Introduction Climate Change Resources Smarter Chemistry Engagement and Advocacy Appendix 2023 Environmental Progress Report 49 Low-water design One example is our new Capstone campus in Austin, We approach low-water design by first focusing on site Texas, where we aim to achieve net-zero water use. selection, conducting a water risk evaluation to determine To accomplish this, the campus will rely on an onsite whether a potential site is in a water-stressed area or wastewater reuse system, as well as condensate recovery not. We aim to avoid locating water-intensive processes and stormwater capture, limiting potable water use to in water-stressed locations, so we either use the results potable purposes only. This effort will avoid 60 m illion to select a more appropriate site where possible, or to gallons of freshwater use, relying instead on nonpotable water for cooling and toilet flushing. 63 This cooling mitigate the impact of our expected water use. approach will also allow us to achieve 28 m illion kWh Then, we look to systems and processes that use less in energy savings annually at the location. water or reuse water, so that we can limit excess water In our supply chain, a majority of water is used during consumption and, where possible, eliminate waste. We manufacturing. For example, in 2019 we launched a also design solutions to manage the quality of the water pilot program at a manufacturing location in China as that we return to the watershed. part of our anodizing improvement program with the In our corporate operations, we discharge the majority of aim of reducing, and eventually eliminating, potentially our wastewater to the sanitary sewer. Up to 44 percent hazardous discharge as well as reducing water and of the water that we use at our corporate locations is chemical use. Anodizing is the most water-intensive discharged back into the local water system rather process in the metal-finishing process of enclosures. than consumed. 62 We monitor the water quality As part of the pilot, we employed several water efficiency from sites where we have an industrial wastewater approaches, including using cascade and counterflow discharge so that each location meets or exceeds local rinsing processes, which helped retain 75 to 85 percent discharge requirements. of the water used during metal finishing. This process improvement has the potential to save millions of gallons of freshwater annually when applied at scale. The aluminum anodizing process is typically water-intensive. In 2019, we launched a pilot to seek to eliminate hazardous discharge and increase water efficiency from anodizing. The cascade and counterflow rinsing processes, which helped retain 75 to 85 percent of the water used during metal finishing, could save millions of gallons of freshwater annually when applied at scale.
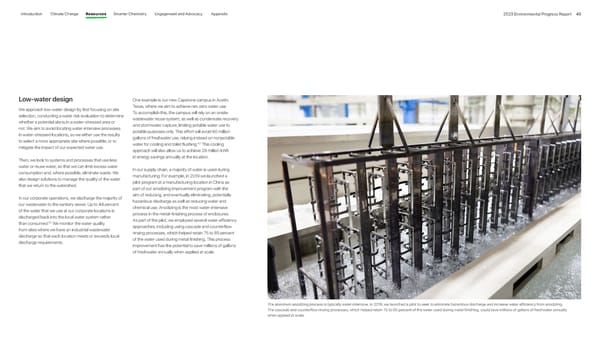