across the lifecycle of our projects. De5ign is inclusive of the process to identify and record the risks, use hazard identification/elimination and risk reduction assessments, design hazard lists and red, amber, green lists, and to take residual risks as low as reasonably practicable by consulting with all parties involved. De5ign supports Jacobs’ design professionals by providing an HSE in-design toolset and integrated training. The framework is scalable in application, ranging from small streetscape design services to advanced research and development and technology industry facilities solutions. De5ign supports and leverages Jacobs’ key BeyondZero and PlanBeyond strategies. Employees at all levels are encouraged to challenge unsafe design and speak up when they need support. Our BeyondZero Observation system is used to collect and share learning and HSE in design best practices. Our HSE in Design reviews with HSE professionals drive tangible improvement to all aspects of HSE including wellbeing, occupational and mental health. HSE in De5ign is integrated with our approach to digital solutions, innovation, and technology to generate high value solutions for our clients and customers.
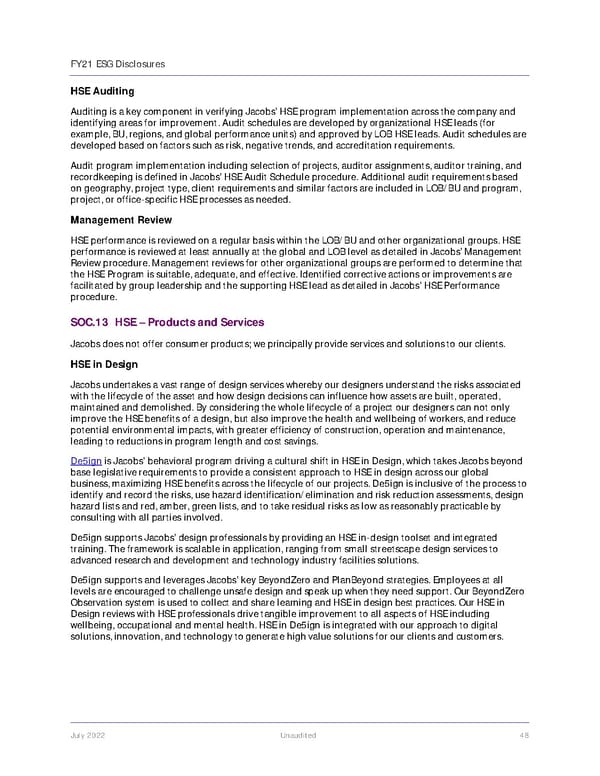