GeneralMills Global Responsibility Report
2022 Global RESPONSIBILITY
68 Appendix 68 ESG Issues and definitions 69 Environmental data summary 70 Global Reporting Initiative index 75 United Nations Global Compact Principles 76 Sustainability Accounting Standards Board reference table 8 Food 9 Food safety 10 Nutrition 16 Consumer education and marketing 18 Transparency 1 Introduction 1 To our stakeholders 2 Company overview 3 Fiscal 2021 report dashboard 4 Environmental, social and governance issues 5 Oversight 5 Stakeholder engagement 6 Public policy 7 About this report 19 Planet 22 Climate change 25 Ingredient sourcing 26 Eliminating deforestation 28 Regenerative agriculture 32 Water stewardship 35 Packaging 36 Sustainable operations 38 Responsible sourcing 40 Animal welfare 56 Community 58 Alleviating hunger 62 Regenerating ecosystems 63 Strengthening hometown communities 41 People 43 Human rights 45 Workplace safety 47 Global inclusion 53 Employee well-being and development ©2022 General Mills. Table of contents
To our stakeholders Jeffrey L. Harmening Chairman, Chief Executive Officer General Mills INTRODUCTION For more than 150 years, General Mills has been making food the world loves. For us that has always meant ensuring our food is a reflection of our ability to do good for our people, planet and communities. That central mission is at the heart of General Mills — and was never more important than it was in 2021. Putting people first In the face of the COVID-19 pandemic, our employees met the moment with resolve. They understood that under normal circumstances we dedicate ourselves to make food the world loves — but in the pandemic, we are also making food the world needs. We appreciate that millions of families are nourished by our food. So when disruptions in the global supply chain came, we committed ourselves to innovative and creative new approaches to ensure we could successfully deliver to meet our consumers’ needs — and we did. Our focus on putting people first extends beyond our consumers to across our entire value chain... the farmers who grow our ingredients, our employees, who are the heartbeat of General Mills and, of course, the communities we are proud to be a part of and serve. We took additional steps in 2021 to provide our employees with a safe workplace, to support their mental health and well-being, and to foster a culture of inclusion and belonging, so that employees could bring their unique selves to work every day and thrive. Addressing inequality We also continued our commitment to use our scale to drive sustainable and meaningful change on issues of racial and social injustice. We come to the table humble, understanding these are broad and complex issues. But we also come with resolve knowing that we have to be part of a larger collective effort if we hope to make significant progress in this space. We have made progress to target racial disparities in food security and its disproportionate impacts on communities of color, support nonprofit organizations that are working to bring about equity in education, and address representation and access opportunities within our own workforce. For example, through our Box Tops for Education program we are equipping teachers to identify and address racial bias, supporting programs to increase the number of teachers of color, and distributing funds to impact schools in need across our headquarters community in Minnesota. Regenerating our planet As extreme weather events occur with greater intensity and frequency around the world — with devastating effects on people and the natural resources necessary to produce food — we recognize that adopting more sustainable practices is not enough. We instead need to regenerate the world’s resources to strengthen ecosystems and community resilience. General Mills is leading the industry in advancing regenerative agriculture by partnering with farmers, advancing science, and measuring outcomes. We see regenerative agriculture driving significant impact on planetary health, people and in reaching our 2030 and 2050 climate targets. In our 52nd year of reporting social and environmental performance to stakeholders, we remain committed to disclosing our progress, as well as our challenges. We continue to support key global efforts to advance the sustainability agenda, including the United Nations Global Compact, which we have endorsed since 2008. While plenty of work remains to be done, we are optimistic. I am incredibly proud of the General Mills team that shows up every day with passion, care and ingenuity. We are inspired by the past and energized by the future we are shaping together. We understand we have a role to play — and we are more determined than ever to ensure the G in General Mills stands for Good. Sincerely, Jeff GENERAL MILLS GLOBAL RESPONSIBILITY 01
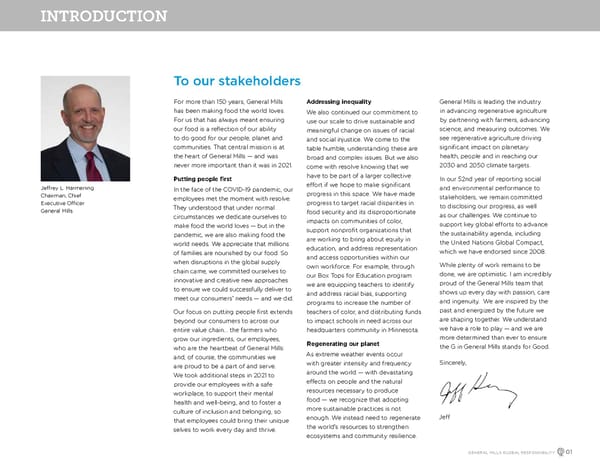
OUR PURPOSE OUR STRATEGY OUR FORCE FOR GOOD PRIORITIES FISCAL 2021 HIGHLIGHTS Company overview Boldly building brands Relentlessly innovating Unleashing our scale Being a force for good Regenerating our planet Improving food security Protecting our people Strengthening our communities 96% of our company-owned production facilities are Global Food Safety Initiative (GFSI) certified. 41% of General Mills global volume met the company’s criteria as Nutrition-Forward Foods in fiscal 2021. #1 General Mills is the largest provider of natural and organic packaged food in the U.S.* 115,000 acres enrolled in programs advancing regenerative management. 63% renewable electricity sourced for our global operations. 89% of General Mills packaging recyclable or reusable (by weight). 50% reduction in serious injuries at our production facilities and Innovation, Technology and Quality centers in fiscal 2021 compared to fiscal 2020. 51% of professional positions and 33% of company officer positions are held by women globally. 90% of our employees say that General Mills is a great place to work, up 4% from 2020. $98 million We gave US$98.3 million to charitable causes in fiscal 2021, including General Mills Foundation grants, corporate contributions and food donations. 41 million Our product donations to food banks enabled 41 million meals around the world in fiscal 2021. 6 continents Our strategic philanthropy and our community giving in General Mills hometown communites spanned six continents in fiscal 2021. FOOD PEOPLE PLANET COMMUNITY *Includes food for both humans and pets. Source: SPINS 52 WE 12/26/2021, Total — US Mulo, Natural Enhanced Channel and Pet Channel. GENERAL MILLS GLOBAL RESPONSIBILITY 02
Fiscal 2021 report dashboard Section Commitment/goal or key performance indicator 2021 Progress Food Achieve Global Food Safety Initiative (GFSI) certification of all company-owned facilities 96% Global volume meeting criteria as Nutrition-Forward Foods (% of global volume) 41% Ranking of largest natural and organic packaged food providers in the U.S. #1 Planet Reduce greenhouse gas emissions by 30% by 2030 vs 2020 baseline (% change) 2% increase Advance regenerative agriculture on 1 million acres of farmland by 2030 (# of acres advancing regenerative management) 115,000 All General Mills packaging to be recyclable or reusable by 2030 (% of global packaging by weight) 89% Champion activation of water stewardship plans for the company's most at-risk watersheds by 2025 (# of at-risk watersheds with active plans in place) 3 out of 10 Source 100% renewable electricity for our global operations by 2030 (% achieved) 63% Reduce food waste in operations by 50% by 2030 vs 2020 baseline (% reduction) 24% reduction Achieve zero waste to landfill at all owned production facilities by 2025 (% achieved) 28% Purchase 100% cage-free or free-range eggs for our global operations by 2025 (% contracted) 61% People Advance respect for human rights across our value chain ongoing Global injury/illness rate per million hours worked (based on ASTM E2920 international standard) 2.14 Women in professional positions (% of global salaried employees) 51% Increase minority representation to 25% (% of U.S. salaried employees) 19% Representation of Black managers (% of U.S. salaried employees) 3% Spend with minority-owned suppliers (US$) $318 million Percent of employees that say General Mills is great place to work 90% Community Amount of charitable giving (US$) $98 million Meals enabled by donations of General Mills surplus food worldwide (# of meals) 41 million Enable 30 billion meals by 2030 through food donations and philanthropic partnerships (cumulative # of meals) 17 billion Throughout the year General Mills has continued our work to be a Force for Good across our value chain, from agriculture and operations to our consumers and communities. Below is a summary of our progress in fiscal 2021. This table does not cover all metrics contained in the report; it includes key commitments and goals as well as select performance indicators in areas of importance to General Mills and our stakeholders. Please refer to each section of the report for details and definitions on these and other metrics. GENERAL MILLS GLOBAL RESPONSIBILITY 03
Environmental, social and governance issues In 2021, we partnered with Pivot Strategies to conduct an update of our ESG issues assessment, last done in 2018. We started this process by developing a list of issues to be evaluated based on: n Results of our 2018 assessment n Peer company ESG disclosures n Internal issues management prioritization n Input from General Mills experts and leaders n Key reporting disclosure frameworks n Stakeholder and consumer research Based on this review and analysis, we created and distributed a survey to more than 80 external and internal stakeholders to assist us with assessing these issues. External stakeholders included NGOs, industry associations, investors, academic institutions, customers, suppliers and peer companies. Internal stakeholders included subject matter experts and leaders from across the company, mostly director-level and above and with significant experience within General Mills. Stakeholders were asked to assess the relative impact of each issue based on two dimensions: external impact (the impact that General Mills has on society and the environment from each issue) and internal impact (the impact of each issue on the company’s performance and enterprise value, considering factors such as revenue, expenses, reputation, risk, capital investment, market access and financial reporting impacts). The results of the survey were aggregated, and each issue was placed on a matrix based on its relative impact on the two dimensions. This ESG issues assessment and prioritization will help guide our strategy and reporting and has enhanced our understanding of what stakeholders feel are currently the most impactful issues for our company to address. We recognize that all of the issues assessed are important and interconnected, and do not view this assessment in isolation, but rather in conjunction with our broader business strategy and priorities. For definitions and boundaries for each of these issues, please refer to the Appendix . n Climate change n Food safety and quality n Health and nutrition n Ingredient sourcing n Packaging n Regenerative agriculture n Biodiversity n Board and executive oversight n Diversity, equity and inclusion n Ethics and compliance n Hunger and food security n Regulatory compliance n Responsible marketing and labeling n Responsible sourcing n Talent management n Transparency n Waste n Water stewardship n Workplace safety n Animal welfare n Community giving and engagement n Deforestation n Human rights n Privacy and data security n Public policy List of issues for ESG issues assessment External survey Internal survey ESG issues assessment process ESG issues matrix Results of 2018 assessment Industry peers External disclosure frameworks Other stakeholder and consumer research General Mills leaders and experts Impact on General Mills’ performance/value General Mills’ impact on people, environment and economy HIGH MODERATE HIGH MODERATE Tier 3 issues Tier 1 issues Tier 2 issues TIER 1: Priority issues core to General Mills’ strategy and performance TIER 3: Issues of importance with focused strategies TIER 2: Significant issues to our business GENERAL MILLS GLOBAL RESPONSIBILITY 04
Oversight Stakeholder engagement At General Mills, we engage with stakeholders to accelerate progress on social and environmental initiatives. Our approach includes open dialogue, collaboration and transparent disclosure. This strengthens our ability to balance business and societal interests; build robust relationships globally across sectors; and ultimately, identify innovative solutions that create shared, sustainable value. We are working to address shared issues — such as health and nutrition, racial equity, climate change and water stewardship — so collaboration is essential to achieving long-term, enduring progress. We work with other companies and organizations to shape standards across the consumer packaged goods industry, which elevates overall sector performance. We engage on issues that are material to our global responsibility strategy and where we can have a substantial positive impact. When engaging with stakeholders, we assess potential alignment on objectives, organizational expertise, capacity, influence and willingness to collaborate. For example, in May 2021 General Mills hosted our first-ever ESG investor event , held virtually. The event included a pre-recorded presentation as well as a live question-and-answer session with management. The engagement reached more than 300 attendees and highlighted the Force for Good pillar of the company’s Accelerate strategy, focusing on how General Mills is regenerating the planet, improving food security, strengthening communities and advancing inclusion among the company’s people and through its brands. The Global Impact Governance Committee, led by our Chairman and CEO and overseen by the Board’s Public Responsibility Committee, is accountable for our global responsibility programs. The Board’s Public Responsibility Committee provides extensive oversight and receives regular updates from the operating teams. Our Chairman and CEO convenes the Global Impact Governance Committee at least three times per year. The purpose of the Committee is to establish, direct and oversee General Mills’ position on matters of significance to the company and its stakeholders concerning corporate social responsibility, environmental and sustainability issues, and philanthropy. Additional details about leadership and governance related to specific global responsibility issues are included in relevant sections of this report. See Corporate Governance to learn more about the company’s broader corporate governance structures and processes, including its Public Responsibility Committee . r This graphic outlines governance and management of global responsibility focus areas at General Mills. Board of Directors’ Public Responsibility Committee Chief Strategy and Growth Officer Global Impact Governance Committee CEO, Chairman of the Board Chief Financial Officer Chief Supply Chain Officer Chief Innovation, Technology and Quality Officer Chief Strategy and Growth Officer Chief Human Resources Officer Group President, North American Retail Chief Communications Officer General Counsel and Secretary Chief Innovation, Technology and Quality Officer Chief Human Resources Officer Global Responsibility Focus Areas Global Impact (sustainability and philanthropy) Health and Nutrition Workplace CEO, Chairman of the Board v This graphic illustrates the range of issues on which we engage with stakeholders. Employees n COVID-19 response n Diversity and inclusion n Employee satisfaction n Training and development NGOs n Packaging n Biodiversity n Human rights n Soil health n Sustainable sourcing n Water stewardship Consumers n Consumer feedback/concerns n Education and responsible marketing n Product needs and preferences Industry associations n Food safety n Public policy n Regenerative agriculture n Sustainable sourcing Customers n Industry partnerships n Product innovation n Sustainability collaboration Suppliers n Animal welfare n Human rights n Regenerative agriculture n Sustainable sourcing Investors n Financial performance n Governance n Social and environmental issues n Sustainability Communites n COVID-19 response n Employee volunteerism n Food security n Racial equity Regulators and public policymakers n Climate change n Food security n Packaging n Water stewardship GENERAL MILLS GLOBAL RESPONSIBILITY 05
At General Mills, we actively engage in public policy issues that are important to our company and stakeholders. We are committed to conducting these activities in an accountable and transparent manner. We articulate our approach in the Public Policy for the Greater Good area of our website. Our public policy priorities include: n Protecting and preserving our planet: w L eading on regenerative agriculture and soil health – General Mills is a leading voice on regenerative agriculture. We invest to help support farmers as they shift toward more sustainable practices and encourage collaboration and investment by governments and the private sector, such as our support for the Foundation for Food and Ag Research ( FFAR ), a critical facilitator of public private partnerships between industry and farmers. Policy is a critical tool to advance this work. We also encourage the U.S. Congress to strengthen collaboration between organizations, components of our supply chains and domestic agriculture producers to meet our ambitious sustainability goals. w C ombating climate change – We have established industry-leading, science-based targets for carbon reduction and advocate for climate change policies: we support a comprehensive, national climate policy; joined Ceres’ LEAD on Climate 2020 Day calling for action; have publicly called for the U.S. to remain in the Paris Climate Accord ; and support the U.S. Environmental Protection Agency’s (EPA) Clean Power Plan . See a list of our public actions here . w Supporting s tronger organic standards – We work to promote and protect the integrity of organic standards and advance their continuous improvement. Learn about our support for the National Organic Standards Board (NOSB) and the Organic Agriculture Research and Extension Initiative (OREI) . w A dvancing water stewardship – We engage policymakers to driv e more sustainable water practices in key watersheds, like California and Kansas. w Addressing packaging and food waste – We promote policies to effectively and efficiently increase p ackaging recycling rates and reduce waste. In the U.S., we are a leader in AME RIPEN — the American Institute for Packaging and the Environment — and are actively engaged in multiple coalitions aimed at red ucing food waste and loss. n Delivering nutrition: We work to advance nutrition priorities, including support for strong Dietary Guidelines for Americans, the U.S. Food and Drug Administration’s (USDA) efforts to reflect the newest scientific information on the definition of “healthy,” strong U.S. school nutrition standards, and the Supplemental Nutrition Program for Women, Infants and Children (WIC). n Ensuring safe food: We strongly support the Food Safety Modernization Act (FSMA) and its goal of raising food safety standards across the food value chain. We have consistently called on Congress to continue adequate funding for FSMA implementation. n Increasing food security and strengthening communities: w Incr easing food security – At the federal level, we are a longtime supporter of The Congressional Hunger Center . We also work with numerous partners to advance policy at the state level. w Pr otecting people – We advocate for inclusive public policies and add our voice to help lead change, including for inclusive U.S. immigration and LGBTQ+ policies . w S trengthening our communities – We develop important community partnerships that drive economic growth, increase connections and improve equity. For example, we are a leader in the Minnesota Business Coalition for Racial Equity and have advocated for Public policy General Mills supports the United Nations (UN) Sustainable Development Goals (SDGs) , and we focus on the goals that align with the company’s priority issues and areas of long-standing commitment, investment and progress. n Food security n Food waste n Health and nutrition n Food safety n Health and nutrition n Talent management n Water stewardship n Climate change n Energy use n Ingredient sourcing n Packaging footprint n Climate change n Food waste n Packaging n Water stewardship n Biodiversity n Deforestation n Ingredient sourcing n Ethics and compliance n Human rights n Public policy n Biodiversity n Water stewardship n Diversity, equity and inclusion n Food security n Human rights n Responsible sourcing n Human rights n Responsible sourcing n Talent management n Climate change n Energy use n Diversity, equity and inclusion n Human rights n Responsible sourcing n Community engagement n Diversity, equity and inclusion n Talent management n Food security n Human rights n Regenerative agriculture United Nations Sustainable Development Goals GENERAL MILLS GLOBAL RESPONSIBILITY 06
the Minnesota legislature to enact policing reforms . Learn more in the Community section of this report. n Informing consumers and increasing awareness: We support public policy efforts to inform our consumers about our products. For example, we are active members of several organizations that provided comments to the USDA requesting that more information about bioengineered ingredients be made available to consumers, not less. Learn more in the Transparency content in this report. Compliance: We comply with all lobbying regulations where applicable and file regular reports on our lobbying activity. General Mills is registered as a lobbying entity at the federal level for the U.S. House of Representatives and U.S. Senate and in the states of Minnesota and California. Political contributions and memberships Our civic policy describes our approval process for corporate political contributions. The Public Responsibility Committee of the Board of Directors oversees the company’s political activities, including our policy, disclosure of corporate political contributions, membership in major trade associations and independent political expenditures (although the company has not made any). For details and historical information, see our 2005-2021 civic involvement reports . The General Mills Political Action Committee (G-PAC) is run by employees and uses employee funds to make political contributions to federal and, in limited cases, state candidates. No corporate treasury funds are used for federal candidate contributions, but as allowed by law, the company pays G-PAC administration costs. All G-PAC transactions are publicly disclosed via reports available on the Federal Election Commission website. General Mills also advances its mission by partnering with trade associations and other independent organizations that share our goals, including: n International organizations, such as EuroGlaces and the Brazilian Association of Food Industries . n U.S. public-policy-focused organizations, such as the Consumer Brands Association and the National Association of Manufacturers . n State or provincial agencies, local chambers of commerce and manufacturing organizations, such as the Minnesota Chamber of Commerce and the Ohio Manufacturers Association . We report details about our largest U.S. trade association memberships annually in our civic involvement reports. We do not belong to, or make payments to, any tax-exempt organizations in the U.S. that write and endorse model legislation. Accountability: In 2021, the Center for Political Accountability rated General Mills as one of the top “Trendsetters” in its CPA-Zicklin Index of Corporate Political Disclosure and Accountability . This ranking, which includes all companies in the Standard & Poor’s 500 Index, maintained our leading performance from past years. The General Mills Global Responsibility Report describes our commitments, goals, programs and performance across a broad range of issues. The company’s Global Impact Team has responsibility for the development of the report. Ultimate accountability lies with the Global Impact Governance Committee ( see page 5 ). The Global Responsibility Report is an important part of a broader set of disclosures that provide stakeholders a multifaceted description of General Mills performance, including the company’s annual report , SEC filings and annual proxy statement . Report scope n The report covers the company’s global operations in fiscal 2021 (52 weeks ended May 30, 2021), except where noted otherwise. n Data for fiscal 2021 Scope 1, 2 and 3 GHG emissions have been verified by Apex Companies, LLC. For details, see the Environmental data summary and Greenhouse gas emissions sections in the Appendix. n Unless otherwise noted, data in this report is not externally veri- fied and may occasionally be re- stated due to improvements in da ta collection methodology. n Actual results may vary significantly from expectations expressed or implied in this report. Undue reliance should not be placed on forward- looking statements, which speak only as of the date they are made. We do not undertake to update or revise any forward-looking statements, except as required by law. Reporting standards n This report references the GRI 2016 Sus- tainability Reporting Standards , as well as the F ood Processing Sector Supple- ment. See the GRI index for details. n This report references the Sustainability Accounting Standards Board (SASB) Processed Foods Standard . See the S ASB index for details. n General Mills endorsed the principles of the UN Global Compact in 2008. This report serves as the company’s annual Communication on Progress. See the UN Global Compact index for details. Stakeholder input For the last several years, General Mills has engaged Ceres to convene a group of external stakeholders to provide input on our annual Global Responsibility Report. This year, 11 stakeholders, including investors, NGO representatives, corporate practitioners and industry experts, provided feedback on a detailed report draft. We value this input and have incorporated much of their feedback into the report. Feedback We welcome your comments about this report. Please send any feedback to [email protected] . About this report GENERAL MILLS GLOBAL RESPONSIBILITY 07
of General Mills global volume met the company’s criteria as Nutrition-Forward Foods in fiscal 2021. 41 % of our company-owned production facilities are Global Food Safety Initiative (GFSI) certified. 96 % General Mills is the largest provider of natural and organic packaged food in the U.S.* # 1 At General Mills, our purpose is making food the world loves. Food safety n Nutrition Consumer education and marketing n Transparency IN THIS SECTION *Includes food for both humans and pets. Source: SPINS 52 WE 12/26/2021, Total — US Mulo, Natural Enhanced Channel and Pet Channel. GENERAL MILLS GLOBAL RESPONSIBILITY 08 Food
Our approach: Safety is a priority for our company and central to our culture. Leading with safety — both in the workplace and the food we make — is one of the key operating principles that guides our work. We share best practices with industry peers, suppliers and regulators to help raise standards industry-wide. Systems: Our global food safety systems focus on prevention, intervention and response. n Processes – Food safety is integrated into all our processes, beginning with R&D and extending across our supply chain. n Risk mitigation – We conduct internal risk-based surveillance and food safety testing at all General Mills facilities to identify and prioritize specific areas of risk. n Audits – Our Global Internal Audit team periodically audits the effectiveness and efficiency of food safety controls and operating procedures. Results are reported to the company’s Global Governance Council and Board of Directors. n Traceability – Our inventory control and supplier management systems include the ability to trace the sources of our ingredients, which is key to isolating risks in the event of food safety concerns. We evaluate our suppliers’ systems to ensure they meet our traceability requirements. Governance: n Policies – Governance of General Mills food safety and regulatory matters begins with a corporate Food Safety and Regulatory Policy signed by our Chief Executive Officer. This corporate- wide policy is supported by 18 individual policies with accompanying standards, procedures and guidelines.* n Leadership – The Vice President of Food Safety and Quality has direct responsibility for food safety. The Global Internal Audit team periodically verifies that our food safety processes and controls are operating effectively. The company’s Global Governance Council conducts a quarterly review of risk, which includes food safety. Suppliers: n Audits – We conduct supplier and co-producer audits globally to help ensure the safety of the raw materials we use in our products. In addition to performing direct virtual and physical onsite audits, we encourage third- party audits and/or certification as an additional preventive control measure. n Training – We bring together our suppliers to share food safety knowledge and c ommunicate expectations. Recalls: When we learn about illnesses that may be linked to our products, we take quick action. We collaborate with health officials to investigate the situation, communicate with customers and consumers, and issue voluntary recalls to remove affected products from store shelves, when appropriate. We conducted one small voluntary product r ecall globally in fiscal 2021 for soup, compared to two recalls in fiscal 2020. Food safety *These apply to our human and pet food products globally and cover a broad range of food safety areas, including regulatory compliance, trace and recall, labeling, claims, physical, chemical and biological hazards, transportation, and good manufacturing practices and sanitation. supplier and partner audits conducted, including 177 packaging audits, 567 human food ingredient audits, 32 pet food ingredient audits and 139 co- producer audits. GFSI certification:* 915 suppliers participated in food safety training sessions 550 *Includes Blue Buffalo pet food facilities. **Includes General Mills and Cereal Partners Worldwide (CPW) employees, suppliers, partners and co-producers. ***Includes corporate quality and supply chain professionals globally as of September 2021. *Includes human food co-production sites and suppliers. GFSI compliance numbers may fluctuate from year to year as new sites are added and other sites are removed based on changes in volume and ingredient requirements for new products, as well as delays in the issuing of certificates by certifying bodies, travel restrictions and other factors. people trained through global centers of excellence and online training academy** quality professionals trained in food safety*** inv ested into food safety, equal to 10.7% of total supply chain essential capital in v estment 4,750 862 $ 17.9 million of company-owned production facilities Global Food Saf ety Initiative (GFSI) certified* 96 % 100% GOAL 96 % GLOBAL CO-PRODUCTION SITES GLOBAL INGREDIENT SUPPLIERS NORTH AMERICAN INGREDIENT VENDOR SITES 93 % 85 % 97 % OUR PERFORMANCE OUR SUPPLIERS 2021 Progress GENERAL MILLS GLOBAL RESPONSIBILITY 09 Food Planet People Community
Our approach Our goal is to provide a diverse portfolio of products that contribute to the well-being of our consumers and meet a variety of their needs. We are committed to making food with passion and putting people first by improving the nutrient density, affordability, and accessibility of our products. At General Mills, we view nutrition as a source of growth and as a force for good. Our aspiration: We recognize the importance of our foods in consumers’ lives, and we provide a variety of foods that fit with our consumers’ budgets, time, tastes and nutritional needs. We understand the importance of sustainable food systems and the critical role the food industry can play in meeting these needs. We aspire to provide nutrient-dense foods that are made with ingredients grown using regenerative agricultural practices, that are affordable, easy to prepare and that the whole family loves. Learn more about our leadership in sustainable food systems and our sustainable sourcing practices in the Planet section of this report. Investment in research: We invest in research and development (R&D) to improve the nutrient density of our products and help us better understand the impact of food on health and wellness. We believe in cross-sector dialogue and diverse partnerships to advance nutrition research in support of public health. We collaborate with a range of scientists, universities, consortiums and organizations across the globe to advance nutrition science and help answer multifaceted nutrition problems. We are dedicated to discussing our policies and practices openly and transparently. Bell Institute of Health and Nutrition: General Mills’ global Bell Institute of Health and Nutrition is the company’s source for scientific health and nutrition expertise that creates value and growth for General Mills. The Bell Institute of Health and Nutrition is a team of scientists and registered dietitians who guide General Mills’ product development through: n Nutrition science research n Insights on nutrition claims and regulatory matters n Health communications to customers, nutrition professionals and consumers n Nutrition recommendations for product innovation and reformulation Learn more on the Bell Institute website . Leadership and governance: Responsibility for product development and marketing lies within the R&D and marketing organizations, respectively. Responsibility for marketing communications is held by the Chief Strategy and Growth Officer. The Chief Innovation, Technology and Quality Officer is responsible for the areas of product nutrition, safety and labeling. The Bell Institute of Health and Nutrition reports to the Chief Innovation, Technology and Quality Officer who approves the overall health and wellness strategy and updates the Public Responsibility Committee of the Board of Directors. Health and Wellness Advisory Council: Since 1989, our Health and Wellness Advisory Council of globally recognized external academic experts in health and nutrition meets regularly to provide feedback on our nutrition strategies and actions. Learn more about our Nutrition and Food Safety Partnerships and Collaborations. Nutrition policy: Globally, we engage transparently on nutrition policy topics through public engagement opportunities to provide evidence- based positions that support public health concepts like nutrient density, fortification, whole grain and healthy dietary patterns. For more information about where and how we engage on nutrition policy topics, please see the public policy content in the report’s Introduction section. Nutrition CHIEF INNOVATION, TECHNOLOGY AND QUALITY OFFICER HEALTH AND WELLNESS ADVISORY COUNCIL PRODUCT MARKETING AND COMMUNICATIONS FOOD SAFETY AND QUALITY RESEARCH AND DEVELOPMENT BELL INSTITUTE OF HEALTH AND NUTRITION CHIEF STRATEGY AND GROWTH OFFICER CEO, CHAIRMAN OF THE BOARD GENERAL MILLS GLOBAL RESPONSIBILITY 10 Food Planet People Community
Nutrient-dense foods Nutrient density is the contribution of positive nutrients and food groups, and nutrients to limit, per calorie. At General Mills, we provide a diverse portfolio of products, including many nutrient- dense foods, that can help consumers meet dietary recommendations and build healthy eating patterns. Focusing on nutrient density — rather than just what nutrients have been increased or reduced — can help best support consumers in adopting healthy dietary patterns. Nutrient-dense foods — like fortified whole grain cereals, low-fat and nonfat yogurts, granola bars, and frozen fruits and vegetables — play an important role in healthy diets. They are important contributors to consumption of key food groups, including whole grain, dairy, fruits and vegetables, nuts and seeds, and beneficial nutrients, like vitamins, minerals, protein and fiber, while balancing nutrients to limit, such as sodium, sugar and saturated fat. Fortification: We fortify key products in line with public health principles including using evidence-based decision-making to help guide the use of nutrients in our foods. General Mills periodically assesses population nutrient intakes using nationally representative dietary surveys to ensure our products help meet consumer dietary needs. Affordable and accessible: We believe in providing affordable, accessible nutrient-dense foods that people love. We do this in a variety of ways, including offering nutrient-dense products, like ready-to-eat cereal and yogurt, that meet the nutrition guidelines for U.S. federal nutrition assistance programs, such as the Special Supplemental Nutrition Program for Women, Infants, and Children (WIC) , the Child and Adult Care Food Program (CACFP) , the School Breakfast Program (SBP) and the National School Lunch Program (NSLP) . Through our philanthropic partnerships and tied to our company’s purpose, we are committed to building food- secure communities. Examples include enabling 30 billion meals to be provided for hungry people by 2030, increasing reliable food access for 10 million people struggling with food insecurity by 2030 and investing to expand the capability of food bank networks globally. Learn more about how we are increasing food security by expanding food access for families in need and alleviating hunger in the Community section of this report. + + Plus up the nutrition of affordable, convenient family favorites School meals During the COVID-19 pandemic, General Mills has supported schools with grab-and- go solutions, such as whole grain–rich cereals in bowlpaks and cups and individually wrapped whole grain–rich pancakes and waffles. We also accelerated new product innovation for grab-and-go feeding programs, including the introduction of Nature Valley whole grain rounds with 32 grams of whole grain. v Blueberry and Rice Chex in a convenient portable cup is a whole grain–rich, gluten-free cereal with at least 18 grams of whole grain per cup and meets CACFP sugar requirements. v Whole grain– rich Nature Valley Oatmeal Rounds deliver 32 grams of whole grain. General Mills provides meal ideas on bellinstitute.com focused on nutrient density, affordability and convenience for a variety of our products. For example, Old El Paso Taco Dinner Kit s act as a nutritious and convenient carrier for lean meat, low-fat dairy and vegetables, while Progresso soup can easily be paired with fruit, side salad and a glass of milk for an easy and satisfying meal. Adding nutrient-dense vegetables to a box of Hamburger Helper helps stretch food dollars and saves time in the kitchen — by adding lean protein and vegetables, consumers can easily prepare a filling and nutritious dinner for the entire family. Hamburger Helper + 1/2 lb. of lean ground beef 1 cup of black beans, drained and rinsed 2 cups of milk Paired with a side salad 1 cup of frozen peas, thawed + + GENERAL MILLS GLOBAL RESPONSIBILITY 11 Food Planet People Community v On average, a serving of Yoplait Original yogurt is 60 cents and provides an excellent source of calcium and good source of vitamin D.
Food Planet People Community Global health reporting Over the years, we have made significant progress reformulating products by increasing positive nutrients, like whole grain, fiber and iron, and reducing limiters, like sodium and sugar. From fiscal 2005 to 2018, we tracked and shared our progress through our U.S. Health Metric reporting system, whereby we improved the nutrition of our U.S. retail sales volume by 81% primarily by increasing positive nutrients or decreasing nutrients to limit. In fiscal 2019, we updated and expanded our approach to a new global health reporting system that provides a transparent snapshot of the nutritional characteristics of our global portfolio. The process for determining which products qualify as Nutrition-Forward Foods is based on established nutrition criteria grounded in regulations, dietary guidance and nutrient density. Results: In fiscal 2021, 41% of General Mills global volume met our Nutrition- Forward criteria, including 22% that met the criteria by providing a meaningful amount of a food group and 19% that met the U.S. Food and Drug Administration’s Healthy criteria through limits on sodium and saturated fat. Our expansive and diverse portfolio offers a delicious variety of nutrient-dense products from every food group to help support consumers in building healthy eating patterns. *Global Health Reporting excludes our Pet segment. **Nutrition-Forward Foods must meet the following criteria per labeled serving: n At least 8 grams of whole grain, a ½ serving of low-fat or nonfat dairy per regional definition, or a ½ serving of fruits, vegetables or nuts/seeds. (22% met these criteria.) — or — n Meet U.S. Food and Drug Administration’s Healthy criteria: 21 Code of Federal Regulations 101.65. (19% met these criteria.) In fiscal 2021, 41% of General Mills global volume met the Nutrition- Forward criteria.** GLOBAL HEALTH REPORTING * Examples of General Mills Nutrition-Forward Foods from key product categories PRODUCT CATEGORY Whole grain cereals Low-fat or nonfat yogurts Snack bars Soups Fruits and vegetables FEATURED PRODUCTS Big G cereals like Original Cheerios, Kix, Fiber One, Chex and Wheaties Yoplait yogurts like Yoplait Original, Light, Source, Panier Standard, and Go-GURT Nature Valley Crunchy Bars, Fiber One Chewy Bars Oats and Chocolate, and Annie’s Chewy Granola Bars Oatmeal Raisin Progresso soups like Reduced Sodium Hearty Minestrone and Light Vegetable & Noodle Soup A variety of Cascadian Farm frozen fruits and vegetables, Muir Glen tomatoes, Betty Crocker potatoes, a variety of Progresso canned beans NUTRITION- FORWARD CRITERIA Provides at least 8 grams of whole grain per labeled serving Provides at least ½ serving of low-fat or nonfat dairy per regional definition Provides at least 8 grams of whole grain per labeled serving OR ½ serving of nuts or seeds Meets U.S. FDA Healthy criteria OR provides ½ serving fruits/vegetables per labeled serving Provides at least ½ serving of vegetables/ fruit per labeled serving IMPACT Over 99% of our cereal portfolio provides at least 8 grams of whole grain per labeled serving 58% of our yogurt portfolio provides at least ½ serving of low or nonfat dairy 75% of our snack bar portfolio provides at least 8 grams of whole grain OR ½ serving of nuts or seeds 51% of our soup portfolio meets FDA Healthy criteria OR provides ½ serving fruits/vegetables per labeled serving 97% of our vegetable portfolio provides at least ½ serving fruits/vegetables per labeled serving 2021 Results 41 % *Per labeled serving. GENERAL MILLS GLOBAL RESPONSIBILITY 12 of our cereal portfolio provides at least 8 grams of whole grain* 99 %
Many Americans fall short on calcium and vitamin D in their diet. To help address this gap, most flavors of Original Style Yoplait were reformulated to provide an excellent source of calcium and a good source of vitamin D. The nutrition profile of Light Style Yoplait also underwent a change. Yoplait Light yogurts now provide 80 calories, 7 grams total sugar and 1 gram of added sugar (down from 90 calories, 10 grams total sugar and 4 grams of added sugar). In Mexico, we reduced added sugar by 78% in our Nature Valley Fruteria snack bar and added 13 grams of fiber per 100 grams. With this formulation improvement, whole grain oats are now the first ingredient. Product reformulation highlights Sustainable diets The World Health Organization has identified Sustainable Healthy Diets as dietary patterns that promote an individual’s health and well-being; have low environmental pressure and impact; are accessible, affordable, safe and equitable; and are culturally acceptable. General Mills supports this perspective, and we are focused on providing nutrient-dense foods that contribute healthful ingredients, including whole grains and low-fat dairy, to the diet. We also invest in regenerative agriculture to reduce environmental impact, restore soil health, and support farming communities. Our packaging team continually explores renewable materials and new opportunities to reduce packaging while keeping foods fresh. Learn more about how General Mills supports regenerative agriculture and works to reduce the environmental impacts of food packaging in the Planet section of this report. Personalized nutrition As consumers’ desire for personalized nutrition expands, General Mills is working to provide innovative offerings. Our diverse portfolio includes many products designed to meet the evolving preferences of consumers who choose their foods with specific nutrition and lifestyle goals in mind. Examples include: n Carb-conscious – Our Ratio brand extended its keto-friendly product offerings to include dairy snacks and soft bakes with net carbs in mind. Good Measure offers snack bars — convenient snack solutions that provide fiber and nuts and have 5 grams or less of net carbs — as an occasional snack for consumers interested in limiting their carbohydrate consumption. Wonderworks is the newest cereal brand from General Mills, with 3 grams of net carbs and 17 grams of protein per serving. n Weight management – Fiber One bars and brownies are smart choices for consumers looking for tasty ways to enjoy their favorite snacks while managing their weight. Our Yoplait Light brand has been a calorie-controlled yogurt for years and was recently reformulated to have less sugar and fewer calories. n Heart-healthy – Cheerios Original and Honey Nut Cheerios , staples in many households, are made from whole grain oats, which contain beta-glucan, a soluble fiber that can help lower cholesterol as part of a heart-healthy diet. n Gluten-free – We offer many gluten- free products. General Mills is the third-largest producer of gluten-free products in the U.S.* More than one in four of our North American product SKUs are labeled as gluten-free.** *Nielsen xAOC; 52 weeks ending 12/25/2021. **As of November 2021. GENERAL MILLS GLOBAL RESPONSIBILITY 13 Food Planet People Community r Our products designed to meet the needs of carb-conscious consumers include Ratio keto- friendly yogurt, Wonderworks cereal and Good Measure snack bars. r Old El Paso gluten-free tortillas
Cereal Partners Worldwide Our Cereal Partners Worldwide (CPW) joint venture with Nestlé makes and markets cereals globally outside North America. CPW is committed to making breakfast better by providing nutritious, tasty and convenient breakfast cereals. For more than a decade, CPW has been improving the nutrient density of its global product portfolio to increase beneficial ingredients and nutrients that are important to a balanced diet — such as whole grain and fiber — and reduce ingredients like sugar and sodium. Actions: Since 2003, CPW has increased the use of whole grains by 50%. Along with international health organizations, industry peers and other partners, CPW and General Mills participate in the Whole Grain Initiative , a global effort to increase consumer awareness of the importance of whole grains and promote greater consumption of them. With the initiative, CPW and General Mills support the annual International Whole Grain Day each November to encourage consumption of whole grains worldwide. Results: * n 100% of CPW breakfast cereals that carry the green banner are made with a minimum of 8 grams of whole grain. n 99% of CPW cereals and bars meet the Codex requirement for being a source of fiber. n 95% of CPW cereals and bars have less than 450 milligrams of sodium per 100 grams. n 76% of CPW cereals and bars have less than or equal to 2 teaspoons of sugar (7.5 grams) per serving. *Based on data for January to December 2021. Our approach: Today’s fast-changing food landscape requires rapid innovation and a steady stream of new ideas. General Mills has been a leader in food innovations throughout our history, dating back to advances in milling technology more than 150 years ago. Today, we invest in food innovations through 301 INC, the venture capital arm of General Mills, and through G-Works, our corporate venture studio. Looking ahead, we are building food solutions for tomorrow’s families by focusing on disruptive growth opportunities that extend beyond launching and supporting emerging food brands to consider not only what we offer, but also how we serve consumers. We are exploring new ways to build, invest and partner to create the next growth engine for General Mills and deliver innovative food solutions that solve consumer problems. Highlights of our progress during 2021 are listed below. 301 INC partners with entrepreneurs to accelerate their growth by nurturing the skills of founders and providing access to a team of General Mills functional experts across marketing, sales, operations and R&D who serve as partners to the brand teams, helping them to meet the evolving needs of consumers faster than ever. In fiscal 2021, we continued to grow our 301 INC portfolio and support for entrepreneurial brands. G-Works is changing the way the company innovates. The group started in 2019 within our North America Retail segment and includes several small, nimble teams focused on a transformational business, trend or project related to solving a consumer need. G-Works launched several new brands in fiscal 2021, including: n Good Measure nutrient-dense products with little impact on blood sugar n Bold Cultr cheese alternative made using a precision fermentation process n Doolies products — smoothies, bites and bars made with fruits that are good for digestion and naturally occurring fiber — support a healthy digestive system to help kids avoid constipation Investing in food innovations 301 INC partners As of December 2021, we have 9 partners. GENERAL MILLS GLOBAL RESPONSIBILITY 14 Food Planet People Community r Good Measure, Bold Cultr and Doolies are three new brands launched in 2021. v Outside of North America, Cheerios is available in selected markets worldwide through CPW.
Our business depends on a healthy planet, so it is imperative that we continue to seek ways to care for it. Since 2000, we have steadily expanded our natural and organic business to meet growing consumer demand and embed sustainability across our product portfolio. Natural and organic brands: We offer a mix of certified organic cereals, yogurt, frozen fruit and vegetables, snacks, meals and baking products. One in eight products in our North American portfolio is certified organic or made with organic ingredients.* While each of these brands is unique, they all strive to accelerate work in regenerative agriculture and to advance leading-edge sustainability programs that can be leveraged throughout General Mills. Learn more in the Planet section of this report about the steps we are taking across our supply chain to build our organic capacity and expand regenerative agriculture practices. Plant-based and vegan products: Consumers seek plant-based foods for environmental, social and nutritional reasons. Our portfolio has long been plant-based, with flour, breakfast cereals, snack bars, soups and frozen fruits and vegetables. More than 800 of our products are vegan,* including Dairy-Free Go-Gurt , most Lärabar products, Annie’s fruit snacks and Annie’s Organic Vegan Mac . In the yogurt aisle, Oui by Yoplait and Liberté Dairy Free (available in Canada) are plant- based alternatives. Cascadian Farm brings plant-based protein to granola bars and frozen vegetable blends. Through our business development and venture capital unit, 301 INC , we invest in new brands, including many that are plant-based, such as Rhythm Superfoods, maker of nutrient-dense snacks containing vegetables, fruits and seeds, and Kite Hill, maker of almond- based non-dairy products. Learn more about our investments in food innovations on p. 14. Long part of our company’s story, plant-based foods are an exciting part of General Mills’ future. Natural pet food: Blue Buffalo has become the leading natural pet food brand in the U.S. by feeding pets like family members. Blue Buffalo is made with high quality, natural ingredients with real meat as the first ingredient and never any corn, wheat, soy, poultry by-product meals, artificial flavors or preservatives. The promise to “Love them Like Family. Feed them Like Family.” guides everything Blue Buffalo does — from industry-leading standards for sourcing ingredients to state-of-the-art manufacturing facilities to philanthropic initiatives, like supporting pet cancer awareness. Meeting consumers’ desire for natural, organic and plant-based foods *As of November 2021. Does not include pet food products. GENERAL MILLS GLOBAL RESPONSIBILITY 15 Food Planet People Community r Vegan Dairy-Free Go-Gurt We are working to help make our natural and organic foods more accessible to all consumers wherever they shop — whether that’s in a grocery store, convenience store, dollar store or online — and at a price point they can afford. Learn more about our work to expand food access for families in need and alleviate hunger in the Community section of this report. Our natural and organic brands ® ® Increasing access v Annie’s is dedicated to using superior ingredients — including real cheese, organic pasta and other natural and organic ingredients that are sustainably grown — to deliver great taste so kids will want to eat them. r Cascadian Farm offers a variety of plant-based products. General Mills is the largest provider of natural and organic packaged food in the U.S.* # 1 *Includes food for both humans and pets. Source: SPINS 52 WE 12/26/2021, Total — US Mulo, Natural Enhanced Channel and Pet Channel. v Blue Buffalo has more foods for specific breed sizes and life stages than any other natural pet food brand, so pet parents are sure to find the right option for their dogs and cats.
Our approach: Whether marketing to children or adults, we present the qualities and advantages of our products truthfully, responsibly and with appropriate taste. We take special care with respect to child audiences. We believe that children should be encouraged to consume lower-calorie, nutrient-dense foods that support their growth and activity. Learn more about our commitment to maintain the highest standards for responsible marketing. We adhere to strict internal and industry guidelines — often more demanding than local regulations — in producing and reviewing ads to ensure they are appropriate for the intended audience. Beyond complying with applicable law, we ensure that our ads are consistent with our core values. When possible, our advertising aims to reflect the diversity of society. And our advertising reflects generally accepted standards of social behavior, avoids stereotyping people and never insults or demeans any demographic groups. Policies: General Mills marketing policies ensure that our commitment to responsible marketing underlies all of our marketing activities. Responsible marketing Our approach: General Mills provides useful, fact-based information on packages to help consumers make informed dietary choices. All of our product packages display accurate nutrition labeling and follow relevant nutrition and health claim requirements as prescribed by regulations in the country of sale. Our commitment: As a member of the International Food and Beverage Alliance (IFBA), General Mills has made a commitment to adopt a common global approach to nutrition information on packaging that includes, at minimum, the labeling of calories on front-of-pack. This initiative was implemented globally during 2014-2016 to inform consumers about specific product nutrition attributes. In countries with front-of- pack labelling requirements, we adhere exclusively to the local regulation. We also commit not to place any regulated health or nutrition claim on a product unless it meets the criteria set forth by the regulations in the country of sale. Our progress: Around the world, our product labeling meets local regulatory requirements while remaining consistent with our global approach. Examples of our compliance with local and regional guidelines include: n Australia – 100% of our products display nutrition intake information in front-of-pack labeling, consistent with the Australian Daily Intake Guide and IFBA requirements. n Brazil – All General Mills package information complies with local regulations and includes the energy icon on the front of packaging. n Mexico – All General Mills package information complies with local regulations and includes front-of-pack consumer information as directed by the Mexican Health Ministry. n China – All General Mills package information complies with local regulations and includes the energy icon on the front of packaging. n Canada – All General Mills package information complies with Health Canada and Canadian Food Inspection Agency labeling requirements. n Europe – All General Mills package information complies with European Food Information to Consumers Regulation . n United States – The majority of our U.S. products feature front- of-package labeling through the Facts-up-Front program. Consumer education and marketing Consumer education GENERAL MILLS GLOBAL RESPONSIBILITY 16 Food Planet People Community In the U.S., General Mills supports product labeling changes to help reduce food waste through clearer guidance for consumers about food shelf life. We have updated all of our U.S. product packaging to comply with this voluntary date-labeling initiative that uses standard nomenclature to reduce consumer confusion. Learn more about General Mills’ food waste reduction efforts in the Planet and Community sections of this report. Date labeling of our U.S. packaging contains updated date labeling to help reduce food waste.* *As of November 2021 100 %
Governance: General Mills marketing policies are reviewed and updated regularly by our company’s Responsible Marketing Council and reviewed with the company’s Chief Executive Officer and other senior leaders of our U.S. and international operating units. The Responsible Marketing Council is responsible for drafting and issuing marketing policies, ensuring full compliance with the policies through training and initiatives, and holding advisory reviews of all new product development and brand marketing plans for products that will be marketed to children. Global commitment: As charter members of IFBA, we joined other leading food and nonalcoholic beverage companies in a public letter to the Director General of the UN’s World Health Organization in September 2014 communicating a set of enhanced global commitments that included responsible marketing and advertising initiatives. The enhanced commitments included an expansion of IFBA’s global marketing policy to cover all forms of child-directed advertising, specifying that members would only advertise products that meet better-for-you criteria or refrain from all product marketing to children under 12 years old. In 2021, we joined with other IFBA members to announce further enhancements to the IFBA program, which will now address marketing to children under age 13 (instead of age 12) and require adherence to globally applicable nutrition criteria. These new IFBA criteria now serve as a global gap- filler, governing child marketing around the world by providing robust nutrition criteria even in markets where local or self-regulatory standards do not exist. At General Mills, we commit to adhere not only to the new IFBA criteria in these global markets, but we also renew our longstanding commitment to follow the U.S. Children’s Food and Beverage Advertising Initiative (CFBAI) criteria in these markets. In other words, we have long covered the whole world with our commitment, historically via CFBAI standards and now with both CFBAI and IFBA. We have also now expanded our commitment by announcing that we will adhere globally to the requirements of the International Chamber of Commerce Framework for Responsible Food and Beverage Marketing Communications. Aside from these global commitments, at local levels we fully comply with the applicable local programs, including the EU Pledge in Europe, CAI in Canada and CFBAI in the U.S.* Our compliance track record with these programs is extraordinarily strong. CFBAI, in particular, publishes a report annually that addresses the compliance of all of its participants. We are not aware of any instance of noncompliance by General Mills in the past several years, and CFBAI has confirmed this in its reports. In the unlikely event of any instance of noncompliance, a core function of our Responsible Marketing Council would be to address such issues and determine appropriate corrective action. Beyond our commitments under the programs noted above, we have made additional responsible marketing commitments that exceed industry norms. For example, we have adopted industry-leading standards regarding the responsible use of social media platforms. We do not, in the context of any child-directed communication, encourage children to visit any social media service for which they are too young (according to the terms of those services), nor do we use our own presence on these social media platforms to direct any communications to children. We have also long committed to refrain from marketing food to children in schools or at school events — and this commitment applies to all schools, even middle schools and high schools. This commitment covers all forms of marketing (beyond the identification of the brand and product on menus and packaging). For example, we do not depict or display food brands, products or logos on posters, signs, scoreboards or school equipment, nor do we market foods by distributing product samples or branded merchandise in schools. There are no exceptions to this commitment. In the U.S., we operate the Box Tops for Education™ school fundraising program which, through sales of our products and those of many other companies (primarily nonfood companies), has provided close to US$1 billion to schools since the program’s inception in 1996. Though schools are the beneficiaries of this program, we refrain from marketing the program to school children (whether inside or outside the school environment). *Other locally applicable programs include: Australia — Responsible Child Marketing Initiative of the Australian Food and Grocery Council ; Brazil — Enhanced Commitment to Responsible Advertising to Children pledge; Singapore — Singapore Food and Beverage Industry Responsible Advertising to Children Initiative . v General Mills joined other food and beverage companies in signing a letter to the UN Secretary General in September 2018 highlighting commitments and achievements to reduce the burden of noncommunicable diseases in support of UN Sustainable Development Goal 3.4. We collect and use consumer personal data for a variety of purposes, including to provide recipe-related publications to consumers who subscribe for these, to run sweepstakes and contests, to ensure that our advertising is directed to relevant audiences, and to otherwise improve our product and service offerings. We are sensitive to the privacy concerns of our consumers and are fully committed to complying with regulations, including the EU General Data Protection Regulation (GDPR) and the California Consumer Privacy Act. In addition to meeting changing legal requirements in this area, General Mills is committed to acting responsibly and transparently to continue to earn and maintain the trust of our consumers with respect to our collection, retention and use of personal data. We also maintain safeguards to control against the loss of personal data or the unauthorized access, use, disclosure, destruction or modification of personal data. Learn more in our data privacy policy .* Data privacy *Links to main U.S. policy as an example. General Mills has additional privacy policies specific to other parts of our business globally. GENERAL MILLS GLOBAL RESPONSIBILITY 17 Food Planet People Community
Our approach: At General Mills, we are committed to increasing transparency about our food. We recognize that consumers, regulators, investors and other stakeholders seek information about our products and processes. Consumers want to know what’s in their food, where it comes from and how it is prepared. They also want assurance that food has been grown and harvested in a responsible and sustainable manner that respects people, animals and the environment. We continue to increase transparency by providing information to key stakeholders when and where they need it. For example, to help consumers learn more about what is in their food, we provide information in multiple ways — on packages, through our company and brand websites, on our brands’ social media channels and on third-party sites, such as e-commerce and transparency platforms. In addition, we actively support public policy efforts to inform consumers and increase their a wareness about our products — these efforts are detailed in the Introduction section of this report. Our actions: Some examples of our current transparency initiatives are outlined here. n To provide transparency about the way our ingredients are grown, we feature details on product packaging, including some of our Annie’s macaroni and cheese boxes, Food Should Taste Good tortilla chip packages and EPIC beef bars. n We provide consumers with answers to questions about our food at askgeneralmills.com . Topics range from food ingredients to gluten- free products and use of genetically modified organisms (GMOs). More than 72,000 users visited the web site during fiscal 2021. n In the U.S., we provide product details through SmartLabel™ , an industry initiative that seeks to share digital product information with consumers. We also enroll products — especially our organic products — in the U.S. Non- GMO Project , a nonprofit organization that provides information to consumers and third-party verification for non-GMO food and products. Sustainable sourcing: We are committed to sustainable sourcing of the ingredients used in our products and we regularly share information about our progress. For example, we disclose an updated list of all our palm oil suppliers down to the mill level to facilitate transparency and accountability in our extended supply chain. Details about our ingredients, how they are sourced and how we engage with farmers are included in the sustainable sourcing content in the Planet section of this report. Biotechnology: Safety is our highest priority, and we find broad global consensus among food and safety regulatory bodies that approved GMOs are safe. We agree with the UN’s World Health Organization (WHO) that the development of GMOs offers the potential for increased agricultural productivity and improved nutritional value that can enhance human health and development. We have been disclosing the presence of bioengineered ingredients on our U.S. packages since 2016. Pesticide use: We recognize that some consumers and stakeholders have concerns about the use of pesticides. General Mills maintains a comprehensive system of controls and processes to ensure the highest level of product quality and safety. We also work to reduce the need for synthetic pesticides in agriculture. We detail our work in this area on our comprehensive Pesticide, food safety and ecosystems health web page . Transparency *As of November 2021 TRANSPARENCY products listed on smartlabel.org* products enrolled in the U.S. Non-GMO Project topics covered on askgeneralmills.com 1,940 459 324 2021 Progress GENERAL MILLS GLOBAL RESPONSIBILITY 18 Food Planet People Community In 2021, we introduced our limited-edition Cascadian Farm Climate Smart Kernza Grains Cereal in Whole Foods stores. The cereal is made with Kernza® sourced through our partnership with The Land Institute. We have been working together to scale up the supply of organic Kernza since 2017 because of this perennial grain’s deep roots, which increase soil health and drought resistance, prevent erosion and store critical nutrients — along with carbon — in the soil. The environmental benefits of Kernza grains are highlighted on the cereal packaging. Highlighting the environmental benefits of Kernza grains
renewable electricity sourced for our global operations of General Mills packaging recyclable or reusable (by weight) 63 % 89 % Our goal is to create resilience for people, the planet and our business. Climate change n Ingredient sourcing n Eliminating deforestation Regenerative agriculture n Water stewardship n Packaging Sustainable operations n Responsible sourcing n Animal welfare IN THIS SECTION Planet acres enrolled in programs advancing regenerative management 115,000 GENERAL MILLS GLOBAL RESPONSIBILITY 19
At General Mills, we are thinking and leading differently, unleashing our scale and driving systemic change for the better. A decade ago, our main planet initiatives and commitments focused on sustainability. But in order to make food for future generations, simply sustaining the current state of ecosystems and communities is not enough. We need to work in a manner that regenerates the Earth’s resources. Over the last several years, we have gained many insights from our sustainable sourcing and climate programs. We understand we must take a more integrated, systemic approach to unlock the tremendous opportunity of enhanced food system resilience. We believe that regenerative agriculture is the most critical solution to deliver on our greenhouse gas commitments and to create positive outcomes for people, planet and communities. So we’ve taken the lead in this space within our industry, partnering with farmers, advancing the science and measuring outcomes. But we have a lot of work to do. Changes in agriculture take time, especially as we’re building a program that is grounded in measurable outcomes and new science and technology. For the first time in many years, our greenhouse gas emissions actually increased in fiscal 2021 as our company produced more food in order to help feed the world during the global pandemic. We will need the help of our partners, both upstream and downstream, to advance our progress as our company cannot do it alone. We recognize the need to accelerate our decarbonization, so we have evolved our Global Impact governance structure to include General Mills’ executives from the business and all key functions, enabling better integration, prioritization, resourcing and operationalization of key global impact priorities. We have also invested time and focus in developing a recommended new operating model that creates cross- functional integration, investment and accountability in reaching our shared goals. We know we need to drive systemic change if we aim to hit our goals, and we believe these new structures will help to accelerate progress toward our ambitions. Thank you for your interest in our work to help create a more resilient planet. Sincerely, Mary Jane From our Chief Sustainability and Global Impact Officer Mary Jane Melendez Chief Sustainability and Global Impact Officer General Mills GENERAL MILLS GLOBAL RESPONSIBILITY 20 Food Planet People Community Greenhouse gas Reduce value chain greenhouse gas emissions by 30% by 2030 Food waste Reduce food waste in our operations by 50% by 2030 Regenerative agriculture Advance regenerative agriculture on 1 million acres of farmland by 2030 Zero waste to landfill Achieve zero waste to landfill at all owned production facilities by 2025 Packaging General Mills brands will design 100% of packaging to be recyclable or reusable by 2030 (by weight) Animal welfare Purchase 100% cage-free or free- range eggs for our global operations by 2025 Water Champion activation of water stewardship plans for the most at-risk watersheds by 2025 Human rights Assess and address our human rights impacts in alignment with the United Nations Guiding Principles on Business and Human Rights Renewable electricity Source 100% renewable electricity for our global operations by 2030 GHG F21 progress: 2% increase vs 2020 baseline F21 progress: 24% reduction vs 2020 baseline F21 progress: 115,000 acres enrolled in programs advancing regenerative management F21 progress: 28% achieved F21 progress: 89% achieved 2021 progress*: 61% contracted *Cage-free egg progress based on calendar year 2021 F21 progress: 3 of our 10 priority watersheds have active water stewardship plans in place F21 progress: ongoing F21 progress: 63% achieved Commitments and fiscal 2021 progress
United Nations Sustainable Development Goals: General Mills supports the United Nations (UN) Sustainable Development Goals (SDGs), a set of 17 broad goals and 169 more- specific targets to drive the 2030 Agenda for Sustainable Development globally. We focus on the goals that most closely align with the company’s priority issues and areas of long-standing commitment, investment and progress. Leadership and governance: The Global Impact Governance Committee (GIGC), led by our Chairman and CEO and overseen by the Board’s Public Responsibility committee, is accountable for our sustainability program. The Chairman and CEO convenes the GIGC at least three times each year to establish, direct and oversee General Mills’ positions on matters of significance to the company and its stakeholders concerning corporate social responsibility, environmental and sustainability issues, and philanthropy. These matters are included in our Chairman and CEO’s annual performance objectives and impact his compensation. The GIGC, which was formalized in 2021, is an evolution from the previous Sustainability Governance Committee and reflects the continued integration of sustainability into the company and the understanding that our ambitious targets will require alignment, operationalization and investment across the company. Further oversight of the company’s sustainability work is provided by the Board’s Public Responsibility Committee, which regularly reviews the company’s sustainability objectives, strategies and performance. The company’s Chief Sustainability and Global Impact Officer stewards the company’s sustainability work, reporting to the Chief Strategy and Growth Officer, and working closely with other key business leaders to develop, coordinate and execute programs to achieve company-wide targets. Public policy: We actively engage in public policy discussions to advance our environmental initiatives, including: n Leading on regenerative agriculture n Combating climate change n Advancing water stewardship n Addressing packaging and food waste Learn more in the Introduction section of this report. r General Mills helps to address these United Nations Sustainable Development Goals through the programs and performance described in this section. Board of Directors’ Public Responsibility Committee Chief Strategy and Growth Officer Chief Supply Chain Officer Global Impact Governance Committee CEO , Chairman of the Board Chief Financial Officer Chief Supply Chain Officer Chief Innovation, Technology and Quality Officer Chief Strategy and Growth Officer Chief Human Resources Officer Group President, North American Retail Chief Communications Officer General Counsel and Secretary VP, Chief Sustainability and Global Impact Officer VP, Global Sourcing VPs, Supply Chain CEO, Chairman of the Board General Mills is recognized as a global leader in sustainability * CDP Disclosure A List 2021 – Climate Change CDP Disclosure A List 2021 – Water Security 100 Bes t Corporate Citizens 2021 – 3BL Media Member FTSE4Good Member of Dow Jones Sustainability North America and World Indices The Just 100 2021 - Just Capital and CNBC America’s Most Responsible Companies 2021 – Newsweek *Recognitions as of December 2021. r In September 2021, several members of the Global Impact Governance Committee and a group of employees across the company traveled to Stoney Creek Farm in Redwood Falls, Minn. to learn firsthand more about the importance of soil health and the benefits of regenerative agriculture. GENERAL MILLS GLOBAL RESPONSIBILITY 21 Food Planet People Community
At General Mills, our business depends on the health and resilience of our planet and its natural resources. We take the outputs of Mother Nature and turn them into great tasting products that help feed people around the world. But we are experiencing increased frequency, intensity and duration of extreme weather events that affect global food security and impact our ability to deliver quality products to our consumers. We need to take action now to help maintain planetary health. As a global food producer, we have a responsibility to leverage our scale and influence to combat the devastating impacts of climate change — and to lead others to do so as well. Our General Mills Policy on Climate , which focuses on mitigation, adaptation, disclosure and advocacy, establishes our company’s framework to track and reduce greenhouse gas (GHG) emissions across our value chain. Collaboration: We directly control only a small portion of our value chain, so driving transformation across the entire system requires leadership and collaboration with suppliers, farmers, ingredient and packaging producers, product transport providers, retailers and consumers. Combating climate change also requires collective action across industries and our broader society. We participate in the following initiatives: n Science Based Targets initiative (SBTi) n Business Ambition for 1.5°C n We Mean Business n We Are All In pledge n UN Caring for Climate Declaration n Business for Nature’s Call to Action n Climate Collaborative n Project Drawdown Science-based goal: General Mills was the first company to publish a full value chain goal approved by the SBTi, in 2015. During 2020, we launched a new climate goal to drive further progress, in alignment with the SBTi 1.5°C guidance. General Mills will reduce absolute GHG emissions across our full value chain* by 30% by 2030 (compared to 2020). By 2050, we will achieve net zero GHG emissions across our full value chain. Fiscal 2021 progress: In fiscal 2021, our absolute GHG emissions footprint increased 2% compared to our fiscal 2020 baseline. This reflects business growth during the year as General Mills increased production to make food the world needed during the pandemic and company-wide net sales increased 3%. Almost all parts of our value chain saw an increase in emissions (see value chain breakdown on next page). See the Appendix for additional details on our GHG emissions and calculation methodology. Looking ahead: Recognizing the need to accelerate our progress in reducing emissions, General Mills is working to advance our internal carbon focus from footprint accounting to decarbonization strategies and execution. We are starting to staff internal teams to build internal glidepaths for carbon reduction and investing in external support to bring in capabilities of carbon abatement, quantification, and training. We also have work in process to begin engaging with suppliers in key categories to encourage them on their decarbonization journey, including setting targets and developing carbon abatement strategies. Climate change The path to 2050 2020 2030 2050 0 15 10 5 13.9 13.5 9.4 13.3 9.0 2021 0 0.6 0.7 0.4 12.8 Million metric tons CO 2 e Total General Mills Scope 1 + 2 (market-based) Scope 3 *Consistent with Science Based Target Initiative (SBTi) guidelines, our goal focuses on the categories of GHG emissions that are the most impactful and actionable for General Mills (approximately 77% of our total value chain footprint in FY21). It excludes emissions such as low-volume ingredients, capital goods, employee commuting, franchises, downstream warehouse and storage at retail, consumer trips to store and end of life (consumer food waste). GHG emissions: goal and progress 2030 SBTi target 2020 baseline* 2021 results* % change Total General Mills -30% 13.5 13.9 +2% Scope 1 + 2 (market- based)** -42% 0.7 0.6 -25% Scope 3 -30% 12.8 13.3 +4% *Emissions noted in million MT CO 2 e **Market-based Scope 2 reporting considers any contractual instruments that may be used in competitive energy markets, such as green tariffs, renewable certificates, or PPAs. GENERAL MILLS GLOBAL RESPONSIBILITY 22 Food Planet People Community
*Percentages next to each phase represent the portion of General Mills’ fiscal 2021 science-based target footprint value chain GHG emissions **Wheat, dry corn, oats, sugar beets *** Cocoa, soybean oil and sugarcane represent nearly half of Other CONSUMING (12%) SELLING (1%) SHIPPING (14%) KEY DRIVERS WAREHOUSE 3% TRUCK 75% OTHER MODES 22% PRODUCING (6%) KEY DRIVERS FUEL 50% 36% ELECTRICITY 14% OTHER PACKAGING SUPPLY CHAIN (10%) KEY DRIVERS METAL 33% FIBER 41% OTHER 4% PLASTIC 22% AGRICULTURE AND TRANSFORMATION (57%) KEY DRIVERS DAIRY 28% ROW CROPS** 33% MEAT 20% 19% OTHER*** EMISSIONS (MILLION METRIC TONS CO 2 E) GHG emissions across the value chain * KEY DRIVERS BUSINESS TRAVEL 15% HÄAGEN-DAZS SHOPS 35% OFFICE BUILDINGS 50% KEY DRIVERS HOME COOKING 60% HOME STORAGE 19% END OF LIFE 19% COMMERCIAL BAKING 2% EMISSIONS (MILLION METRIC TONS CO 2 E) 0.08 0.10 2021 2020 EMISSIONS (MILLION METRIC TONS CO 2 E) 1.87 1.71 2021 2020 EMISSIONS (MILLION METRIC TONS CO 2 E) 1.72 1.70 2021 2020 EMISSIONS (MILLION METRIC TONS CO 2 E) 0.86 1.03 2021 2020 EMISSIONS (MILLION METRIC TONS CO 2 E) 1.37 1.40 2021 2020 2021 2020 7. 9 2 7.64 As agriculture drives our largest climate impact, we must adapt farming practices to reduce land-based emissions. Drive emission reductions across all aspects of dairy operations and value chains, including animal feed, enteric emissions, manure, and on-farm energy. Advance work to eliminate deforestation in supply chains across select high-risk ingredient categories. Achieve energy usage reductions and identify efficiency opportunities at General Mills owned production facilities. Source renewable electricity for 100% of General Mills owned operations globally and evaluate external supply chain opportunities. Work with transport carriers to leverage more GHG-efficient equipment, shift to lower- GHG transport modes, optimize truck fill rates and reduce empty miles. Optimize manufacturing processes to reduce waste of ingredients, limiting agricultural emissions and waste. Our goals for 2030 and 2050 are aggressive, but needed, to achieve a stable climate. In order for General Mills to hit these targets, we need to collaborate across our value chain and drive systemic change. We have developed a multipronged strategy to enable General Mills to reduce greenhouse gas emissions. DAIRY Key levers to achieving our climate commitment REGENERATIVE AGRICULTURE ENERGY EFFICIENCY FOOD WAST E TRANSPORTATION EFFICIENCY RENEWABLES ELIMINATING DEFORESTATION GHG GENERAL MILLS GLOBAL RESPONSIBILITY 23 Food Planet People Community
Risk management Climate change is included as a risk in our company-wide Enterprise Risk Management (ERM) process. To better understand our climate risk, in 2020 General Mills commissioned Trucost/S&P Global to assess its climate-related transition and physical risks and opportunities in line with the TCFD recommendations. The Task Force on Climate-related Financial Disclosures (TCFD) develops voluntary, consistent climate-related financial risk disclosures for companies to provide information to stakeholders. General Mills supports this initiative and is committed to providing our stakeholders with relevant information on climate-related issues. A summary of our approach to each of the key pillars can be found below. Additional details on how we address the recommendations can be found in the TCFD index on our website and in our CDP Climate disclosure . Task Force on Climate-related Financial Disclosures Governance Strategy Risk management Metrics and targets Governance The Board’s Public Responsibility Committee provides oversight of the company’s sustainability work — including our climate program. In addition, our Chairman and CEO convenes the Global Impact Governance Committee at least three times each year to review and approve climate-related strategies, programs and key investments. Strategy As more than 85% of our overall greenhouse gas (GHG) emissions occur outside of General Mills operations, our climate strategy focuses on driving transformation and reducing emissions across our entire value chain. Our General Mills Policy on Climate outlines our approach to mitigation, adaptation, disclosure and advocacy. Metrics and targets In alignment with the new SBTi 1.5°C guidance, General Mills will reduce absolute GHG emissions across our full value chain (Scopes 1, 2 and 3) by 30% by 2030 (compared to 2020). By 2050, we will achieve net zero GHG emissions across our full value chain. We report on our metrics and targets annually in our CDP Climate disclosure . In 2021, General Mills took a leadership position by aligning a portion of our company’s financing with our commitment to combat climate change. In April 2021, we announced the renewal of a five-year $2.7 billion revolving credit facility, which includes a pricing structure tied to environmental impact metrics. General Mills was the first U.S. consumer packaged goods company to put in place a sustainability-linked revolving credit facility. By entering into this agreement, General Mills receives a pricing adjustment based on progress in two key areas: reducing greenhouse gas emissions in owned operations and using renewable electricity for global operations. In addition, in October 2021 General Mills announced its inaugural sustainability-linked bond aligned to climate change, making us the first U.S. investment grade CPG company to execute this type of bond. The 10-year, $500 million sustainability-linked bond is tied to measurable improvements on our journey to reduce our Scope 1 and 2 greenhouse gas emissions. Both of these innovative financing structures demonstrate our commitment to combating climate change and illustrate how we continue to embed sustainability into the fabric of how we operate. “Climate change and its effects are having an impact on our planet, people’s lives and on General Mills’ ability to live out our purpose of making food the world loves. General Mills is focused on reducing emissions across our value chain, and we are making strategic financial investments connected to our sustainability goals to further advance and support this important work.” — Kofi Bruce, Chief Financial Officer General Mills links financing with climate change commitments Being a force for good plays an important role in driving long-term shareholder value. We are integrating our force for good commitments across the enterprise, from brand strategy development to long range financial planning and capital management. For this reason, I serve on our Global Impact Governance Committee and am actively working to integrate ESG issues across our strategic planning and global finance functions. In May 2021, General Mills was the first U.S. consumer packaged goods company to enter into a sustainability- linked revolving credit facility, and in October we announced our inaugural sustainability-linked bond aligned to our climate change targets (learn more below). We also hosted our first-ever ESG investor event in May, highlighting how our work in this space is a key component of the company’s Accelerate strategy. Pragmatic long-range planning also requires an understanding of the risks that climate change presents to our future business results. To that end General Mills signed on as a supporter of the Task Force for Climate-Related Financial Disclosure (TCFD) in 2019. And in 2020, we commissioned Trucost/S&P Global to assess our risks related to climate change, including physical risks as well as risks associated with the transition to a low carbon economy, using a robust data- driven approach. You can find more information about our approach below. We believe that being a force for good and integrating our ESG efforts across the enterprise is not only an imperative for the planet, but can also drive value for all our stakeholders. Kofi Bruce Chief Financial Officer General Mills Thoughts from our Chief Financial Officer GENERAL MILLS GLOBAL RESPONSIBILITY 24 Food Planet People Community
In 2013, General Mills launched a goal to sustainably source 10 priority ingredients by 2020. Last year we achieved this goal, but our work continues to ensure access to high- quality ingredients as well as to manage the social, economic and environmental impacts of our ingredients. Through the results of our sustainable sourcing work, we learned that we need to take a holistic approach to regenerating ecosystems and advancing human rights in order to more fully actualize opportunities that catalyze change. This begins with understanding how systems — such as climate, agriculture, water, biodiversity, and farming communities — are all interconnected and how we as a company can positively impact each. Rooted in that knowledge, we have evolved from individual ingredient strategies to programs that help regenerate the planet while also creating positive outcomes for people. Below is how we have shifted our focus for the 10 sustainable sourcing priority ingredients. Please refer to the Regenerative agriculture , Eliminating deforestation , Water stewardship and Human rights sections for more detail on our strategies for these and other ingredients. Ingredient sourcing General Mills is collaborating with Musim Mas Group to invest in a smallholder palm farmer engagement program in Aceh Singkil, Sumatra, Indonesia, neighboring the Leuser ecosystem. We believe that investment and collaboration at origin, in partnership with key upstream suppliers, can support smallholder farmers in addressing environmental, social and economic challenges. Our partnership with Musim Mas is focused on improving the economic security of smallholder farmers and assisting them on their journey toward sustainable production, in collaboration with local government. Investment from General Mills is supporting the hiring of village extension officers (VEOs) who will provide good agricultural practice, financial literacy and no deforestation, no peat, no exploitation (NDPE) training and resources to smallholders. The program aims to train VEOS in order to ultimately provide support to over 1,000 smallholders in high-priority villages. As of October 2021, 75 VEOs have completed the training and Musim Mas has started engaging smallholders in three out of the six priority villages. Partnering to support sustainable production and smallholder farmers w Engaging smallholder farmers to improve sustainable farm management Ingredient sourcing to advance social and environmental ambitions Individual ingredient strategies Strategies that regenerate the planet and create positive outcomes for people Cocoa Corn Vanilla Dairy Oats Fiber packaging Wheat Sugarcane Sugar beets Palm oil Climate Regenerative agriculture Water stewardship Human rights FROM TO GENERAL MILLS GLOBAL RESPONSIBILITY 25 Food Planet People Community
Our approach While General Mills has minimal sourcing exposure to deforestation risks, we are committed to eliminating deforestation and the resulting impacts on biodiversity, endangered species, livelihoods and climate change. We regularly review our global sourcing footprint and focus on commodities at high risk of driving deforestation and where we can make a meaningful impact: cocoa, fiber packaging and palm oil. Within these categories, we employ a combination of approaches designed to help us achieve our sourcing goals and drive requirements to our upstream supply base. General Mills is a founding member of the Consumer Goods Forum Forest Positive Coalition of Action, formally launched in September 2020, which requires member companies to collaboratively work toward a forest positive future, and proactively work with suppliers to mainstream deforestation- free production across their business. Click here to view more on the Forest Positive Coalition of Action. Palm Oil: General Mills is a relatively small buyer of palm oil, using less than 0.5% of global palm oil supply in products like baking mixes, biscuits, and snack products. Despite the size of our purchase, we recognize that our purchasing practices toward deforestation-free palm oil can positively impact ecosystems as well as drive progress toward our science-based GHG emissions reduction to Scope 3. To help ensure our palm oil purchases do not contribute to deforestation of the world’s rainforests or negatively impact the communities and habitats that depend on them, we have sourced 100% of our palm oil as Roundtable on Sustainable Palm Oil certified sustainable since 2015. Our Statement on Palm Oil Sourcing lays out the principles we expect of direct suppliers, to ensure that they are in line with industry best practices, and contains information on our palm oil metrics, traceability and grievance process. Our approach, as well as the industry approach, to responsible palm oil is continually evolving and we are committed to working with our suppliers, peers, competitors and partners to support the development of a forest-positive, people-positive and climate-positive palm oil supply chain. General Mills is now more actively engaging its suppliers in direct review of their palm oil production and sourcing practices, moving to traceability to mill, and evolving where possible to plantation. We work closely with our suppliers and industry partners, like Proforest , to build sustainability performance and compliance with our policy commitments through active scorecarding, conversations and collaboration. As part of our effort to advance progress, General Mills has also joined the No-deforestation, No-peat and No- exploitation Implementation Reporting Framework (NDPE IRF) active working group — a reporting tool designed to help companies understand and track progress in delivering NDPE commitments, including deforestation- free supply chains. Click here to view our NDPE IRF profile, updated August 2021. Cocoa: More than 90% of our cocoa supply comes from West Africa, and 96% of our global supply comes from three key suppliers — Barry Callebaut, Cargill, and Olam. We work closely with NGO and supplier partners on the ground in Ghana and Côte d’Ivoire and invest to scale sustainable sourcing programs with a focus on strengthening smallholder farmer livelihoods, empowering women, and improving ingredient quality. In 2021, over 90% of our cocoa volumes were covered by these programs. In March 2017, we signed on to the World Cocoa Foundation’s Cocoa and Forests Initiative (CFI) to combat deforestation in key cocoa growing regions. Through this initiative we have worked closely with suppliers, stakeholders and Proforest to identify strategic actions to protect and restore forests, increase sustainable production, and promote social and community engagement. Additionally, we work with suppliers who plan to leverage full traceability to address deforestation risks within their supply chains. Our CFI action plans and progress to date for Ghana and Côte d’Ivoire can be viewed here . As we continue our work with CFI in our key cocoa sourcing regions in West Africa, we will leverage the knowledge we gain to inform approach and strategy to achieve deforestation-free cocoa for the rest of our sourcing origins. Eliminating deforestation GENERAL MILLS GLOBAL RESPONSIBILITY 26 Food Planet People Community
Fiber packaging: General Mills sources 100% of our fiber packaging from recycled material or from virgin wood fiber regions where there is demonstrably low risk of any deforestation. In 2021, 99% of our fiber packaging supply is considered at low risk of contributing to global deforestation because the packaging uses either recycled materials or virgin fiber that is sourced from regions where deforestation is not occurring. The remaining 1% is sourced from countries considered at high risk, particularly China. We’ve assessed suppliers in China to better understand certifications in use. Our fiber purchased from China is only sourced from suppliers that have Forest Stewardship Council (FSC) Mix certification or better, which will be maintained. Looking ahead: While we must focus on deforestation-free ingredient streams in the near term, this is nested in a larger strategy that works toward the acceleration of regenerative systems. Within tropical forests the regenerative approach brings focus to farmers, forests, and soil by looking at holistic systems to examine both planetary and community resilience within a particular landscape. This approach encourages mixed agroforestry, creating a polyculture and fostering biomimicry, leading to enhanced soil quality, better- managed water retention, and increased carbon sequestration within the forest. The regenerative approach also encourages capacity-building activities within local communities to focus on smallholder training on forest practices, economic resilience, and social inclusion training to regenerate livelihoods. Due to the challenges posed by key agricultural commodities such as palm oil and cocoa coupled with our scale and position in the supply chain, we recognize that moving to a regenerative approach is complex and will take time, as well as engagement with partners. Since 2019, General Mills has provided philanthropic support to PUR Projet to drive long-term forest protection and restoration by improving cocoa farmer livelihoods. Through work with smallholder farmers, PUR Projet has identified the urgent need to restore forest cover and strengthen economic resilience in key General Mills cocoa sourcing regions in West Africa, including Mont Peko buffer communities in Cote d’Ivoire and Kakum National Park in Ghana. With a goal of addressing deforestation in these regions, our PUR Projet partnership supports ecosystem restoration by engaging local communities through the introduction of diversified agroforestry and tree nurseries, while simultaneously launching complementary community-based activities that support the long-term success of tree planting initiatives, carbon sequestration, and ecosystem service-oriented activities through community empowerment and income diversification and generation. Combatting deforestation through farmer resilience r Farmer training on planting and maintenance in Ghana For more details on PUR Projet’s initiatives in cocoa, please find more information here . Community-run agroforestry and community- owned tree nurseries Income diversification through beekeeping and fish breeding Improved cooking stoves Environmental awareness and community resource management Impact studies on ecosystem services and farmer livelihoods GENERAL MILLS GLOBAL RESPONSIBILITY 27 Food Planet People Community
As a global food company, our business is rooted in agriculture. Over time, the quality and availability of the earth’s natural resources have declined, while the need to provide for a growing population has increased. Simply sustaining the current state of ecosystems and communities is not enough. We must instead invest in the potential of agriculture to ensure a thriving future for both people and planet. We are on a journey to make a meaningful difference through regenerative agriculture, which we define as a holistic, principles-based approach to farming and ranching that seeks to strengthen ecosystems and community resilience (see graphic below). Using our scale to maximize our impact, we are working with farmers to advance regenerative agriculture in key regions where we source our most greenhouse gas intensive ingredients, such as wheat, oats and dairy. Our goal: Advance regenerative agriculture on 1 million acres of farmland by 2030 (represents approximately 25-35% of our global sourcing footprint*). Progress: 115,000 acres enrolled in pilot programs advancing regenerative management Looking ahead: We’re energized by the level of farmer interest in our regenerative agriculture pilots and are building momentum as we learn from these early rollouts. We believe regenerative agriculture is the biggest lever in reducing our climate impact, so we are piloting a range of strategies for accelerating farmer adoption of regenerative agriculture in key sourcing regions. We are also investing to scale regenerative agriculture investments and measurement technologies as a leading climate lever. We’ve engaged SustainCERT to review our carbon insetting approach for agricultural GHG reductions and removals and have released a white paper on the results. Regenerative agriculture SOIL HEALTH: Soil is a complex ecosystem that forms the base of the food chain for humans and land animals. It plays an essential role in cleaning and storing water, supporting biodiversity and regulating the climate. WATER MANAGEMENT: Regenerative agriculture helps maximize water infiltration and use efficiency, and can reduce agriculture’s impact on water quality, helping to protect and restore clean water in nearby streams, rivers and lakes. BIODIVERSITY: Diversified cropping systems and integration of livestock support wildlife and beneficial organisms important to keeping pests in check and ensuring ecosystem resiliency to climate shocks. COW AND HERD WELL-BEING ( IN DAIRY OPERATIONS ): Rotational grazing and feeding cows a diverse mix of crops support cow health and increase resiliency across the whole dairy ecosystem. SIX CORE PRINCIPLES OF REGENERATIVE AGRICULTURE UNDERSTAND context of farm operation MINIMIZE disturbance MAXIMIZE diversity KEEP the soil covered MAINTAIN living roots year-round INTEGRATE livestock FARMER LIVELIHOODS AND COMMUNITY RESILIENCE: Regenerative agriculture systems repair and enhance ecosystem processes like nutrient cycling, water infiltration, and pest suppression, reducing the need for more expensive inputs and strengthening whole-farm profitability and resilience over time. Regenerative agriculture outcomes *Global sourcing footprint excludes acres associated with rotational crops; percentage may be updated in future reports due to changes in our business, improvements in data collection/accuracy or updates to calculation methodology. GENERAL MILLS GLOBAL RESPONSIBILITY 28 Food Planet People Community
Our actions We have multiple workstreams underway to accelerate the implementation of regenerative agriculture principles: Pilot programs: To advance adoption of regenerative agriculture, we have partnered with Soil Health Academy and Understanding Ag to activate pilots across three of our priority ingredient sourcing regions (see map). Each of these pilots provide farmers with practical tools to implement regenerative agriculture including one-on-one coaching and technical assistance for three years, customized plans for implementation in their operations, soil health testing, farmer networking communities, access to regenerative agriculture workshops, and biodiversity and economic assessments to demonstrate impact on outcomes over time. Learn more . We are also collaborating with leading conservation organizations within our key regions that — combined with the pilots — help to drive further progress in advancing regenerative agriculture systems. These include: n Soil health programs with the Wilkin County, Walsh County, and Kittson County Soil & Water Conservation Districts in the Northern Plains n Oklahoma Conservation Commission farmer-to-farmer mentorship program in the Southern Plains We are partnering with organic and conventional farmers, suppliers and trusted farm advisors in key growing regions to drive the adoption of regenerative farming principles. Starting with pilot programs in: Learnings from our pilot programs We’ve received positive feedback from both farmers and Understanding Ag (UA) consultants since launching our Southern Plains regenerative agriculture pilot in spring of 2020. This pilot, along with the Northern Plains pilot, are designed to study how effective deep soil health training, 1:1 technical assistance, and peer- to-peer learning are in advancing regenerative agricultural systems in the region. After two years of participation, Understanding Ag consultants surveyed farmers to understand how the program has aided them in their journey. The results to the right demonstrate the value of technical and social support programming in the understanding of soil health, implementation of techniques and related impacts, and the desire to continue advancing in the future. The feedback suggests our pilot investments have been effective in driving change and we’re now exploring how layering financial assistance mechanisms to further accelerate momentum. 2022 will be the final year for our Northern and Southern Plains pilots so we look forward to sharing additional insights and a broader suite of environmental and economic impacts in future reports. Survey Question Ye s No Do you feel you have a better understanding of soil health now compared to the start of the project? 20 1 Would you be using as much cover cropping on your farm if it were not for the support of your UA Consultant? 16 5 Would you be using as many diverse cover crop mixes if it wasn't for the advisement and support of your UA Consultant? 16 5 Do you feel that your soil health has advanced since the start of the project? 19 2 Have you experienced greater profits since the beginning of the project due to the advisement of your UA Consultant? 15 6 Do you intend to continue trying new things after the project is over to advance your soil health? 21 0 2021 Southern Plains Regenerative Agriculture Pilot Survey GENERAL MILLS GLOBAL RESPONSIBILITY 29 Food Planet People Community 70,000 ACRES OF ROW CROPS 40,000 ACRES OF ROW CROPS 5,000 ACRES OF DAIRY AND ROW CROPS SUPPORTED BY: SUPPORTED BY: SUPPORTED BY: NORTHERN PLAINS SOUTHERN PLAINS GREAT LAKES
Advancing measurement and technology: General Mills believes that measuring environmental and economic outcomes is critical to ensure that implementing regenerative agriculture leads to desirable outcomes. We are leading the industry in developing robust scientific methodologies to monitor and study the outcomes associated with regenerative agriculture in order to ensure credibility of our efforts. In partnership with numerous scientific organizations, we are conducting in-depth research on the impacts of regenerative management on soil health and carbon sequestration, water quality and conservation, insect and bird biodiversity, and farm economics. In addition to this farm-level research, we are implementing technologies that will allow us to quantify environmental impacts across entire regions where we source key ingredients. Using satellite imagery, we have begun to track changes in agriculture practices such as cover crops and no-till on the landscape over time and model the resulting impacts on metrics like greenhouse gas emissions. We are also developing more scalable approaches to monitoring biodiversity across farms, utilizing microphones for recording birds and light sensors to detect insects. Current Future Expensive, labor-intensive work to collect and analyze samples and farm data. Satellite imagery of agricultural practices Model environmental and economic outcomes High-tech sampling and monitoring for model validation + + + + In partnership with Furman University, we built a model simulating the effects of regenerative agriculture on bird populations and biodiversity. The model compared the current landscape to scenarios with 25%, 50% and 75% of cropland using regenerative agriculture practices in the Central Great Plains. Preliminary results suggest regenerative agriculture may play an important role in conserving many woodland and grassland species of birds on agricultural landscapes. Tracking regenerative agriculture outcomes on biodiversity r Our leadership in piloting groundbreaking technology is advancing the industry’s understanding and measurement of regenerative agriculture impacts. Riani (Ray) Lourens grew up on a farm in South Africa before relocating to a remote farming community in Saskatchewan, Canada. Her family’s operation is part of the General Mills Northern Plains Regenerative Agriculture Pilot program which kicked off in 2019. Ray has been working with Understanding Ag to implement regenerative management techniques on the majority of the farms’ managed acres, specifically incorporating livestock, nutrient cycling and reducing inputs. After the first year of participation, Ray’s expertise and leadership was recognized by Understanding Ag. As a result, she was invited to serve as a field consultant for Understanding Ag and work with other pilot farmers in addition to continuing as a pilot participant. Ray also helps with overall program administration and farm data collection to document the impact of regenerative management on ecosystem functions and farm/community resilience. Farmer spotlight “The best part about being in a project like this is the opportunity to meet other farmers who are like-minded and share thoughts and ideas. With our short growing season, we have unique challenges and have to find ways to incorporate the principles of soil health in context to our environment and individual operations.” — Ray Lourens GENERAL MILLS GLOBAL RESPONSIBILITY 30 Food Planet People Community
We believe one of the biggest barriers to widespread regenerative agriculture adoption is the shortage of experienced conservation professionals to help farmers implement regenerative agricultural systems. General Mills has partnered with the National Fish and Wildlife Foundation (NFWF) to help overcome this barrier by enabling greater local impact and providing more financial resources to farmers to reduce the economic risk of implementing new practices. The NFWF–General Mills partnership will support the hiring of field conservation professionals who will work directly with landowners to develop and implement planning and stewardship actions that generate economic benefits alongside positive environmental outcomes. Locally led programs will offer assistance that is adaptable to each producer’s unique goals, experience, risk tolerance, and other considerations on their path to a regenerative system. By focusing on the Great Lakes Basin and the Southern Great Plains, this effort prioritizes areas that are important for fish and wildlife, and advances regenerative agriculture principles in key ingredient sourcing regions for General Mills. General Mills’ investment with NFWF will be matched at a 2:1 ratio by the USDA National Resources Conservation Service (NRCS) and local conservation organizations. Scaling regional impact through partnership Research partnerships: Our regenerative agriculture commitment is the product of many long-term partnerships and investments. Just as we are working to help farmers implement regenerative principles, we are working with scientists to advance our understanding of complex farm ecosystems and the impacts of regenerative agriculture. Below are some of the partners we’ve worked with recently to study the soil health, biodiversity, climate, and economic impacts of regenerative systems. Brand activations: We know that our consumers care about where and how the ingredients in their food are grown. We work to advance regenerative agriculture by developing products with ingredients using regenerative principles. As we continue our journey to communicate and establish the importance of regenerative agriculture to consumers, on-pack messaging is a powerful way for us to introduce commitments, progress, and the farmers with whom we are partnering in this journey. Market opportunities: We work to increase market opportunities for farmers using regenerative management techniques. General Mills is a Founding Circle member of the Ecosystem Services Market Consortium (ESMC) and is working to advance market-based incentive mechanisms for farmers who reduce their environmental impacts. Soil health partnerships n University of Manitoba n Colorado State University n The Ecosystem Services Market Research Consortium n Soil Health Institute n Resource Environmental Solutions n The Ecdysis Foundation n University of Minnesota n Furman University r Some of General Mills products made with ingredients grown using regenerative principles General Mills, the Kansas Department of Health and Environment (KDHE) and the Ecosystem Services Market Consortium (ESMC) are partnering to pilot test ESMC’s program that rewards farmers for generating ecosystem services like greenhouse gas reduction and water quality improvement through regenerative agriculture. In the pilot, launched in 2020, General Mills and KDHE are testing ESMC’s protocols and processes to measure environmental impacts and pay farmers for soil carbon sequestration, reduced greenhouse gases, and improved water quality. The pilot is a leading example of public and private sectors coming together to quantify environmental improvements and compensate farmers for the environmental benefits they produce through regenerative agriculture. “Providing funds to farmers for their outcomes through an ecosystem payment is cutting edge and an important part in the future of agriculture. Instead of reacting to issues created by mainstream, traditional agriculture, this payment approach aims to eliminate them before they could even become a problem.” — Brandon Kaufman, Kansas farmer, co-founder of Sustain-A-Grain (growing Kernza) and partner in the ESMC program Piloting market opportunities with farmers GENERAL MILLS GLOBAL RESPONSIBILITY 31 Food Planet People Community
Water is essential for life — for drinking and sanitation, and to grow food, generate power, support commerce and nurture ecosystems. Ecosystems, including the farms that grow our ingredients, rely on a healthy global and local water cycle. So as a food company, General Mills too depends on water. On average, agriculture accounts for 70% of global freshwater withdrawals, and the food sector faces increasing risks related to water quality and availability. This underscores the leadership role General Mills and other food companies must take to address water stewardship issues. The General Mills Water Policy provides a framework for engaging with stakeholders and improving the health of watersheds that are critical to our business, and we are signatories to the United Nations CEO Water Mandate. We focus on water use from watershed to production, identify opportunities to increase efficiency, conservation, and regeneration (or recharge), and continually improve performance and enhance resiliency. Water stewardship As General Mills advances our work in regenerative agriculture, improved water efficiency and quality are some of the targeted outcomes. Regenerative agriculture can help to restore the water cycle on farms by enhancing water infiltration in soil and reducing water losses due to evaporation. This leads to more efficient use of water resources on farms and minimizes the runoff of soil, nutrients, and chemicals that can contaminate waterways — outcomes which we are monitoring as part of our regenerative agriculture commitment. We know that the holistic benefits of regenerative agriculture, including improved water outcomes, can benefit a wide variety of stakeholders. In 2020, General Mills commissioned Ecotone Analytics, in collaboration with the Cheney Lake Watershed, Kansas Department of Health and Environment, and No-till on the Plains, to conduct an Impact Analysis to estimate the social return on investment for regenerative agriculture in the Cheney Lake Watershed, where General Mills has a regenerative agriculture pilot. The study found that for every US$1 in costs to implement regenerative principles on-farm, there is approximately US$5 in social return on investment to farmers/landowners, taxpayers, local communities, municipal water plants and water users. Water and regenerative agriculture Farms that grow our ingredients depend on water As a food company, General Mills depends on water Livestock need clean water to drink and water to grow their feed Plants require adequate rainfall or irrigation from ground water or surface water to grow Pollinators, birds, and other local wildlife depend on access to water and healthy plants Water makes it possible for soil microbes to cycle nutrients and consume soil organic matter, key to healthy soil Farmers rely on water to run their businesses — and as living beings! Farm communities need water for drinking, sanitation, recreation, and more FOR INGREDIENTS — 85% n Growing ingredients from both crops and livestock n Ingredient transformation FOR PACKAGING — 14% n Growing (fiber) and extracting (metal, plastic) packaging feedstocks n Feedstock transformation n Packaging manufacture FOR MANUFACTURING — 1% n Plant sanitation n As an ingredient n Employee well-being Estimated return on investment per acre per year $189 Average additional cost per acre per year of regenerative agriculture practices $38 Average annual on-farm economic benefit over first 3-5 years of RA adoption Improved surface water quality and reduced eutrophication Reduced soil erosion from water Increased carbon sequestration Improved drinking water quality Reduced soil erosion from wind Increased farm resiliency Reduced irrigation needed *Estimation is a first approximation of value realized from RA practices. Additional benefits per acre will vary over time and by location within the watershed. Projected 400% social return on investment For every $1 contributed toward regenerative agriculture in the watershed, approximately $5 in additional social, environmental and economic value is generated in comparison to conventional practices.* GENERAL MILLS GLOBAL RESPONSIBILITY 32 Food Planet People Community
Our approach Water issues are local, so we take a risk-based approach to address risks in priority watersheds across our global supply chain. Through an updated and expanded water risk assessment conducted in 2019–2020, we assessed 20 key ingredients in 45 sourcing regions and 255 facilities (including 208 in our external supply chain), covering 60 major watershed basins and 221 minor watershed subbasins globally. This process included factors such as water quantity, water quality and reputation. We used the World Resources Institute (WRI) Aqueduct Water Risk Atlas and World Wildlife Fund (WWF) Water Risk Filter in this assessment. Based on this assessment, we identified 10 priority watersheds as the most material and at-risk (see map). Within these watersheds, we consider two types of risks: Acute risks are tied to specific locations, where we are focused on risk mitigation by supporting key NGO partners implementing watershed health strategies. Widespread/diffuse risks are broader in geographic scope and not easily traceable to specific organizations. To help address these, we pursue holistic approaches such as regenerative agriculture pilots. Water stress can manifest in different ways. For example, acute quantity risk could take the form of extreme droughts or flooding. Acute quality risk could be point-source pollution or widespread, such as agriculture runoff that leads to dead zones in bodies of water. The context around water stress in a given location helps determine the response needed. Goal: Our goal is to champion the activation of water stewardship plans for the company’s most material and at- risk watersheds in its global value chain by 2025. This is an ongoing process; as we continue to grow our company and identify new watersheds impacted by our business, this target may be extended to an evergreen commitment given the ongoing importance of water. Progress: Three of our 10 priority watersheds have active water stewardship plans in place. See map for details on how we’re advancing water stewardship in all of our priority watersheds. Our actions: n Fund and participate in local water stewardship activities and policy advocacy with NGO partners n Maximize water efficiency in owned plants in priority watersheds n Advance regenerative agriculture in California almonds, a priority watershed and high-risk ingredient, inspired by water impact in our Kansas regenerative agriculture wheat pilot Acute risks – Tier 1 Acute risks – Tier 2 Widespread/diffuse risks – Tier 3 Acute risks – Tier 1: Risk mitigation Acute risks – Tier 2: Observation n These high to extremely high watershed impact risks pose financial and brand risk due to geographically restricted commodity sourcing or plant impact n We implement local solutions to mitigate these risks, often focused on water use reduction and efficiency EXAMPLE AWS Certification in Albuquerque cereal/snacks plant n We monitor successful implementation of local solutions, with limited additional input needed from General Mills EXAMPLE Observing progress of Central Everglades Planning Project in a key sugarcane sourcing region n These geographically broad watershed risks cannot be pinpointed to water impacts at a specific location. As a result, brand risk is low to medium. n We pursue holistic approaches such as regenerative agriculture to address these issues EXAMPLE Our regenerative wheat pilot project in the Cheney Lake Watershed in Kansas. Tier 3: Positive impact potential GENERAL MILLS GLOBAL RESPONSIBILITY 33 Food Planet People Community
Yongding He HEBEI/S ANHE (BEIJING), CHINA Fa cility RISK LEVEL: EXTREMEL Y HIGH Status: Under evaluation Yangtz e ( Chang Jiang) SHANGHAI, CHINA Fa cilities RISK LEVEL: HIGH Status: Under evaluation Ganges MADHYA PRADESH, INDIA Gro wing region (wheat) RISK LEVEL: EXTREMEL Y HIGH Status: A ctiv e pr oject – Scienc e-Based Ta rget pilot San Joaquin CALIFORNIA, U .S. Gro wing region ( dairy , nuts, fruits and v egetables ), f acility RISK LEVEL: EXTREMEL Y HIGH Status: A ctiv e pr ojects – Gr oundw ater sustainability implementation and r egener ativ e almonds; Scienc e-Based Ta rget pilot Rio Gr ande/Rio Br avo NEW MEXIC O, U.S. Facility RISK LEVEL: EXTREMEL Y HIGH Status: A ctiv e pr oject – Regener ativ e fo restry Gro wing region (wheat, potatoes ) RISK LEVEL: EXTREMEL Y HIGH Status: Observ ation Risk le vels ar e based on a c ombination of the WRI Aq ueduct Wa ter Risk Atlas and the WWF Wa ter Risk Filt er, customiz ed to Gener al Mills. We refresh our wa ter risk assessment every thr ee y ears, and we complet ed that pr ocess in Fiscal 2021. Some of the priority wa tersheds not ed in this map ha ve changed. F or ex ample, recent structur al changes in our business led us to remo ve a previous priority wa tershed in China, and in North America we added priority wa tersheds in Arkansas and El Bajio . Rio Lerma Basin EL BAJÍ O, MEXIC O Gro wing region (strawberries ), f acility RISK LEVEL: HIGH Status: A ctiv e pr oject – Regener ativ e st rawberries Snak e IDAHO , U .S. South Florida Basins FL ORID A, U .S. Gro wing region ( sugarcane ) RISK LEVEL: HIGH Status: Observ ation Gro wing region ( dairy), f acility RISK LEVEL: HIGH Status: Under evaluation Escault/Parisian Basin ARRA S, FRANCE Gro wing region (ric e) RISK LEVEL: HIGH Status: A ctiv e pr oject – W etland conserv ation in ric elands Ba you Met o/Gulf Coas t EA ST ERN ARK ANS AS , U .S. General Mills priority watersheds Almonds — which are sourced largely from California — are a featured ingredient in many of General Mills’ products, such as cereal and granola bars. California is facing extreme water stress, which is leading to ground and surface water depletion as well as negative impacts to agricultural quality. And almonds, with their high water dependency, comprise the biggest water footprint of any California crop. Preliminary research suggests that almonds grown with regenerative agriculture principles result in powerful soil health and water benefits, including significantly higher water infiltration rates as well as potential reductions in irrigation needed. General Mills is taking a multipronged approach to advance understanding and adoption of regenerative agricultural practices for almonds: n Supporting sustainable water regulation implementation and agricultural water efficiency n Funding research focused on regenerative agriculture and water in California, with a specific focus on outcomes measurement and modeling for almonds grown using regenerative principles n Leading a working group with the California Water Action Collaborative to scope a regenerative agriculture pilot that aims to improve water resilience in the San Joaquin Valley Advancing regenerative agriculture in almonds w To advance regenerative agriculture in almonds, Lärabar is funding research with the Ecdysis Foundation to determine how on-farm practices are linked to regenerative outcomes. GENERAL MILLS GLOBAL RESPONSIBILITY 34 Food Planet People Community
Our approach Packaging plays a critical role in preserving the safety, nutrition and quality of the food we make. It presents challenges in terms of raw materials used in production as well as the waste generated when improper disposal occurs. Packaging is also the top sustainability issue with consumers. General Mills works to reduce the environmental impact of packaging by increasing use of recycled and recyclable materials, innovating to make our materials better, and leading through external collaboration. We are focused on protecting the attributes of the food while giving consumers a positive experience with our packaging, from shelf to bin. Given the many different types of packaging in our products, innovation in this space requires significant time, investment and collaboration. Ambition: Our packaging ambition is that all General Mills brands will design 100% of packaging to be recyclable or reusable by 2030. Progress: Through fiscal 2021, 89% of our packaging was recyclable (by weight). Our actions: n 100% of our fiber packaging is from sustainable sources, using either recycled materials or virgin wood fiber, avoiding deforestation. n We are innovating in plastic packaging, including bio-plastic film and recycled content in cereal box liners. n We are partnering with third-party suppliers of recyclable packaging to launch innovative solutions. (See the Nature Valley example below.) n We consistently seek opportunities to reduce or eliminate packaging materials, such as primary and secondary film, through lightweighting and removal. n We are supporting the development and use of recycling infrastructure by educating consumers; more than two-thirds of our products in the U.S. included How2Recycle labels, developed by the Sustainable Packaging Coalition. n We are leveraging external collaboration to drive industry- wide advancement in infrastructure, including with The Recycling Partnership and the Sustainable Packaging Coalition. Packaging In early 2021, General Mills launched the first store drop-off recyclable snack bar wrapper for our Nature Valley bars, coupled with a consumer education campaign on how to recycle them. Wrappers recycled through store drop-off programs are turned into new materials like composite lumber. To encourage adoption of this technology and accelerate the benefits of scale, General Mills has decided to not pursue a patent. We urge others in the industry to develop recyclable solutions, including polyethylene- based designs that can be certified for recycling within the store drop-off program. In 2019, Annie’s Homegrown and supply chain partners Charter NEX and Envision Plastics worked together to develop a new cereal liner that uses at least 35% postconsumer recycled (PCR) HDPE and is suitable for direct food contact. The Annie’s Friends cereal box includes special consumer- facing messaging around the use of recycled content. Launching food-grade PCR is revolutionary for the industry and took more than 20 years to develop from idea to on-pack. We have expanded the use of PCR film from one product to the full portfolio of Annie’s cereals and are now moving to include it in Cascadian Farms cereal as well. General Mills recognized for innovation by Sustainable Packaging Coalition Innovation in Recovery award winner Innovation in Responsible Sourcing winner 23% Plastic General Mills packaging materials * *F21 percentage of finished product packaging material by weight, including product and transportation packaging 57% 2% 1% 1% Fiber Composite cans Glass Aluminum 16% Steel GENERAL MILLS GLOBAL RESPONSIBILITY 35 Food Planet People Community
Our approach We work to drive sustainability across our global operations and continually reduce our environmental impact. Our main focus areas include GHG emissions, energy use, water withdrawal and waste reduction. Metrics reported in this section reflect data for General Mills’ wholly owned manufacturing facilities, unless otherwise specified. Greenhouse gas emissions: Greenhouse gas emissions from operations decreased by 30%* in 2021 compared to our 2020 baseline, primarily due to our ongoing progress in energy efficiency, consolidation of operations and application of renewable energy certificates (RECs) from our wind power agreement and purchases of Guarantees of Origins (GOs) in Europe (see details in the Appendix ). Energy use: During fiscal 2021, the energy usage rate at our production facilities decreased by 2% compared to the prior year, as efficiency improvements offset higher production of energy-intensive products. We identify and implement improvements through our Five-Step Energy Reduction Process (see graphic), by working with our manufacturing plants to establish energy programs, conduct energy analyses, develop and execute improvement plans, and validate results. This process historically focused on facilities with significant spending on energy. We have recently evolved it to include all General Mills manufacturing facilities, by focusing improvement efforts on common systems such as compressed air, lighting and steam/hot water. In fiscal 2021, we completed 35 energy efficiency and reduction projects across the company. In total, these projects saved 4.1 million kWh of electricity, 58 thousand MMBTU of natural gas, and avoided 370,594 metric tons CO₂e of GHG emissions. One example of these projects is a rooftop solar and battery system installed at our Sanhe, China, location, which is estimated to save 1.1 million kWh of electricity annually. Sustainable operations Five-Step Energy Reduction Process STEP 1 Establish energy program STEP 2 Conduct energy analysis STEP 3 Develop improvement plan STEP 4 Execute improvement plan STEP 5 Validate results During 2020, General Mills set a goal to source 100% renewable electricity for our global operations* by 2030. We achieved 63% of this target through fiscal 2021. We have implemented numerous renewable energy initiatives at facilities worldwide that meet financial guidelines and support our environmental objectives. Examples include anaerobic digestion (which captures and uses methane to generate electricity) and burning oat hulls and other biomass. During fiscal 2021, we generated and used 270,381 gigajoules (GJ) of renewable energy and applied renewable energy certificates (RECs) and Guarantees of Origins (GOs) that equaled 3,042,771 GJ of electricity. These RECs and GOs decreased our GHG emissions footprint by 385,346 metric tons CO₂e, contributing approximately 10% of reduction toward our 2030 full value chain goal. See additional details in the renewable electricity table in the Appendix. In June 2017, General Mills signed a 15-year virtual power purchase agreement with Renewable Energy Systems (RES) for 100 megawatts of the Cactus Flats wind project in Concho County, Texas. In fiscal 2021, this project generated RECs equivalent to approximately 1,205,596 GJ of electricity for General Mills, about 33% of electricity usage at our owned manufacturing locations in the U.S. In April 2019, we announced a 15-year virtual power purchase agreement with Roaring Fork Wind, LLC, a joint venture partnership between RES and Steelhead Americas, for 200 megawatts of its Maverick Creek wind project. Located in central Texas, the project will produce RECs for General Mills that, together with the Cactus Flats wind power agreement, are calculated to equal 100% of the electricity used annually at the company’s owned U.S. facilities. The Maverick Creek wind project began commercial generation in November 2020. Renewable electricity r Cactus Flats in Concho County, Texas. In fiscal 2021, General Mills rose to No. 22 on the Top 100 list of the EPA Green Power Partnership. *Scope includes all globally owned General Mills facilities (Manufacturing, R&D, Offices, Warehouses, HD Shops, and Cake Kitchens) *Emissions calculated using the market-based method, which considers any contractual instruments that may be used in competitive energy markets, such as green tariffs, renewable certificates, or PPAs. GENERAL MILLS GLOBAL RESPONSIBILITY 36 Food Planet People Community
*Disposal includes landfill and incineration without energy recovery. **These facilities sent no waste to landfill or incineration without energy recovery. ***Compared to 2020. ****General Mills follows the Food Loss & Waste Protocol Standard when defining “food waste.” Numbers do not include waste generated from Pet plants, waste going to animal feed or inedible byproducts. *https://refed.org/food-waste/the-challenge/#overview Water consumption: In fiscal 2021, the water usage rate at our production facilities decreased by 7%. Absolute water withdrawal related to our manufacturing processes equaled 13.6 million cubic meters, 4% less than in fiscal 2021. Waste reduction: We also work to decrease waste, which saves money and materials and decreases our overall GHG emissions. In fiscal 2021, the solid waste generation rate at our owned production facilities decreased by 1%. During the year, 62% of our total production solid waste globally was recycled, 26% was processed for energy recovery and 12% was disposed.* Worldwide, at the end of fiscal 2021, 11 General Mills production facilities (28% of the global total) met our zero waste-to-landfill criteria.** This changed from the previous year due to plant closures. We continue working to reach our target of 100% by 2025. To view additional data about GHG emissions, energy usage in our directly controlled operations, and water and solid waste, see the Environmental data summary . Food waste: In 2020, we announced a goal to reduce food waste in our operations by 50% by 2030.*** In 2021 we had reduced our food waste volume by 24% compared to 2020. In fiscal 2021, 0.5% of our total production volume was food waste.**** We participate in numerous initiatives to decrease food waste in operations and beyond, such as the U.S. Food Loss and Waste 2030 Champions, Friends of Champions 12.3 and Consumer Goods Forum Food Waste Coalition of Action. Learn more in the summary below. A multifaceted approach to rescue food We closely monitor and manage our production processes to keep surplus food out of the waste stream. Surplus food from our operations is first offered to food bank partners to feed hungry people; the remainder is repurposed for animal feed or anaerobic digestion. In fiscal 2021, 0.5% of our total production volume was food waste. In addition, 11 facilities (28% of the global total) met our zero- waste-to-landfill criteria in fiscal 2021. We also work to reduce food waste in our office buildings. At our headquarters, 89% of total waste was recycled and 0.58% went to landfill. We actively participate in industry, nonprofit and government groups focused on food loss and waste reduction as well as surplus food recovery, including AMERIPEN, the Food Waste Reduction Alliance, the Consumer Brands Association, ReFED, Consumer Goods Forum Food Waste Coalition of Action, MBOLD, and the U.S. Food Waste and Loss 2030 Champions. We are part of an industry effort to standardize food date labels to improve clarity about food quality and safety and reduce the amount of good food that’s thrown away. As of June 2021, we have updated 100% of our U.S. packages. General Mills is committed to increasing surplus food recovery, especially among consumer-facing food businesses — grocery stores, restaurants and other food outlets. These organizations collectively account for 28% of all food waste, roughly 50 billion pounds (more than 20 million metric tons) per year in the U.S. alone.* During the past four years, our global investments in food recovery technology have empowered more than 43,000 retail and foodservice locations to participate in systematic food rescue. General Mills provides philanthropic support to leading nonprofits that makes it possible for food manufacturers, grocers, restaurants, distributors, trucking companies and other organizations to donate surplus food so it can be distributed to people in need. n Our product donations to food banks enabled 41 million meals to nourish people globally in 2021. n Our investments in Feeding America’s MealConnect food recovery platform have helped recover and charitably redistribute more than 3.1 billion pounds of good surplus food. Communities Food retailers Operations As a global food company, General Mills believes that food loss and waste are major environmental and economic challenges that undermine food security, contribute to climate change, unnecessarily consume natural resources, like water, and add more costs to families, communities and businesses alike. Production waste *Disposal includes landfill and incineration without energy recovery. 2019 2020 2021 Disposal* Energy recovery Recycling Metric tons 50,000 150,000 300,000 100,000 250,000 200,000 350,000 9% 12% 8% 26% 26% 28% 65% 62% 64% Industry GENERAL MILLS GLOBAL RESPONSIBILITY 37 Food Planet People Community
Our approach At General Mills, we are responsible for maintaining high standards not only in our own operations, but also across our value chain. Our supplier base is large, complex and global, with thousands of suppliers in more than 25 countries. Through our Global Responsible Sourcing program, we uphold our Supplier Code of Conduct and drive ongoing supplier progress in the areas of health and safety, human rights, business integrity and the environment. This increases our influence to protect and respect the people who supply, transform and manufacture the goods and services we use to make our products. Audits: We expect all suppliers to uphold our Supplier Code of Conduct, and we use responsible sourcing audits to assess and understand suppliers’ business practices. These audits, which follow the Sedex Members Ethical Trade Audit (SMETA) protocol, are distinct from food safety audits. The SMETA framework is widely recognized by companies across many sectors, which enables suppliers to share audit results with multiple customers to improve efficiency and reduce audit burden. Accredited third-party auditors perform these audits and ensure timely creation of corrective action plans and closure of noncompliances identified within a specified time frame. Due to the challenges of COVID-19, General Mills is accepting virtual SMETA audits in regions where physical audits are not permitted. Owned locations and co-packers: All of our owned manufacturing locations and co-packers are required to conduct a physical audit every three years at a minimum and develop and confirm implementation of a corrective action plan for all noncompliances. During fiscal 2021, 45 of our owned locations and co-packers were audited, representing about 21% of the total. When issues arise in audits or through media alerts, the responsible sourcing team elevates them for visibility and provides regional sourcing leadership with recommendations to close the finding. If needed, visibility is brought to the regional supply chain leader for resolution. Regular progress review is conducted until the issue is resolved. Tier 1 suppliers: Tier 1 direct suppliers (suppliers that provide ingredients used in our food products or packaging) are rated by inherent country and goods risk using external data sources and are segmented into different risk levels. (See box for details.) From fiscal 2018 to fiscal 2020, inherently high-risk Tier 1 direct suppliers were asked to complete a self-assessment questionnaire followed by an audit for the subset of those suppliers identified as highest risk. In fiscal 2021, we shifted management of our audit program to in-house and expanded the scope to additional geographies and business segments. We also simplified our program by eliminating the self-assessment questionnaire and only requiring a SMETA compliant audit to decrease supplier time and resource requirements and improve the effectiveness of the program. All suppliers are expected to comply and participate in the program by submitting a SMETA- compliant audit when requested. Governance and integration: The Chief Procurement Officer leads Global Sourcing with accountability to our Chief Supply Chain Officer who reports to our Responsible sourcing 1990s 2008 2014 2021 General Mills was an early adopter of responsible sourcing and developed a program for manufacturing facilities producing premiums (such as toys included in or on pack) and supplier facilities that license our brands Launched program in our owned locations and co-packer facilities Added more Tier 1 direct materials suppliers in North America and expanded to locations in Asia, Latin America, Europe, and Australia, as well as Blue Buffalo locations in our Pet segment Expanded program to include locations of inherently high-risk Tier 1 direct materials suppliers in North America (suppliers that provide ingredients used in our food products or packaging) Global Responsible Sourcing timeline To segment our Tier 1 suppliers into different risk levels, we consider factors including geography, ingredient category, and the results of prior responsible sourcing audits from around the world, covering health and safety, human rights, business integrity and the environment. The audit-related data sources used include 3,655 SMETA supplier audits, 12,763 ISO 14001 supplier audits and 1,324 SA8000 supplier audits. These 17,742 supplier audits were concentrated in countries with known environmental, social and governance risks, based on public sources including the Yale Performance Index, the Social Progress Global Index, the Worldwide Governance Index and the Corruption Perception Index. Our segmentation, completed in January 2019, was determined based on an aggregation of this data. We selected these data sources to uncover risks as outlined in our Supplier Code of Conduct, focused heavily on human rights and health and safety. Risk-based segmentation GENERAL MILLS GLOBAL RESPONSIBILITY 38 Food Planet People Community
CEO. The Global Responsible Sourcing program has a dedicated team and is part of our Global Sourcing Operations and Capabilities (GSOC) group. GSOC reports to the Chief Procurement Officer and is focused on integrating key capabilities into Sourcing processes for General Mills globally. Responsible sourcing is integrated into our Source to Pay process, the workflow utilized by the Global Sourcing organization. In fiscal 2021, we further advanced our program in the following ways: n Shifted management of our Global Responsible Sourcing program from a third party to in-house n During the bidding process, began requiring all suppliers to upload a responsible sourcing audit and corrective action plan if one has been conducted in the last three years n Piloted addition of responsible sourcing metrics to co-packer scorecards, along - side commercial metrics such as on- time delivery and price competitiveness n Expanded program to include Tier 1 supplier locations globally, including Blue Buffalo in our Pet segment, supported by internal data systems n Leveraged holistic risk elements (such as financial, ethics and compliance, human rights and cyber) through the Global Supply Risk Center of Excellence (COE) to provide a more complete picture of supplier business practices n Assisted in the launch of an internal dashboard that allows buyers to easily access internal risk scores of all General Mills suppliers n Launched the use of virtual audits as needed due to COVID-19 n Piloted a new Risk Escalation and Reso - lution process that incorporates Global Responsible Sourcing program critical findings and also investigates human rights concerns outside of audit data (learn more in our Human rights section) n Began requiring buyer risk resolution plans to be submitted and approved by the sourcing leadership team as part of the escalation process n Launched a root-cause-analysis process with our suppliers to provide more robust corrective action plans n Began incorporating media alerts into our risk identification process n Partnered with the sustainability team to pull environmental data from our audits to help measure progress against our sustainability goals At the start of the COVID-19 pandemic, General Mills wanted to ensure the health and safety of workers at all levels in our supply chain. We broadly shared a list of best practices and guidelines with our suppliers on how General Mills was approaching COVID-19 safety protocols in our own facilities. Our Sourcing and Quality teams came together to host a food safety webinar that was available to all external manufacturing sites and direct suppliers. The webinar was created to share human and food safety best practices in light of the changes that COVID-19 brought to our manufacturing operations. We began to work in new and different ways, such as allowing for virtual audits and product startups so we could continue working in a safe and productive environment. Finally, we implemented a supplier appreciation and recognition program to show our gratitude and support to our suppliers who were working through a situation that was changing day by day. Partnering with our suppliers to address COVID-19 *% of noncompliances resolved are reported based on the number of findings rather than the number of suppliers with findings **Of noncompliances identified for owned manufacturing locations in fiscal 2021, 30% related to human rights and 70% related to health, safety, and environment. ***Of noncompliances identified for co-packers in fiscal 2021, 28% related to human rights, 59% to health and safety, 7% to environment and 6% to business integrity. ****Increase due to higher compliance from moving audit program in-house and expanding scope to additional geographies and segments. *****Of noncompliances identified for Tier 1 direct suppliers in fiscal 2021, 30% related to human rights, 61% to health and safety, 6% to environment and 3% to business integrity. Fiscal 2018 Fiscal 2019 Fiscal 2020 Fiscal 2021 Owned manufacturing locations Number of sites audited 20 19 23 15 Locations with noncompliances** 12 9 16 7 % of noncompliances resolved (December 2020 F18-F20) 94% 89% 65% 35% Co-packers Number of sites audited 47 35 22 30 Locations with noncompliances*** 31 17 14 20 % of noncompliances resolved (December 2020 F18-F20) 68% 98% 53% 34% Tier 1 direct suppliers Number of sites audited 38 11 1 190**** Locations with noncompliances***** 24 6 1 120 % of noncompliances resolved (December 2020 F18-F20) 60% 55% 0% 49% Responsible Sourcing Audit Overview: Fiscal 2018 – Fiscal 2021 * GENERAL MILLS GLOBAL RESPONSIBILITY 39 Food Planet People Community
Although General Mills is primarily a plant-forward food company, with large businesses such as Cheerios and Nature Valley, we use some animal- derived products and have long worked to support the humane treatment of animals in agriculture. This helps to ensure a resilient supply chain and aligns with our ambition to be a force for good. At General Mills we do not raise or handle livestock, but we are committed to protecting animals and work closely with our suppliers to do so. We regularly engage with stakeholders focused on animal health and welfare and leverage industry initiatives that advance livestock production. Our Animal Welfare Policy outlines our approach throughout the global supply chain for our food products, including: Cows: General Mills encourages all suppliers in our dairy supply chain to support industry-wide efforts that promote the humane treatment of cattle. All of the fluid milk we source in the U.S. for Yoplait comes from co-ops whose member farms operate in accordance with the standards of the National Milk Producers Federation animal care program (Farmers Assuring Responsible Management). The program comprehensively addresses dairy cow care, including standards for proper pain relief and disbudding, and prohibits the routine use of tail docking. The FARM standards are revised on a three-year cycle starting with a review by a technical committee composed of veterinarians and animal care experts. Eggs: Eggs are an important ingredient in ice cream, baked goods and doughs, and we strive to ensure the hens laying them are treated humanely. Our commitment is to purchase 100% cage- free or free-range eggs for our operations globally by 2025. In calendar year 2021, we contracted 61% of global egg purchases to be cage-free or free-range. COVID-19 has impacted our business mix and indirectly our egg volumes. In spite of this and other headwinds including inflation and market fluctuations caused by the implementation of Proposition 12 in California, our commitment is unchanged, and we detail our expected glide path below. Our progress is dependent on our suppliers’ ability to source cage-free or free-range eggs; ongoing challenges in supply and availability could impact these numbers. Chickens: General Mills will work to transition 100% of the broiler chickens we buy in the U.S. to meet a higher standard of animal welfare by 2024. Also by that year, we will work to ensure broiler chickens are processed using multistep controlled atmosphere stunning. By 2026 we will only use breeds accepted by the Global Animal Partnership (G.A.P.) or the Royal Society for the Prevention of Cruelty to Animals. Suppliers will be asked to demonstrate compliance through certification or third-party auditing. As qualifying breeds have only recently been determined by G.A.P., we anticipate that supply will remain limited in the near future. As we monitor industry developments, our near-term efforts will focus on advancing enrichments within the supply chain for our limited chicken purchases. Pigs: General Mills supports the humane treatment of pigs in our supply chain. This includes the development and implementation of pregnant sow housing alternatives. We favor suppliers working to reduce use of gestation crates in their supply chain. Looking ahead: We see potential for regenerative agriculture to provide a paradigm shift in agriculture’s approach to farm animal well-being, from incremental improvement to an animal- and ecosystem-centered approach. We are only just beginning to explore the opportunities here, starting in dairy. We are excited for the journey and learning opportunities ahead. Animal welfare 2021 2022 2023 2024 2025 60–65% 75–80% 80–85% 85–90% 100% Regenerative agriculture and animal welfare 1.5K 5+ <100 In June 2020, General Mills launched a three-year pilot in Western Michigan to advance regenerative principles at dairies that produce fluid milk for our yogurt products, including Yoplait. The pilot provides dairy farmers education and coaching to implement regenerative principles such as growing and using diverse mixtures of crops for feed to support both soil and animal health. Working with the University of Wisconsin–Madison and Cornell University, we are collecting a comprehensive set of animal metrics with the goal of understanding cow health and welfare as an integral part of the dairy ecosystem. These dairies manage 14,000 acres of crop land to feed their cows. Our goal is to introduce regenerative principles on 1,500 acres. The pilot farms represent more than 5 generations of dairy farming. Regenerative agriculture works with a farm’s natural ecosystem to improve overall resiliency and support farmer profitability. The milk from these pilot farms travels less than 100 miles to fill your favorite cup of Yoplait. ACRES GENERATIONS MILES GENERAL MILLS GLOBAL RESPONSIBILITY 40 Food Planet People Community
*Global survey of salaried employees, March 2021. of professional positions and 33% of company officer positions are held by women globally. of our employees* say that General Mills is a great place to work, up 4% from 2020. reduction in serious injuries at our production facilities and Innovation, Technology and Quality centers in fiscal 2021 compared to fiscal 2020. 50 % 51 % 90 % We create a seat at the table for all our employees by fostering a safe, inclusive and rewarding workplace. Human rights n Workplace safety n Global inclusion Employee well-being and development IN THIS SECTION People GENERAL MILLS GLOBAL RESPONSIBILITY 41
General Mills received numerous awards in 2021.* Listed below are a few of these recognitions, illustrating our commitment to being an employer of choice for all employees. *Recognition as of December 2021. 100 Most Just Companies, Forbes 100 Best Companies, Seramount Best Places to Work for LGBTQ Equality, Human Rights Campaign Best Companies for Multicultural Women, Seramount Military Friendly Employer (Bronze), VIQTORY World’s Most Admired Companies, Fortune America’s Most Responsible Companies, Newsweek 100 Best Corporate Citizens, 3BL Best Companies for Dads, Seramount Global 2000 List of World’s Best Employers, Forbes Best Employer for Diversity, Forbes America’s Best Employers for Women, Forbes Diversity Best Practices Leading Inclusion Index, Seramount American’s Best Employers for Veterans, Forbes At General Mills, it’s all about our people. The passion, conviction, commitment, care and resilience that our people bring to everything we do at General Mills are what make the difference. We’re proud of our efforts to create a safe, inclusive and rewarding workplace. We invest in our people because their bold thoughts and big hearts allow us to grow together. Our focus on people — including human rights and racial equity — extends across our value chain. 2021 was another year of change, with COVID-19, continued social inequalities, and our organization’s restructuring to prioritize growth-facing areas critical to the company’s success. These changes both reinforced and strengthened our resolve to put people first and make a positive impact in all our communities around the world. Supporting employees: We know that becoming the undisputed leader in food means continuously reshaping, reimagining and rebuilding. The pandemic reinforced that how we work and why we work matter more than where we work, so in July 2021, we introduced “Work with Heart” to guide managers, teams and individual employees in embracing new ways of working. In addition to providing greater flexibility, we also introduced new programs to support the mental and physical well-being of our employees and their families. Learn more . Governance: Responsibility for our labor practices lies primarily within our Human Resources, Law and Supply Chain organizations. Our Chief Human Resources Officer oversees employee programs, policies and practices, and reports directly to the Chairman and Chief Executive Officer. Reflecting the importance of people to our business, General Mills employs a Director of Diversity and Inclusion, a Vice President of Talent and Organization Capabilities, and a Director of Health, Safety and Environment. At the board level, the Public Responsibility Committee maintains responsibility for issues related to labor practices. Ethics and compliance: General Mills is committed to conducting business in an ethical manner that upholds best practices, protects human rights, complies with regulations, demonstrates integrity, provides equal opportunity and supports fair labor practices. Our comprehensive Code of Conduct and Ethics & Compliance program promote ethical behavior in all aspects of our employees’ work. In support of our Code of Conduct, the company has 24 corporate-level policies that outline more detailed compliance expectations. They cover topics such as food safety, workplace safety, appropriate advertising, business conduct standards, anti-corruption and ethical sourcing. Annually, more than 10,000 company leaders — from managers upward — must attest to compliance with our Code of Conduct and business conduct policies. Employees receive additional training on these policies, and our Ethics Line — which is easily accessible on our intranet and external website — allows employees worldwide to ask questions or raise concerns confidentially and anonymously. Our anti-corruption program includes employee training and assesses corruption risks with our third-party suppliers. All allegations of third-party corruption or employee misconduct are promptly and thoroughly investigated and shared in regular updates with the Audit Committee of the Board of Directors. Our Supplier Code of Conduct outlines our ethical expectations and is included in our contracts with business partners. Our approach Awards and recognition GENERAL MILLS GLOBAL RESPONSIBILITY 42 Food Planet People Community
We believe that societies, economies and businesses thrive when human rights are protected and respected and that human rights abuses of any kind are unacceptable. As one of the world’s leading food companies, we have the responsibility to respect human rights throughout our business and value chain. Respect for human rights is fundamental to our purpose of making food the world loves, our commitment to ethical business conduct and our corporate value of putting people first. As a force for good, General Mills is accelerating action to respect human rights and positively impact all the people we depend upon — and who depend upon us. As a global food company rooted in agriculture, we recognize that we have an impact on human rights beyond just our four walls. While philanthropic programs can play a necessary role in mitigating human rights risks, those programs alone do not offset the potential impact within our value chain. Our goal: General Mills is committed to respecting the rights of all workers and communities across our value chain. Our goal is to assess and address our human rights impacts in alignment with the United Nations Guiding Principles on Business and Human Rights (UNGPs) . Our approach: To better understand our human rights risks and guide our work, we are following a strategic framework (see below) — which directly aligns with the UNGPs — to strengthen our ability to assess, address and prevent potential imp acts across our value chain; and we are taking a thoughtful approach in each step of our journey. Protection of human rights is embedded as a prior ity within our Global Responsible Sourcing program. Learn more . O ur policies and c om mitments: Our Human Rights Policy , Workplace Standards and Ethical Sourcing Policy, E mployee Code of Conduct , Supplier Code of Conduct and Slavery and Human Trafficking Statement set standards fo r our company, suppliers and partners regarding the protection of human rights. We respect and acknowledge internationally recognized human rights princip les. We are working diligently to imp lement the United Nations Guiding Principles on Business and Human Rights (UNG Ps ) throughout our business. We have been a signatory to the United Nations Global Compact (UNGC) since 2008 and are guided by the UNGC’s 10 principles regarding human rights, labor, the environment and anti-corruption. We are also a signatory to the United Nations Women’s Empowerment Principles . Our Human Rights Policy states the standards for our company, suppliers, and partners regarding the protection of human rights. These standards are based in part on the International Labor Organization’s 1998 Declaration on Fundamental Principles and Rights at Work . Consistent with the principles outlined in our Employee Code of Conduct and Supplier Code of Conduct, we: n Prohibit forced labor, child labor and discrimination n Maintain safe and healthy working conditions n Value diversity and consider it core to our business strategy n Seek to compensate employees competitively and operate in compliance with applicable wage, work hours, overtime and benefits laws n Respect the principles of freedom of association and collective bargaining n Recognize the importance of land rights as well as the principle of free, prior, and informed consent (FPIC), as outlined in our palm oil statement , and support implementation of FPIC by national authorities. Governance and accountability: The Global Impact Governance Committee (GIGC) has ultimate accountability for the company’s global responsibility programs and performance. Our Chairman and CEO convenes the GIGC, which consists of officers of the company, quarterly to monitor and approve strategies, policies and key investments related to sustainability and social responsibility initiatives. The Board has made it a priority to ensure sustainability and global responsibility are taken seriously at all levels of the company. The Board’s Public Responsibility Committee provides oversight and receives regular updates from the operating teams. At General Mills, we have resources appoint ed to advance our human rights st rategy. The role of Director of Global Impact Operations Integration has acc ountability for advancing respect for human rights across our value chain Human rights strategic framework Identify greatest human rights risks across our value chain and prioritize known salient issues Integrate human rights expectations into policies and business practices Utilize the UNGP reporting framework to publicly disclose how we assess and address human rights impacts Effectively mitigate risks and remedy harm through stakeholder engagement, taking action and tracking progress ASSESS INTEGRATE ACT AND TRACK COMMUNICATE Human rights GENERAL MILLS GLOBAL RESPONSIBILITY 43 Food Planet People Community
and reports to the Chief Sustainability and Global Impact Officer. The Director of Global Impact Operations Integration also oversees the Human Rights Integration Team, a cross-functional team advancing General Mills’ work on human rights. The Global Responsible Sourcing program has a dedicated team and is part of our Global Sourcing Operations and Capabilities (GSOC) group. GSOC reports to the Chief Procurement Officer and is focused on integrating key capabilities into sourcing processes for General Mills globally. Risk assessment: Our approach to human rights is informed by an assessment conducted in 2020 by Shift , the leading center of expertise on the UNGPs, of practices across our business operations and supply chain according to the UNGPs in combination with our ongoing Global Responsible Sourcing risk assessments. We have defined our focus as the most salient issues in our value chain — those issues where our impact to people is greatest — by examining the relative severity and likelihood of each issue. Among our most salient human rights issues, we have identified forced labor and child labor in our agricultural supply chain as our highest priorities for action. While we seek to address all potential risks, this salient- issues lens informs our strategy. Due diligence: We have put in place a range of due diligence measures for our own operations and supply chains. These measures include audits conducted as part of our Global Responsible Sourcing program, which uses the four-pillar Sedex Members Ethical Trade Audit (SMETA) protocol or mutually recognized audits to assess our supply chain on social and environmental practices. We recognize our policies and programs may not prevent all adverse impacts in our value chain. Our aim is to provide effective responses where we find impacts directly linked to our business operations. We have in place a variety of mechanisms to allow employees, stakeholders and other potentially affected individuals to raise grievances, such as our Ethics Line . Learn more about our efforts in the responsible sourcing portion of the Planet section of this report. Some of the raw materials and ingredients General Mills sources for use in our products are recognized as posing a higher risk of negative human rights impact due to their growing regions and production methods. We are conscious of this impact — such as for cocoa, vanilla, palm oil, seafood and sugarcane. We engage with key Forced labor Salient issues Child labor Wages/ earnings and working hours Freedom of association and collective bargaining Land rights (Indigenous people) Types of actions n Provide assurance that our volumes were purchased responsibly and substantiate our sustainable sourcing claims n Leverage supplier programs for sustainable social and environmental outcomes n Demonstrate ingredient sustainability certifications n Engage with suppliers to verify our values are upheld in our supply chain n Expanded our Responsible Sourcing and Supply Chain Risk Center of Excellence n Updating our Supplier Code of Conduct n Conduct third-party upstream due diligence for high-risk commodities n Align and collaborate with other stakeholders in production landscapes for social and ecological impact n Provide origin-level investment through philanthropy n Collaborate across the sector to address systemic issues and support transformation n Participate in strategic industry coalitions INGREDIENTS What we buy DUE DILIGENCE How we buy LANDSCAPES The places we buy from SECTORS Issues across the sector Action within supply chains Action beyond supply chains Taking action to advance human rights and regenerative ecosystems * *Based on a framework developed by Proforest . GENERAL MILLS GLOBAL RESPONSIBILITY 44 Food Planet People Community
strategic partners to help us enable social and environmental progress in these value chains, such as our work with Conservation International in 2021 to review and strengthen our engagement in seafood supply chains, including risk assessment and mitigation strategies and identification of potential environmental and social impact opportunities. Similarly, our partners at Proforest conducted a human rights risk assessment related to our cocoa, sugarcane and palm oil supply chains in 2021 to enable us to proactively identify and respond to potential or emerging risk areas. As we learn from our partners, we will continue to strengthen our approach to address supply chain risks. Learn more about our efforts in the ingredient sourcing portion of the Planet section of this report. Looking ahead: Our journey to advance human rights is one of continuous improvement. As we grow and develop our program, we plan to expand our disclosures in line with the UNGP reporting framework. Our focus in the coming year includes: n Continue building due diligence capabilities to proactively identify risks where impacts to people are most severe across our value chain n Integrating human rights considerations into environmental strategies n Increasing employee awareness of our enhanced human rights strategy n Continue integrating expectations into standard business processes n Articulating human rights priorities and metrics for measuring impact for greater accountability Our approach: General Mills is committed to creating a culture that ensures zero harm to our employees and the environment. Working safely and in an environmentally conscious manner is not simply a matter of personal accountability or choice. As a corporation, we relentlessly seek to learn from our work and improve controls to prevent and mitigate significant safety and environmental events. Systems: We communicate safety information and measure progress with the following systems: n We use a single, standardized Environmental and Safety Management System (ESMS) at our supply chain locations and ensure uniform implementation of standards globally through functional auditing and a regional support structure. n Through our Global Safety Tracking and Environmental Management System (GSTEMS), we track safety data at all production facilities worldwide, document necessary actions to reduce future risks and communicate progress. Our progress: General Mills has a history of strong safety performance and culture. In fiscal 2021, we took bold steps forward by implementing new injury and illness reporting criteria and metrics to improve our safety culture and focus more intently on eliminating incidents and situations with the greatest potential to significantly harm our people. The decision to change our reporting criteria and metrics was informed by current best practices for preventing serious injuries and fatalities (SIF), including insights from The Campbell Institute Center of Environmental Health and Workplace safety DIVERSIFYING farmer incomes and improving livelihoods ADVANCING supply chain traceability and supplier engagement to advance social and environmental ambitions for palm oil IMPROVING smallholder livelihoods and reducing deforestation through origin-level investment in Indonesia with Musim Mas ACHIEVING Roundtable on Sustainable Palm Oil (RSPO) certification PROVIDING clean cookstoves to improve health IMPROVING agricultural productivity and ecological resilience ENGAGING with community members to mitigate and prevent child labor EMPOWERING women and communities through Village Savings and Loan Associations, women’s groups and community development committees Cocoa * Palm oil ** Making a positive impact on people’s lives Illustrated below are examples of human rights impacts across our cocoa and palm oil supply chains. *Impact achieved in Côte d’Ivoire and Ghana through: the Cocoa Sustainability Initiative (CSI) created by General Mills and CARE International ; partnership with PUR Projet ; support for Cocoa Horizons and Cocoa Promise supplier programs; action plans developed with Proforest ; and membership in the World Cocoa Foundation (WCF) . **Action through partnership with Proforest for supplier engagement, supply chain traceability, grievance management, sectoral collaboration via Consumer Goods Forum Forest Positive Coalition of Action; certification through purchasing RSPO Mass Balance palm and PalmTrace credits; and smallholder integration program at origin with Musim Mas Group. GENERAL MILLS GLOBAL RESPONSIBILITY 45 Food Planet People Community
Safety Excellence and guidance from ORCHSE , a division of the U.S. National Safety Council (General Mills is an ORCSHE member). The new safety metric criteria at General Mills are company- specific and based on the globally recognized principles of the ASTM E2920 international standard for recording occupational injuries and illnesses . Fiscal 2021 was a baseline year for our new safety metrics. Like fiscal 2020, we gathered safety data from 198 tracked locations, 56 of which are production facilities and Innovation, Technology and Quality centers. Those 56 locations were the focus of our safety improvement work. Safety highlights from those locations in fiscal 2021 include: n Zero General Mills and contractor fatalities globally n 50% reduction in serious injuries vs. fiscal 2020 n 14 locations operated with zero reportable injuries this fiscal year n A new baseline injury/illness rate of 2.14 was established Beginning in fiscal 2021, our company safety incident totals and injury/ illness rate looks different because it is based on a subset of the former data. We now calculate rate based on 1,000,000 hours worked as compared to 200,000 under U.S. Occupational Safety and Health Administration (OSHA) Total Injury Rate (TIR) criteria. We continued reinforcing our safety programs in fiscal 2021: n Standards – We published our first-ever standard focused specifically on SIF prevention. n Measurement – We leveraged our fiscal 2020 safety metrics change and improved our capability to identify and reduce SIF potential globally (we identified and took action to address over 1,100 potential SIF incidents in fiscal 2021). We also deployed new company environmental metrics and began data capture related to significant environmental incidents. n Mitigation – We recalibrated the safety and environmental aspects of our capital expenditure process to prioritize funding and improve controls related to our critical safety and environmental risks. n Learning and culture – We introduced additional global learning experiences focused on critical risk management and SIF prevention. We also began development of our next safety culture offering, Safety Leadership 2.0, which is based on current human and organizational performance principles. Leadership and responsibility: n Our Global Safety Governance Board, composed of regional operating vice presidents, oversees safety leadership, structure, processes and actions. n Senior-level responsibility for workplace safety lies with the Director of Global Safety and Environment, who reports to the Chief Supply Chain Officer. n Our Corporate Safety Council is led by our Chairman and Chief Executive Officer, who is responsible for General Mills policy and safety culture. The council, which includes key members of the company’s executive leadership team, reviews safety progress and key initiatives. The Council’s focus is on growing safety culture in both manufacturing and nonmanufacturing locations. n Workplace health and safety is the responsibility of line management and each individual employee. All employees are expected to work safely by following policies, procedures and training. Leaders are accountable for understanding and removing barriers to safe work that may be system related. New safety metrics enable focus on critical risks: PREVIOUS SAFETY METRICS Based on U.S. OSHA TIR* Reasons for the change: n Previous criteria and metrics were not aligned with our current incident prevention strategy. n Metrics were adding increased cost/risk and compromising our safety culture. n New metrics and data were required to evolve in safety. NEW SAFETY METRICS Based on ASTM E2920 principles Benefits: n More globally relevant and aligned with our strategy. n Regions continue to report injuries and illnesses per their local regulatory requirements. n Enables integration of other complementary safety metrics within General Mills to advance serious injury and fatality (SIF) prevention. * U.S. Occupational Safety and Health Administration (OSHA) Total Injury Rate (TIR) **Global incident data includes all General Mills owned/operated facilities, including Yoki and Yoplait International, Häagen- Dazs shops, Blue Buffalo and global offices. Injury/illness rate ** FY13 FY17 FY15 FY19 FY14 FY18 FY16 FY20 0.5 0.0 1.5 1.0 2.5 2.0 1.63 1.34 1.22 1.20 0.85 0.77 0.98 0.85 FY21 0.0 1.0 2.0 3.0 New safety metric based on ASTM E2920 international standard (2021 baseline year). Previous injury/illness rate results based on U.S. OSHA TIR* (# of injuries/illnesses x 200,000) ÷ (# of hours worked) (# of injuries/ illnesses x 1,000,000) ÷ (# of hours worked) 2.14 ** 2.14 GENERAL MILLS GLOBAL RESPONSIBILITY 46 Food Planet People Community
Our approach General Mills recognizes the imperative of using our scale to drive sustainable and meaningful change. We are dedicated to becoming a reflection of the world we seek, where equity and inclusion are a reality for us all. We know that meaningful change takes time — and it will take all of us to make progress at both the systemic and individual levels — and we are committed to continuing this critical journey with the strong belief that we can be a force for good. We continue to build on the positive actions we’ve taken for decades, and we recognize we still have a lot of work to do. We have committed to lead differently, vocally and tirelessly. The issues of social injustice are broad and complex, and we are focusing our efforts where our expertise can make the greatest impact: equitable food access, equity in education and equity in representation. Our goal is to foster a culture of inclusion and belonging that allows all our employees to thrive. Ensuring diversity of perspectives is core to our business strategy. We actively cultivate a culture that acknowledges, respects and values all dimensions of diversity — including gender, race, sexual orientation, ability, backgrounds and beliefs. We are committed to advancing racial equity within and outside our workplace. Our strategy: Using our global inclusion framework, we will advance engagement around the world, leveraging data to assess progress and hold ourselves accountable as we continue to foster a culture of inclusion and belonging at General Mills. Global inclusion Our commitment to racial equity Our role: We will direct our philanthropy to work locally and nationally in the U.S. with food banks and antihunger organizations to address food insecurity that disproportionately impacts communities of color. See our actions in the Community section of this report. Our role: Box Tops for Education TM will build on its legacy of giving nearly US$1 billion to schools, with a renewed focus on creating greater equity in education for kids of color in the U.S. so they can reach their full potential. Learn about our efforts to improve equity in education in the Community section of this report. Our role: We will address representation and access opportunities at General Mills in the U.S. by: n Doubling the representation of our Black managers* n Increasing our minority representation to 25%* n Doubling our spending with minority- owned suppliers** *See workforce diversity data on p. 51. **See supplier diversity data on p. 52 . EQUITABLE FOOD ACCESS EQUITY IN EDUCATION EQUITY IN REPRESENTATION General Mills global inclusion framework CULTURAL INCLUSION: Ensure an inclusive culture that encourages all employees around the world to share their unique perspectives and ideas in a safe and respectful environment WORKFORCE INCLUSION: Ensure we recruit, retain, develop and advance a workforce that reflects the diversity of the consumers we serve in our markets around the world at all levels of the organization CONSUMER INCLUSION: Ensure our brands and products consider the needs of an increasingly diverse consumer and customer base around the world while creating consumer messages that are respectful of that diversity SOCIETAL INCLUSION: Ensure our external impact is inclusive of diverse communities in our markets around the world through philanthropy, volunteerism and social good Societal inclusion Consumer inclusion Workforce inclusion Cultural inclusion GENERAL MILLS GLOBAL RESPONSIBILITY 47 Food Planet People Community
Governance and leadership: We believe leadership advocacy and support of our inclusion efforts are critical to creating the culture we strive to have. Each of our senior leaders is responsible for creating inclusion plans for their respective organizations and ensuring their talent pipelines reflect the diversity of our talent pool. Our Chief Executive Officer and Chief Human Resources Officer review inclusion progress throughout the year, including during our senior-level talent reviews. Our management team also supports our inclusion efforts as sponsors of our employee networks. Our progress In 2021, we continued to support key initiatives that help to develop and reinforce an inclusive culture at General Mills. In addition to these initiatives, our actions to advance equity in representation are highlighted on the next page. Allyship: More than 2,200 General Mills employees have committed to their allyship journey to authentically support individuals and communities who have been marginalized or overlooked. Courageous Conversations: Now in its fifth year, our Courageous Conversations initiative brings together employees to have candid discussions in a safe and supportive setting about important issues affecting our work and our lives. The conversations are designed to build empathy, productive discourse and employee engagement. Inclusion contacts: Our library of inclusion contacts now has more than 300 topics. Generally used at the beginning of a meeting, these contacts create space for team members to share experiences and perspectives, foster discussion and educate and inform teams about events, celebrations and holidays in order to build empathy and understanding. Employee networks: Our employee networks help build a culture of belonging by bringing together colleagues for community building, networking, professional development and community outreach. Our employee networks include: n Women’s Leadership Network (see related story on page 50) n Betty’s Family Network (LGBTQ+) n Asian Leader Network n Black Champions Network n The Familia Network n Veterans Network n Disability Network r Members of the Bettys’ Family Network led Pride celebrations at General Mills’ headquarters in 2021. Juneteenth Day of Action On June 18, 2021, General Mills hosted our first Juneteenth Courageous Day of Action. Employees at our headquarters packed more than 8,000 school supply kits for students. The event coincided with the first observance of Juneteenth as a U.S. federal holiday, commemorating the end of slavery. Learn more about this event and our efforts to advance equity in our communities in the Community section of this report. r CEO Jeff Harmening joined employees packing school supplies. r In August 2021 — one year after making public our commitment to racial equity — we came together virtually across the company for a Courageous Conversation to review our progress and challenge each other to do more. Watch this video to learn more about our progress. WATCH VIDEO r Members of The Familia Network partnered with our brand teams to provide food to participants during Fiesta Latina 2021, the annual Hispanic Heritage Month celebration organized by CLUES (Latino Communities United in Service) and co- sponsored by General Mills. GENERAL MILLS GLOBAL RESPONSIBILITY 48 Food Planet People Community
Our actions to advance equity in representation CEO Jeff Harmening on Representation Our journey 1953 Began support of the United Negro College Fund 1963 Began recruiting at Historically Black Colleges and Universities 1966 Hired first female officer 1972 Appointed first female board member 1973 Hired first minority officer 1975 Appointed first minority board member 1988 Named Reatha Clark King as President of the General Mills Foundation 1991 Hosted first annual Dr. Martin Luther King Jr. Holiday Breakfast 1992 Formalized supplier diversity efforts, including focus on minority-owned businesses 1994 Created the General Mills Office of Diversity 2013 Chosen for 10th consecutive year as one of the “Best Companies for Multicultural Women ” by Working Mother ; seven years later received its Hall of Fame Award 2016 Launched the Courageous Conversations , aimed at providing a safe and supportive place to have candid conversations about important social issues 2019 Launched an Allyship Program to take intentional action, like listening, learning and uplifting individuals and communities who have been marginalized or overlooked 2020 Publicly disclosed the company’s racial equity commitments “General Mills has been a leader in board and officer representation dating back to our first female board member in 1972. We know we live our purpose best when our workforce respresents the diversity of our consumers.” We’ve made our allyship resources publicly available at www.generalmills.com/allyship to help organizations create a culture of belonging for marginalized communities. Learn more about our actions to advance equitable food access and equity in education . Through our partnership with our corporate peers, local and state government, community leaders and others, we are taking bold and leading actions needed to combat racism and social inequality and ensure our community is a place where all can flourish. We are proud to be a founding member of the Minnesota Business Coalition for Racial Equity to create sustainable and meaningful change around racial and social justice for Black Minnesotans. Learn more in the Community section of this report. At General Mills, we have an ongoing commitment to diversity in leadership and talent acquisition. 17% 15% 6% of Officers at General Mills are Black compared to the U.S. average of 3.5%.* 23% are people of color of Senior Leadership Team members** are Black. 23% are people of color of members of the General Mills Board of Directors are Black. 33% are people of color *Source: Based on a study done by the Center For Talent Innovation in 2019 on Being Black in Corporate America. **Senior Leadership Team includes CEO’s direct reports. GENERAL MILLS GLOBAL RESPONSIBILITY 49 Food Planet People Community
General Mills is empowering women across our business. We promote women’s education, training and professional development within our businesses and supply chains. Our Women’s Leadership Network chapters around the world offer networking and development events in addition to mentoring circles. Our Women in Leadership organization advocates on behalf of women at all levels of the company to purposefully cultivate a pipeline of women leaders and a culture where women can thrive. We are committed to gender equality in the workplace, including pay equity. In partnership with external experts, we regularly conduct thorough pay equity reviews to ensure equitable pay outcomes for each job group. As a result of this work, we are assured that our pay systems and practices are generally fair and equitable among all employees (+/- 2% of 100%) without regard to gender, race or ethnicity. Across our supply chain, we work to help increase the economic resilience of women. Learn more about our partnerships to empower female farmers and entrepreneurs in the Community section of this report. Additionally, General Mills made a pledge seven years ago to advance the United Nations Women’s Empowerment Principles , part of the UN Global Compact, to help achieve greater equality for women in the workplace, marketplace and community. These principles are designed to promote gender equality and women’s empowerment. Women’s empowerment United Nations Women’s Empowerment Principles Establish high-level corporate leadership for gender equality Treat all women and men fairly at work — respect and support human rights and nondiscrimination Ensure the health, safety and well-being of all women and men workers Promote education, training and professional development for women Implement enterprise development, supply chain and marketing practices that empower women Promote equality through community initiatives and advocacy Measure and publicly report on progress to achieve gender equality 1 2 3 4 5 6 7 Promoting women leaders During the COVID-19 pandemic, the General Mills Women’s Leadership Network (WLN) focused on supporting its members in three key areas: care, flexibility and prioritization. As many women around the world were downshifting their work responsibilities — or exiting their jobs as part of the “great resignation” — the number of female leaders across General Mills increased.* One of those leaders is Natalia Faiden, director of food safety and quality for Meals and Baking Solutions in North America, who was promoted to this role in 2021. She previously led the WLN chapter in her native Argentina, now leads WLN’s Innovation, Technology and Quality (ITQ) functional network and served as a cochair for WLN’s International Women’s Day (IWD) event in 2021. The event was, for the first time, entirely virtual. “It was much more inclusive because everyone around the world could be present in the same way,” said Faiden. More than 3,000 people from 20 countries participated — twice as many as the previous year. “WLN has provided a safe space to find my voice and my purpose with opportunities for networking and mentoring by women leaders who inspire me. Now I am helping pave the way for others,” said Faiden. “During the pandemic, women have been disproportionately affected as they juggle duties in the workplace and at home, so WLN has put empathy front and center in our programming. We provided input on the need for flexibility and for policies that support employee well-being.” *Percentage of female managers globally increased from 49% in fiscal 2020 to 50% in fiscal 2021; female directors increased from 40% in fiscal 2020 to 43% in fiscal 2021. r Faiden shared her #ChooseToChallenge IWD pledge to help build a gender- equal world through a culture of belonging and inclusivity. #ChooseToChallenge I will help forge a gender equal world GENERAL MILLS GLOBAL RESPONSIBILITY 50 Food Planet People Community
General Mills workforce diversity *Represents U.S. data and includes salaried employees in fiscal 2021. Percentages may not total 100 due to rounding. White W Asian A Black or African American B Hispanic or Latino L Native Hawaiian or Pacific Islander NH Two or more races T Board of Directors Total salaried Officer W: 76% W: 67% W: 83% W: 83% W: 80% W: 81% A: 7% A: 9% A: 7% A: 7% A: 7% B: 4% B: 7% B: 17% B: 5% B: 3% B: 4% L: 6% L: 7% L: 17% L: 6% L: 5% L: 6% T: 1% NH: 1% NH: 1% NH: 0.4% T: 1% T: 2% T: 1% Director Manager Professional Racial/ethnic diversity * Gender diversity ** **Represents global data and includes salaried employees in fiscal 2021. Percentages may not total 100 due to rounding. Female Male 33% 67% Officer Female Male 51% 49% Professional Female Male 42% 58% Board of Directors Female Male 50% 50% Total salaried Female Male 43% 58% Director Female Male 50% 50% Manager Diversity and inclusion recognition n Best Employer for Diversity, Forbes n Diversity Best Practices Leading Inclusion Index, Seramount n Best Companies for Multicultural Women, Seramount n Best Places to Work for LGBTQ Equality, Human Rights Campaign n America’s Best Employers for Women, Forbes n American’s Best Employers for Veterans, Forbes n Military Friendly Employer (Bronze), VIQTORY GENERAL MILLS GLOBAL RESPONSIBILITY 51 Food Planet People Community
Supplier diversity Our approach: General Mills has been committed to establishing and growing relationships with certified diverse suppliers in the U.S. for more than 50 years, providing opportunity to underrepresented groups while fostering job creation and economic development.* By requiring businesses to be certified by our partner advocacy organizations, we stay true to our goal of providing diverse suppliers with greater access to our spending while bringing credibility through third-party authentication. These inclusion efforts also support General Mills by delivering innovation, agility, cost savings and market insights about our increasingly diverse consumers. Our Supplier Diversity Team, which is embedded in our Global Supply Chain organization, builds partnerships across the company to match diverse suppliers with business needs and opportunities. The team integrates supplier diversity into the standard sourcing process, trains all sourcing buyers and provides tools to advance the program. Sourcing category managers incorporate diversity into their strategic plans to drive progress and share results with sourcing leadership. Our approach in recent years has evolved by applying robust data, standard processes and business integration that mirrors our sourcing organization workflow. Our actions: We have expanded our supplier diversity program globally to include all of our sourcing regions in addition to North America.** In fiscal 2021, we successfully: n Compared internal and external data sources to continually locate and verify certified diverse suppliers n Executed a supplier scouting and vetting process to expand our potential partner base n Measured bid inclusion and win rate to highlight capable suppliers across multiple platforms n Moved the Tier 2 program from pilot to launch, expanding our expectations for inclusion to our supply base and increasing overall diverse spending by more than $55,000,000 n Launched a diverse certification sponsorship program to help small or startup businesses achieve diverse certification status with funding and consulting support from General Mills n Made a corporate commitment to double spending with minority-owned businesses and achieved this goal in fiscal 2021 by increasing spending with minority-owned businesses to more than $181 million*** Collaboration: We are active members in national and regional advocacy organizations, such as the National Minority Supplier Development Council (NMSDC), North Central Minority Supplier Development Council (NCMSDC), WEConnect International, Women’s Business Enterprise National Council (WBENC), Women’s Business Development Center (WBDC), and the National LGBT Chamber of Commerce (NGLCC). Through these organizations and other industry groups, we benchmark, share best practices and network with prospective diverse suppliers. *Diverse suppliers are defined as businesses 51% owned and operated by racial minorities, women, veterans, and disabled and LGBTQ+ individuals. **Our program expansion targets women-owned businesses globally, in addition to providing our full support to all recognized diversity groups in North America. ***Includes Tier 1 and Tier 2 suppliers. Minority-owned businesses $181.3 Women-owned businesses $122.9 Veteran-owned businesses $12.5 Disability-owned businesses** $0.09 LGBTQ+-owned businesses $0.07 Total $318.3 Total (% of total global supplier spending)*** 3.7% General Mills spending with diverse suppliers (fiscal 2021, US$ million)* *Represents spending in the U.S.; for suppliers certified in multiple categories of diversity, spending with those businesses is included under their primary diversity status. **Disability-Owned Business Enterprise (DOBE) certification — businesses owned and operated by people with disabilities. ***Diverse U.S. supplier spending as a percentage of total global supplier spending; includes Tier 1 and Tier 2 suppliers. Certification sponsorship program “Working with General Mills has had a greatly positive impact on our business. Because of our certification through WBENC, we’ve been able to secure retailers we wouldn’t have in the past. Our certification has led to a distribution partnership that has vastly broadened our potential retail footprint. We’re incredibly grateful to the General Mills team for their continued support.” — Claire Smith, Founder, Tenera Grains In 2021, we launched a supplier diversity certification sponsorship program to fund and support small diverse businesses in attaining their diverse certification. The first participant was Tenera Grains, maker of innovative Teffola granola made from the ancient grain teff. After achieving WBENC certification as a woman-owned business, Tenera Grains made it to the finals of the WBENC NextGen Pitch Competition. GENERAL MILLS GLOBAL RESPONSIBILITY 52 Food Planet People Community
Employee benefits and well-being Our approach: We provide our employees with a work environment that encourages innovation, productivity and flexibility — and that helps every employee bring their unique self to work every day. Our progress: Throughout 2021, we listened to our employees, then adapted and responded to help meet their evolving needs during this year of uncertainty, challenges and change. Employees told us that flexibility around when and how to return to the office was critical to their satisfaction and ability to do their best work. We introduced the “Work with Heart” program in July to provide flexibility, guidance and resources for new ways of working, including hybrid meetings and schedules. To continue supporting employees’ well-being, we introduced two new programs in January 2021: n Spring Health – A confidential resource that provides mental health support services to employees and their families, including dedicated support from a care navigator, personalized care plans, therapy, meditation exercises, coaching to manage stress, medication management, substance use support and other services to help navigate life’s challenges.* n Virgin Pulse – A behavior-change program that helps employees prioritize their well-being, including eating habits, sleep, physical activity, relationships and finances. The program makes it easy to track progress, connect, and compete with friends, family and coworkers to earn rewards.** Benefits: Employee benefits vary by location. For example, for nonunion employees in the U.S. we offer: n Overall – Comprehensive medical and dental benefits to employees and eligible dependents. Employees are automatically enrolled in company- paid benefits, including life insurance, business travel accident insurance and short- and long-term disability. n Financial planning – Retirement benefits, including a 401(k) savings program and financial coaching. n Time off – Vacation, holidays, flexible work arrangements and leave benefits for all life stages, including up to two weeks of paid caregiver leave per year and 12 to 20 weeks paid parental leave for new parents. Other perks: n Learning, developing and growing – Tools and resources to help employees expand and grow as professionals. See more details in the Development and training content. n Giving back to the community – Volunteer opportunities and donation match programs. Learn more in the Community section of this report. n Talent referral – Bonuses for referring top talent to join the General Mills team. Employee well-being and development *Spring Health is currently available to employees in the U.S. and Canada. **Virgin Pulse is currently available to nonunion U.S. employees and their eligible spouses/partners. Impact of mental health and well-being programs* Mental health: n 3 weeks faster: 1.2 days average wait time for therapy vs. 25-day national average n 22% average improvement in patient depression severity** n 14% average improvement in patient anxiety severity** n 50+ individuals received critical support for positive ideations/intent of suicide n >90% employee satisfaction with their providers and navigators Overall well-being: n 78% of participants increased or maintained healthy activity (average steps per day) n 80% of high-risk/obese participants and 78% of overweight participants have lost weight *Data based on the experiences of employees and family members in the U.S. and Canada who participated in Spring Health programs during the first six months after program launch (January to June 2021). **Those who are actively working their care plan are seeing measurable improvements in as little as one appointment. 2021 Progress n Focuses on results, not facetime n Tailored, because no two employees or teams are exactly alike n Provides flexibility for employees spending a mix of time working onsite and offsite, with variation from day to day or week to week based on what work needs to be done LEADER AND TEAM EFFECTIVENESS WORK PREFERENCES INCLUSION AND BELONGING WORK WITH GENERAL MILLS GLOBAL RESPONSIBILITY 53 Food Planet People Community
Employee engagement, development and training Our ability to make food the world loves is driven by our strategy of engaging people in a culture of learning, growing and belonging. Employee engagement Our approach: We know that engaged employees create value and drive business performance. We continually work to build a more agile, engaged organization by listening to employees, taking action and measuring progress. We survey employees annually to measure five drivers of employee engagement: proud of my company, inspired by my leaders, connected to my team, supported by my manager and energized by my work. In fiscal 2021, we continued to create more frequent opportunities for listening to our employees as we navigated remote work dynamics. *Global survey of salaried employees, March 2021. of our employees say that General Mills is a great place to work, up 4% from 2020.* of our employees say they are comfortable at work saying or doing what they think is best for General Mills, up 3% from 2020.* EMPLOYEE ENGAGEMENT 90 % 87 % 2021 Progress OVERALL: BY DRIVER: FY18 Overall Connected to my team Supported by my manager Energized by my work Proud of my company Inspired by my leaders Engagement trends: Another year of consecutive gains * v We saw continued employee engagement gains in all categories in fiscal 2021, continuing the upward trend since fiscal 2018. Annual global survey of salaried employees, March 2021. 75% 87% 80% 73% 69% 80% 89% 84% 78% 77% 70% 83% 90% 85% 81% 88% 87% 92% 85% 86% FY19 FY20 FY21 “I have been super proud to work at General Mills over the last year — especially during the pandemic. The challenging times have shown the true nature of the people and structure here. I appreciate the open communication and consideration for all factors of our health and well-being.” — General Mills employee GENERAL MILLS GLOBAL RESPONSIBILITY 54 Food Planet People Community
Development and training Our approach: Development of all employees is a core value at General Mills. A recent employee engagement survey revealed that 81% of employees feel they have the opportunity to grow and develop at General Mills.* Learning is a key ingredient of our approach, including formal and informal mentorship programs, employee network connections and a range of development opportunities at all stages of employees’ careers: n New employee orientation and a 12-week onboarding process n Hands-on experiences, including challenging work assignments and robust job rotations n Guidance from others, including feedback from managers, mentors and peers n Real-time learning resources for leaders and all employees n Structured learning — offered both in person and online — including onboarding for new employees, professional development for all and leadership development n Our performance management process, in which more than 19,300 employees globally participated in fiscal 2021 Our progress: In 2021, we launched a new performance management process and continued to accelerate our Engaging Leader initiative, which we introduced in 2017 to transform the way our leaders support employees and live our values to drive performance and engagement. In 2021, we advanced Engaging Leader programs to adapt to new ways of working and tailored training formats for manufacturing locations in order to address the different needs of each employee group. The key behaviors that are the focus of this training vary slightly between our manufacturing sites and nonmanufacturing locations. Manufacturing teams globally focused on: explicit strategic intent — so employees understand the “why” behind the work; knowing and appreciating each team member to help build a culture of belonging; and embracing a learning mindset to encourage team and personal growth. Engaging Leader Leader & employee development Diversity & inclusion Performance & recognition Well-being programs In 2021, we focused on these key Engaging Leader behaviors and actions globally in our nonmanufacturing locations: Generate ideas, broaden reach of input and gather differing points of view Adopt better ways of working that allow us to pivot quickly and seek and integrate external perspective Regularly give and request performance- based feedback and use individual development plans (IDPs) to track toward development goals ENGAGING LEADER BEHAVIORS Encourage productive discourse Foster agility Embrace a learning mindset ACTIONS Engaging people in a culture of learning, growing and belonging **Includes more than 20,400 salaried and wage employees annually. hours of training completed by our employees, equaling 14 average hours per employee.** 287,000+ DEVELOPMENT AND TRAINING 2021 Progress Engaging Leader Weekly Planner For Manufacturing Play to win Act boldly & move quickly Win as a team Grow & inspire Do the right thing all the time Explicit Strategic Intent • Share/understand inspiring Compelling Business Need (CBN) • Connect master plan, priorities & daily work to CBN • Share/know the “why” behind work • Use communication pyramid to engage all in pursuit of vision Know and Appreciate Each Player • Know each team member & what is important to them • Regularly spend time on the floor making purposeful connections • Recognize accomplishments & celebrate success • Do what you say you will do Embrace a Learning Mindset • Believe you and your team can learn & grow • Develop through Learn -Do- Teach • Ask for, appreciate, and act on feedback • Be open minded and willing to try new things • Acknowledge mistakes, learn and move forward F21 FOCUS AREAS r We used a variety of Engaging Leader materials, such as this poster, to build awareness of desired behaviors in our manufacturing locations. *Annual global survey of salaried employees, March 2021. GENERAL MILLS GLOBAL RESPONSIBILITY 55 Food Planet People Community
We gave US$98.3 million to charitable causes in fiscal 2021, including General Mills Foundation grants, corporate contributions and food product donations. Our product donations to food banks enabled 41 million meals around the world in fiscal 2021. Our strategic philanthropy and our community giving in General Mills hometown communities spanned six continents in fiscal 2021. $ 98 million 41 million 6 continents We are deeply committed to the communities where we live and operate and from which we source our ingredients. Our philanthropic partnerships and employee engagement aim to build strong, equitable and resilient communities. Alleviating hunger n Regenerating ecosystems Strengthening hometown communities IN THIS SECTION Community GENERAL MILLS GLOBAL RESPONSIBILITY 56
General Mills philanthropy ties closely to our company’s purpose, core business and food systems knowledge. We partner in innovative ways with nonprofits and other partners to grow our collective impact in targeted issue areas, while engaging employees through volunteerism. Leadership and governance: General Mills philanthropy and community engagement programs are led by the Chief Sustainability and Global Impact Officer with support from a team of experienced specialists who steward the company’s philanthropy. In addition, employee councils located across our key global operating communities — General Mills “hometowns” — help to inform our local grant-making by recommending nonprofits to be considered for grants. General Mills philanthropy is governed by the Global Impact Governance Committee , which includes the company’s Chairman and Chief Executive Officer and leaders from law, finance, R&D, supply chain, marketing, strategy and growth, communications and innovation functions. Global focus areas: Alleviating hunger – feeding those in need, promoting surplus food recovery and addressing racial disparities in food access. Regenerating ecosystems – empowering growers and regenerating ecosystems and natural resources. Strengthening hometown communities – making meaningful impact in the communities where our employees live and work. Targeted impact: To ensure General Mills philanthropy is well informed and effective, we use an outcomes-based approach to help strategically target and advance solutions in priority issue areas. Led by managers on our Global Impact Team and with input from other internal and external subject matter experts, we leverage the evidence base to develop logic models for each of our priority issue areas that clearly define: the end outcomes (social and environmental) we are targeting; the key activities and interventions that best support those outcomes; and the key measures we will use to assess our impact and progress along the way. Our approach General Mills fiscal 2021 giving to strengthen communities The amount we gave to charitable causes in fiscal 2021 $ 98 million Corporate contributions Food donations Foundation giving $ 15 million $ 58 million $ 25 million *Includes food donations, Box Tops for Education TM and other corporately funded cause marketing and charitable contributions, as well as giving from the General Mills Foundation. The total amount of all General Mills charitable giving from 2011 to 2021. * $ 1.4 billion r Our philanthropy work is strongly aligned with many of the United Nations’ Sustainable Development Goals (SDGs), including goals 2, 5, 6, 12, 13 and 15. Holistic approach to regenerating forest ecosystems General Mills’ philanthropic program in cocoa growing communities in West Africa aims to support long-term forest protection and restoration by improving overall farmer livelihoods. To ground our work in community needs and achieve longstanding impact, General Mills’ partner, PUR Projet, conducted two Farmer Livelihood Assessments during fiscal 2021 in Ghana and Côte d'Ivoire. This methodology provides a holistic vision of objectives, constraints and opportunities for the program’s participating farmers by embedding a systems approach in a series of interlocking activities. These assessments provided a clear framework for operating that is key to achieving success. Learn more in the Planet section of this report. GENERAL MILLS GLOBAL RESPONSIBILITY 57 Food Planet People Community
Our approach: Grounded in our belief that every individual, family and community should be food secure and free from hunger, we work to: n Ensure food access for all — Together with our nonprofit partners, we take aim at inequitable food access and hunger to ensure all members of the community have reliable access to a wide range of affordable foods. n Expand surplus food recovery and charitable redistribution of good food — We support food banks in more than 40 countries as well as other nonprofits focused on ensuring the world’s good food is used to nourish people and doesn't go to waste. n Support strategic public policy — We advocate for policies that support long-term solutions to alleviate hunger and reduce food waste. Learn more about our public policy engagement to ensure people have access to nutritious and sufficient food. Alleviating hunger Alleviate child hunger n Strengthen the reach and impact of school meal programs in our key global markets worldwide n Increase food access among lower income populations by promoting participation in national food and nutrition assistance programs among those who are eligible Address racial disparities in food insecurity Promote vibrant community food systems with equitable food access: n Partner with civil rights and anti-hunger organizations n Support culturally specific, locally driven solutions n Advocate for resources and policies to drive long-term systems-level solutions to end hunger Grow capacity for surplus food recovery n Donate General Mills surplus food n Support and strengthen food banks’ capacity to recover and equitably distribute food n Invest in innovative food recovery systems to make it easy for food makers, grocers, restaurants, distributors, schools and trucking companies to donate their surplus food n Support farm-level food rescue General Mills and our partners are improving equitable food access for people in need. Alleviating hunger globally Our actions: We work with partners around the world — including food banks, school breakfast club programs and other anti-hunger organizations — to expand food security and build long-term resilience for the future. We support community outreach programs that help families at risk of hunger enroll in food and nutrition assistance programs, such the U.S. Supplemental Nutrition Assistance Program (SNAP) (see how our employees supported this effort), and that strengthen the reach and impact of school meal programs to reduce childhood hunger globally. We know that households with children are more likely to be food insecure.* Because schools are powerful levers for increasing food and nutrition security among children, we work to expand access to school meal programs around the world. In the U.S. we are working to help close the “school breakfast gap”** — the number of children in low-income households who are eligible for, but not participating in, free school breakfast programs — so that all children have daily access to a nourishing school breakfast. In 2021, we continued our produce- to-donate program started in May 2020 to help Australians in need. In partnership with our suppliers, we continue to produce 10,000 meals per month for Foodbank Australia. This collaborative program had enabled 153,000 meals as of November 2021. Increasing food access *In 2020 (during the first year of COVID-19), nearly 12 million children were living in food insecure households (1 in 6/11.7 million) and 1 in 8 individuals was at risk of hunger (11.8%/38.3 million). Sources: Feeding America and U.S. Department of Agriculture Economic Research Report ** Prior to the COVID-19 pandemic, the breakfast gap included 3 million children. What is food security? Food security , as defined by the United Nations’ Committee on World Food Security, means that all people, at all times, have physical, social and economic access to sufficient, safe and nutritious food that meets their food preferences and dietary needs for an active and healthy life. GENERAL MILLS GLOBAL RESPONSIBILITY 58 Food Planet People Community
Our commitment to racial equity * : Equitable food access Nationwide n 41% of Black households n 37% of Latino households n 23% of white households Minnesota n 83% of Black households n 70% of Latino households n 32% of white households As part of General Mills’ commitment to advance racial equity, we direct our philanthropy and align employee volunteerism to support food banks, anti-hunger and racial justice organizations that are working to target and close racial disparities in food security and its disproportionate impacts on communities of color. The COVID-19 pandemic has exacerbated social inequities, including the disproportionate experience of food insecurity. Racial disparities in U.S. households experiencing food insecurity:* *As of July 2020, Census Household Pulse Survey reported by Northwestern University (national) and Wilder Research (Minnesota). Learn more . *Commitment includes equitable food access, equity in education and equity in representation . **In the Minneapolis and St. Paul, Minnesota metro area. r See how we are directing our philanthropic work to address food insecurity that disproportionately impacts people of color. WATCH VIDEO National partnerships Elevating food justice and racial equity in food- access partnerships with leading civil rights and anti-hunger organizations (NAACP , UnidosUS, Share our Strength) Culturally-specific initiatives Investment in locally driven solutions to equitable food access for and led by Black, Indigenous and people of color in historically marginalized communities** (Appetite for Change , Pillsbury United Communities, Comunidades Latinas Unidas En Servicio , Division of Indian Work) Systems change Uniting to improve food-access systems locally and nationally in the U.S. through Supplemental Nutrition Assistance Program (SNAP) promotion and support for school meals policy change. GENERAL MILLS GLOBAL RESPONSIBILITY 59 Food Planet People Community
Impact of the MealConnect platform created by Feeding America and funded by General Mills: n 43,000+ food businesses (grocery stores, restaurants, cafeterias) have donated their surplus food, creating billions of nourishing meals for food-insecure people. n 60+ food transport companies have used the platform n 3.1+ billion pounds of food recovered since 2014, equal to 2.6+ billion meals Food access Food recovery and distribution Food system insights and regeneration What is food recovery? Resources saved by recovering food Also known as food rescue, food recovery is the practice of intercepting or gleaning good surplus food that would otherwise go to waste from places such as restaurants, grocery stores, produce markets, or dining facilities and distributing it to local emergency food programs. Food recovery reduces GHG emissions and conserves natural resources. General Mills donated 49 million pounds of food in fiscal 2021. Based on the ReFED Insights Engine Impact Calculator (see next page), the impact of keeping that food out of landfills is equivalent to 1,925 passenger vehicles driven for 1 year. Learn more in the Planet section of this report. In the U.S., where 35% of all food goes unsold or uneaten, food waste is responsible for the following impacts:* 4% of U.S. GHG Emissions 14% of all Fresh Water Use 18% of all Cropland Use 24% of Landfill Inputs #1 material (EPA Estimate) *Source: ReFED We work with a variety of organizations around the world to increase food access and enable food recovery. Shown here are a few of our key partners and how their efforts intersect. Key hunger relief partners GENERAL MILLS GLOBAL RESPONSIBILITY 60 Food Planet People Community
Our actions: To ensure no good food goes to waste and that the world’s surplus food is used to nourish people, we leverage our philanthropy and General Mills' deep food system expertise to expand surplus food recovery. Our efforts and investments have resulted in grocery stores, restaurants and thousands of other food outlets around the globe gaining and adopting systematic food recovery solutions so that their good surplus food can now be used to nourish hungry people and does not end up in landfills. Since food waste and loss occur from "farm-to-fork” and impact growers, families, communities, the environment and businesses, we engage with a wide variety of partners to advance positive change. We bring a systems lens and take a collective impact approach to the issue, working with cross-sector coalitions and nonprofit organizations around the globe. Our focus areas include: n Expanding global knowledge and insights about the most scalable, high-impact solutions to food waste and loss n Strengthening the capacity, safety and efficiency of food banks worldwide n Catalyzing innovative new surplus food recovery solutions Our latest philanthropic support for ReFED — a leading U.S. nonprofit that works with businesses, government leaders, environmental organizations, community nonprofits, researchers, investors and others to advance food waste solutions — helped bring about the ReFED Insights Engine as part of the organization’s Roadmap to 2030 . A first-of-its-kind solution, the Insights Engine is an interactive online platform that enables any user from any sector to dynamically explore the food waste issue and model the projected impacts (climate, economic, social, etc.) of various solutions (see above). In addition to supporting broader food system solutions, we also donate surplus food from our own operations to enable meals for food-insecure people. Enabling food recovery 2021 Progress meals enabled worldwide by our food donations and philanthropic partners during 2021. We are working to enable 30 billion meals for hungry people by 2030, and have charitably enabled 17.1 billion meals since fiscal 2019. General Mills grants supported and strengthened food banks in more than 40 countries. 9 billion 40 + countries meals enabled by donations of General Mills surplus food worldwide during 2021, contributing to 365 million meals since 2010. children worldwide have access to nourishing school meals daily, with General Mills support. 41 million 1,095,500 + 46,843 retailers and foodservice operators worldwide empowered to participate in systemic food rescue through our global investments in food recovery technology.* *Through MealConnect and FareShareGo. r We support initiatives that help ensure good food doesn't go to waste. r The ReFED Insights Engine is a hub for food loss and waste data and solutions, providing information and insights to help people take meaningful action to reduce food waste. Find out how much food is being wasted in the U.S., learn why it's happening and see where it goes. Visit the Food Waste Monitor Learn which food waste reduction solutions are the most relevant and impactful for meeting specific goals. Visit the Solutions Database Explore ReFED's database of 850+ organizations offering products and services to help reduce food waste. Visit the Solutions Provider Directory Quantify the climate, natural resource and food security impacts of wasted food. Visit the Impact Calculator Understand the problem Explore solutions Find solution providers Calculate impact GENERAL MILLS GLOBAL RESPONSIBILITY 61 Food Planet People Community
Regenerative agriculture: Philanthropic impact Focus area Goal Partners Our approach: We leverage philanthropy to advance regenerative agriculture practices and support the conservation of natural resources and ecosystems around the world. Complementing our company’s broader sustainability and regenerative commitments, we invest in NGO-led initiatives that increase farmers’ economic resilience and advance respect for human rights, improve soil and water health and increase biodiversity through improved pollinator health and habitat. Learn more in the Planet section of this report. We also actively engage in public policy discussions to advance sustainability priorities — see related details in the report’s Introduction section. Regenerating ecosystems Improving the well-being of farming communities The philanthropic support* we provide to NGO partners, including CARE in Côte d’Ivoire and Ghana and Positive Planet in Madagascar, is helping smallholder farming communities improve their livelihoods and farming practices, empower female farmers, establish farmer cooperatives, increase food and nutrition security, support youth education and prevent child labor. These efforts collectively reach more than 58,400 smallholder farmers and their family members. r These cocoa farmers in Côte d'Ivoire are diversifying their household income sources through food crops. Farmer resilience Forest preservation Soil health Water stewardship *These efforts complement the collaborative work of our business teams and ingredient suppliers described in the Planet section of this report. Improve the well-being of 30,000 people (farmers and their families) by 2030 in smallholder farming communities from which General Mills sources cocoa and vanilla and other key ingredients. Accelerate the preservation and rehabilitation of forests in cocoa-producing regions of Côte d’Ivoire and Ghana. Support broad adoption of regenerative agriculture principles and best practices, such as no-till farming and the use of cover crops, to improve soil health. Invest in water stewardship funds and coalitions to protect and restore at-risk watersheds. GENERAL MILLS GLOBAL RESPONSIBILITY 62 Food Planet People Community
Our approach: Just as we care about the communities where our ingredients are grown, we also care about the places our employees call home. Around the world, we support our hometown communities through employee volunteerism and local community giving. Our employees are General Mills greatest asset as they bring our company’s purpose to life every day. Supporting local causes they are passionate about invigorates our employees while strengthening our hometown communities around the globe. Strengthening hometown communities We are proud of our company’s longstanding work and deep commitment to using our philanthropy as an added lever to advance racial equity. We work in targeted ways to use our resources and influence to bring an end to racial disparities in social outcomes, including student educational achievement and food insecurity . Listed below are examples of our efforts and impact. Advancing racial equity in charitable giving by General Mills and its Foundation over the last five years (fiscal 2017- 2021) to nonprofits in the Twin Cities (greater Minneapolis and St. Paul metro area), including $18 million toward promoting equitable food access and equity in K-12 education. $6.7 million 31 years $25 million In 1991, General Mills developed and hosted our first Dr. Martin Luther King Jr. Holiday Breakfast. Thirty years later, the event is attended by thousands of people each year to contemplate and celebrate the legacy of Dr. King. Since that time, General Mills and its Foundation have provided more than $6 million in support to the United Negro College Fund (UNCF) to help Black students get to and through college. Amount of charitable support that General Mills and its Foundation have provided to UNCF. hosting Dr. Martin Luther King Jr. Holiday Breakfast General Mills was recognized in the Points of Light 2021 Civic 50 report for helping to advance work on social justice through the MBCRE. As a cofounder of the Minnesota Business Coalition for Racial Equity (MBCRE) , we are helping the business sector sharpen and accelerate actions to improve conditions and advance equitable outcomes with and for Black Minnesotans. The coalition’s approach seeks systemic changes via public policy, philanthropy, allyship and workplace environments. The General Mills philanthropy team continues to work to ensure our charitable giving helps support organizations with missions and practices that advance racial equity and whose organizational makeup — including leaders (e.g., Executive Director, Board of Directors) and staff — is racially diverse and representative of the diverse communities they serve. In our 2021 review of our philanthropic portfolio in the Twin Cities, we integrated new practices to explicitly measure and review dimensions of organizational diversity, equity and inclusion as part of our grantmaking application to ensure equitable distribution and investment levels across grantmaking portfolios. Our approach includes supporting community-driven solutions guided by minority-led organizations, including: diverse and minority- led nonprofits SUPPORTING GENERAL MILLS GLOBAL RESPONSIBILITY 63 Food Planet People Community
We've committed to donating $500,000 to Black Men Teach to help increase the number of Black male elementary school teachers in Minnesota classrooms; and to co-investing $250,000 with the Minneapolis Foundation as part of their Reimagine Education initiative to support local nonprofit and education organizations to increase equity in Twin Cities*** schools. The Box Tops app has a new feature to support schools in need which allows supporters the option to direct their funds to improve the educational experiences in participating schools that meet U.S. government criteria. Our commitment to racial equity * : Equity in education As part of General Mills commitment racial equity, we use our philanthropy to accelerate opportunities to close gaps in academic outcomes that disproportionately impact students of color in our headquarters community of Minneapolis, Minnesota. Our progress: During fiscal 2021, we contributed more than US$1.5 million to more than two dozen nonprofit organizations that are working to bring about equity in education in our home state of Minnesota, including: n Improving equity in K-12 education – Supporting an ecosystem of education- transformation organizations, strengthening an array of holistic solutions that advance equitable educational outcomes across multiple levels. Grantee examples include: Ed Allies, Northside Achievement Zone , Voices for Racial Justice , ConnectedMN’s Digital Learning Fund, Great MN Schools. n College and Career Readiness – Supporting local solutions to including partners like Achieve Minneapolis, BestPrep and UNCF partnerships and scholarships — funded through the attendee participation, engagement and US$6 million raised to date through the Dr. Martin Luther King Jr. Holiday Breakfast event — for college support and equity in education. n Box Tops for Education TM – To advance equity in education and ensure all kids can reach their full potential, Box Tops is helping to equip teachers to identify and address racial bias, supporting programs that work to increase the number of teachers of color, and distributing Box Tops funds to impact schools in need. In 2021, we partnered with and provided grants** to organizations that are working toward greater equity in education to help schools increase teacher diversity and address racial inequities in the classroom. These partners include: Black Men Teach, Ed Allies, Teach for America, TNTP (formerly The New Teacher Project), Innocent Classroom, Minneapolis Foundation, Culturally Responsive School Leadership Institute . The Box Tops for Education digital program, operated by General Mills, provides funds for participating U.S. schools, which can be used for supplies and other priorities. Box Tops impact includes: n US$940 million provided through Box Tops for Education since the program began in 1996. n US$5.48 million earned by U.S. schools during the 2020-2021 school year. n More than 3.5 million people have downloaded and opened the Box Tops app n 80,639 U.S. schools benefiting from the program Box Tops for Education TM *Our commitment to racial equity includes equitable food access , equity in education and equity in representation . **Funded through Box Tops for Education and General Mills educational equity grantmaking program. Learn more . ***Includes the Minneapolis and St. Paul, Minnesota metropolitan area. r Learn more about how Box Tops is elevating racial equity in education. WATCH VIDEO GENERAL MILLS GLOBAL RESPONSIBILITY 64 Food Planet People Community
Our approach: We support our hometown communities around the world through local community giving and employee volunteerism. We encourage and empower our employees to apply their skills, expertise and passion to help strengthen their communities. We are proud of the 80+% employee volunteerism rate that General Mills has maintained in recent years. During the COVID-19 pandemic, we have encouraged our employees to support their communities in modified ways that keep everyone safe and healthy, such as the food donation event we hosted at our headquarters, which enabled employees and their families to drive-up and donate foods and household items for area charities. Employee volunteerism and giving for community impact r General Mills employees and volunteers from Black Men Teach assembled backpacks for students in North Minneapolis. Learn more . A force for good in Northeast Philadelphia For the past seven years, an average of 20 to 30 General Mills employees annually have been volunteering at the Frankford Boys and Girls Club in Northeast Philadelphia, serving as mentors, supporting youth leadership activities and helping to host holiday celebrations. During that time, General Mills also supported a major renovation of the club’s decaying facility through community grants and many hours of volunteer time, including monthly visits to help with demolition and improvements to the building’s interior, exterior and surrounding area. Since completion of the renovation, enrollment and participation have increased 500% — from 40 kids to more than 200 daily and nearly 300 in the summer. “We look forward to further expanding our strong partnership with the Boys and Girls Club and truly being a force for good. We can be proud of the impact General Mills is having with these amazing kids and our communities,” said Billy Watts, Customer Vice President East and Industry Relations, General Mills. r With help from General Mills and other sponsors, the facility was renovated with new bathrooms, windows, heating and air conditioning and electrical system, a refurbished kitchen, gymnasium, computer lab, reading lab and art rooms. r Prior to COVID-19, General Mills volunteers met regularly with kids in person to read stories, practice interviewing skills, help with school applications and other activities. During the pandemic, volunteers shifted to virtual engagement with the kids and socially distanced, outdoor events. r As part of the renovation, employees helped paint the exterior and plant gardens around the building. We invested in more than 52 hometown communities of General Mills with local grants during fiscal 2021. 52 471 charities worldwide received philanthropic funding from General Mills and our Foundation**, enabling them to serve and strengthen communities. *US$1,065,777 raised by employees with the General Mills match during fiscal 2021. **Beginning in January 2022, we are shifting our philanthropy away from the General Mills Foundation and transitioning to corporate-funded philanthropy. COMMUNITY IMPACT 2021 Progress raised by employees for 2,060 nonprofits with the General Mills match.* $ 1 million 3,245 employees participated with contributions through the General Mills employee charitable gift matching program. EMPLOYEE GIVING GENERAL MILLS GLOBAL RESPONSIBILITY 65 Food Planet People Community
Skills-based volunteerism: Many of our employees apply their professional skills and knowledge to make a difference at the local and societal levels, including through our in-house GoodWorks pro-bono program and our international nonprofit partner, Partners in Food Solutions: n GoodWorks: Through GoodWorks, General Mills employees lend their expertise in marketing, finance, sourcing and supply chain management, innovation, technology and quality to help nonprofit organizations overcome challenges and scale up their impact. Since the program began in 2009, more than 200 volunteers have completed over 60 projects. In 2020, the GoodWorks program expanded its community focus to provide targeted support for local nonprofits and small businesses owned by Black, Indigenous and people of color. In 2021, GoodWorks teams in Minnesota provided support to eight small businesses owned by people of color and nonprofit organizations serving people of color in Minneapolis and St. Paul, including marketing and business assistance for their projects. n Partners in Food Solutions: Our employees volunteer with Partners in Food Solutions (PFS) , an independent nonprofit organization that links the technical and business expertise of volunteer employees from seven food companies with high-potential food processors and millers across Africa. Through the program, more than 725 General Mills employees globally have contributed over 78,000 hours to 306 different clients across Africa. By sharing their diverse expertise, General Mills employees have assisted entrepreneurs in growing their businesses and supporting a supplier base of more than 1.1 million farmers. v Lucy Buteyo, a senior quality engineer at General Mills, participated as a PFS mentor with Oyeyemi Fadairo (pictured here), who was a quality control lead at Wilson’s Juice in Nigeria. They met monthly for 6 months during 2021 to discuss skills and design a food safety plan. “I joined the mentorship program because I wanted to reciprocate the mentoring opportunities I have been fortunate to receive during my career and share my knowledge and skills for good,” said Buteyo. “Through the mentorship, we’ve been able to identify necessary areas of improvement at my company. I have noticed defining moments that have helped shape my thinking,” said Fadairo. Through the GoodWorks program, a cross-functional team of General Mills employees helped the Minnesota Department of Human Services develop a campaign to raise awareness about how Minnesotans in need can access food assistance through the Supplemental Nutrition Assistance Program (SNAP). The GoodWorks team conducted research, formulated a strategy and supported the campaign’s execution with media activation, website assistance and a toolkit for organizations to use in helping to spread the word. Key outcomes of the outreach campaign include: n More than 17,000 SNAP applicants received assistance from outreach partners. n SNAP applicant eligibility more than tripled as a result of targeted campaign messaging and application assistance from trained SNAP specialists. n The Minnesota Department of Human Services received a 2021 Golden GOVIT Award for the campaign collaboration with General Mills. See the campaign at MNFoodHelper.org. Increasing food access through SNAP outreach campaign Discover how SNAP can stretch your food budget. GETTING HELP WITH THE GROCERIES IS EASIER THAN YOU THIN K . r See how General Mills GoodWorks volunteers helped Maazah Chutney, a small business owned by women of color, tell their brand story. Learn more . WATCH VIDEO GENERAL MILLS GLOBAL RESPONSIBILITY 66 Food Planet People Community
Juneteenth Day of Action On June 18, 2021, General Mills hosted our first Juneteenth Day of Action. Employees at our headquarters packed more than 8,000 school supply kits for the benefit of Minneapolis-area students and families served by the Northside Achievement Zone , Way to Grow and ACER. Disaster relief: When disaster strikes in the communities where we operate, General Mills is ready to contribute in ways that provide relief and help communities recover. Through financial grants and General Mills food donations, we help to ensure that our humanitarian and disaster relief partners are resourced and equipped to help communities during their most urgent times of need. In fiscal 2021, we provided the following support: n $80,000 in financial grants from our brands and the General Mills Foundation in response to the severe winter storms in Texas. Our businesses and brands also donated two truckloads of food to the Feeding Texas food bank, enabling 60,00 meals. n $35,000 grant to American Red Cross to help communities in Iowa and Illinois affected by the El Derecho weather events. n $50,000 in disaster relief for communities impacted by West Coast wildfires in California, Washington and Oregon, including $40,000 to American Red Cross and $10,000 to United Animal Nations for the Red Rover Response program to support displaced animals. Employee giving: Employees in North America, Europe, Australia and India participate in the General Mills gift matching program, which offers up to a US$1,000 match when they give to their favorite charities. More than 3,200 employees had their gifts matched during fiscal 2021. in financial grants provided by our brands and the General Mills Foundation during fiscal 2021 in response to natural disasters in our communities, in addition to food donations. $ 165,000 DISASTER RELIEF 2021 Progress in charitable giving contributed by General Mills and our Foundation* worldwide in fiscal 2021. in cumulative giving provided by General Mills and our Foundation to strengthen communities since our Foundation was established in 1954.** $ 98 million $ 2.6 billion STRENGTHENING COMMUNITIES *Beginning in January 2022, we are shifting our philanthropy away from the General Mills Foundation and transitioning to corporate-funded philanthropy. **This figure includes General Mills Foundation grants, Box Tops for Education™ giving, corporate contributions and the company’s global food donations. GENERAL MILLS GLOBAL RESPONSIBILITY 67 Food Planet People Community
APPENDIX ESG issues and definitions Animal welfare Advance strategies to ensure the humane treatment of animals throughout our value chain. Biodiversity Manage the impact on biodiversity loss and habitat destruction through the company’s activities related to operations and land use. Board and executive oversight Ensure appropriate oversight by our executive leadership team and Board/Board Committees of material ESG issues. Climate change Advance programs to reduce greenhouse gas emissions in our own operations and across our entire value chain to mitigate the effects of climate change. Community engagement and giving Improve the communities in which we live and work through philanthropic efforts, volunteerism and other programming. Deforestation Advance strategies to eliminate deforestation and the resulting impacts on biodiversity, endangered species and climate change. Diversity, equity and inclusion Foster a culture of inclusion and belonging that allows all our employees to thrive and ensures diversity of input and perspectives; and ensure our external impact is inclusive of diverse communities in our markets around the world. Ethics and compliance Operate with integrity and with the highest standards in oversight, ethics and compliance. Food safety and quality Set and maintain the highest standards for food safety and quality. Health and nutrition Improve the health profile of products, including by offering nutrient-dense foods, and diversify product offerings to meet diverse consumer needs and preferences, including natural and organic foods. Human rights Respect the rights of all workers and communities across our value chain in alignment with the United Nations Guiding Principles on Business and Human Rights. Hunger and food security Food security is when all members of a community have physical, social and economic access at all times to the foods they want and need. Ingredient sourcing Improve the social, environmental and economic impacts of raw materials through verification/certification programs and origin-direct investment that improves farmer livelihoods, protects environmental resources and enhances ingredient quality. Packaging Reduce the environmental impact of packaging by increasing use of recycled, recyclable, reusable and innovative bio-based materials and collaborating to promote recycling and improve recycling infrastructure. Privacy and data security Act responsibly and transparently with regard to the collection, retention and use of personal and proprietary data. Public policy Engage with policy makers to advocate and advance the interests of General Mills and its stakeholders, maintain the company’s license to operate, and drive social and environmental improvement. Regenerative agriculture Advance use of regenerative agriculture principles by farmers and ranchers to strengthen ecosystems and community resilience, including improving soil health, biodiversity, water quality, cow and dairy herd well-being and farm economics. Regulatory compliance Prepare for and comply with ESG rules and regulations and enhance the company’s ESG disclosures. Responsible marketing and labeling Maintain the highest standards for marketing and advertising, including through adherence to internal and industry guidelines when marketing to children and adults, and provide accurate nutrition and ingredient labeling. Responsible sourcing Manage ESG risk in the supply chain by driving ongoing supplier progress in the areas of health and safety, human rights, business integrity and the environment. Talent management Recruit and retain talented employees by providing competitive pay and benefits; investing in training and development; engaging employees through a work environment that encourages innovation, productivity and flexibility; and supporting the physical, emotional, financial and social well-being of employees. Transparency Communicate openly and disclose accurate information about our products and business practices. Waste Decrease solid waste generation, increase recycling and waste processed for energy recovery so less waste from our production facilities ends up in landfills, and reduce food loss and waste across our value chain through food rescue and recovery programs that keep surplus food out of the waste stream. Water stewardship Reduce water use and ensure appropriate water management throughout our value chain, especially in water-stressed areas. Workplace safety Maintain a safe workplace for our employees, contractors and visitors. CONSUMING SELLING SHIPPING PRODUCING PACKAGING TRANSFORMING AGRICULTURE CIRCLES NOTE VALUE CHAIN PHASES FOR EACH RELEVANT ISSUE GENERAL MILLS GLOBAL RESPONSIBILITY 68
Key manufacturing metrics (wholly owned or controlled production facilities globally) * In thousands, except rate data 2017 2018 2019 2020 2021 Energy usage rate (GJ/metric ton of product) 1.91 1.89 1.91 1.95 1.92 Energy usage (GJ) 9,787 9,051 9,385 10,052 10,201 GHG emissions rate (metric tons CO 2 e/ metric tons of product)** 0.165 0.16 0.16 0.12 0.08 GHG emissions (Scopes 1 and 2)** (metric tons CO 2 e) 831 811 812 633 446 Scope 1 (metric tons CO 2 e) 254 267 274 303 334 Scope 2 (metric tons CO 2 e)** 576 511 511 330 112 Water consumption rate (cubic meters/ metric ton of product) 2.99 2.85 2.72 2.76 2.56 Water consumption (cubic meters) 15,100 13,604 13,367 14,260 13,607 Groundwater (cubic meters) 6,400 5,772 5,545 5,714 5,226 Municipal (cubic meters) 8,700 7,832 7,822 8,498 8,369 Solid waste generation rate (metric tons/metric ton of product)*** 0.045 0.065 0.061 0.064 0.063 Solid waste (metric tons)*** 228 309 299 329 337 Food waste (metric tons)**** 2.24 1.71 Percentage of owned production facilities that achieved zero waste to landfill***** (%) 14% 20% 24% 30% 28% *Data in this table is reported on a fiscal year basis and represent wholly owned or controlled production facilities globally. Past fiscal years have not been adjusted for acquisitions or divestitures. Some data are restated compared to reporting in prior years to reflect improvements in data gathering and tracking methodologies. Beginning in 2019, data reflects the acquisition of Blue Buffalo Pet Products, Inc., completed in April 2018. **Scope 2 GHG emissions data were calculated using the location-based method from 2017-2019 and the market-based method (applying RECS and European Residual Mix Factors) in 2020 and 2021. These data were externally verified for 2015- 2019 by Bureau Veritas, and for 2020-2021 by Apex Companies LLC. ***Solid waste data is from production and excludes waste associated with construction as well as nonproduction activities such as new product trials. **** General Mills defines food waste following the Food Loss & Waste Protocol Standard and the baseline year for our goal reduction is fiscal 2020 (not reported for earlier years). ****These facilities sent no waste to landfill or incineration without energy recovery. Data includes facilities that were operating at the end of the relevant fiscal year. Location Energy attribute certificates (GJ)* Total electricity use** % renewable electricity*** Type United States and Canada 2,550,780 3,782,592 69% RECs (VPPA) Europe 491,991 538,902 91% Guarantee of Origin All other geographies 0 507,597 n/a Total General Mills 3,042,771 4,829,091 63% *Certificates to prove renewable energy consumption. One (1) EAC represents one (1) MWh of renewable electricity generated. **Scope includes all globally o wned General Mills facilities (Manufacturing, R&D, Offices, Warehouses, HD Shops, and Cake Kitchens). ***Aligned with RE100 definition; t otal energy attribute certificates / total electricity use Renewable electricity, fiscal 2021 SBTi Target boundary GHG Protocol Fiscal 2021 Fiscal 2020 Fiscal 2021 Fiscal 2020 Scope 1 364,000 335,000 364,000 335,000 Scope 2 (market-based)** 195,000 412,000 195,000 412,000 Scope 3 13,300,000 12,800,000 17,300,000 16,700,000 Total 13,859,000 13,546,000 17,859,000 17,446,000 *See below for GHG calculation methodology and definitions. Scope 1 and 2 totals differ from the Key manufacturing metrics to the left as the data in this table include those locations as well as other wholly owned or controlled facilities globally (such as off ice s and Häagen-Dazs shops) as well as fleet vehicles. ** Ge nera l M ills uses the market-based emissions methodology for Scope 2 emissions, which considers any contractual instrume nts that may b e used in competitive energy markets, such as green tariffs, renewable certificates, or PPAs. Both mar ket-based and location-based emissions are reported in our CDP Climate disclosure.. General Mills GHG emissions by scope (metric tons CO 2 e) * GHG calculation methodology We work with Quantis to cal cul ate our global GHG emissi ons foo tprint each fiscal year, fo llowing the guide lines of the GHG Pro to col Co rporate Accounting and Re porting Standard . This footprint cove rs our co mplete val ue chain. Fo r our 203 0 sci ence-b ased t arg et, we define our emissi ons bound aries in alignment wit h the Sc ience -based Targe t Ini tiat ive (SBTi ): S cop e 1: Di rect gre enhouse (G HG ) emiss ions that occur from sources that are co ntro lled o r owne d by an organiz at ion (e.g ., emissi ons asso ciated with fuel combustion in bo ilers, furnace s, veh icles). Ge neral M ills us es op erat iona l contro l to cate gorize those emissions within its org ani zat ional bounda ry. Sco pe 2: Ind irec t G HG em iss ions asso ciate d with the purcha se of electricity, ste am, he at , or co oling. Genera l Mil ls uses operat ion al co ntro l to cate gorize those emissions within its org ani zat ional b oundar y. General Mills uses the market-based metho dolo gy for cal culation of our Scope 2 emissions, whi ch cons iders any co ntract ual inst rument s that m ay be used in competitive energy marke ts, su ch as green tariffs , renewa ble certifi cates , or PPA s. S cop e 3: Ind irec t G HG em iss ions occu rring fro m assets not owned or controlled by the re porting orga nizat ion, but t hat the orga nizatio n ind ire ctly impacts in its valu e chain. Scope 3 e missio ns include all sources not within an organization’s scope 1 and 2 boundar y, as outlined by the GH G Protoco l. General Mil ls us es operat ional con tro l to categ orize those emissio ns within its org anizat ional boundary. Cons iste nt with SBTi guideli nes, our ta rg ets focu s on the categories of GHG emiss ions that are the most i mpactful and actiona ble for Ge neral M ills, a nd excl ude e miss ions suc h as low- volume ingredi ents, capital good s, employe e comm uting, franchises, downstream warehouse and storag e at retail, consum er trips to store and end of life (cons umer food waste). S cope 1, 2 and 3 data in the above table were externa lly verified b y Apex Companies, LLC, and our verification letter can be found on our w ebsite . We work to continually update our methodology, visibility and accuracy, and update resul ts as appropriate each year. Our Fiscal 2020 baseline will be re-verified if there is a change greater than 5%. Data to be finalized and updated Environmental Data Summary GENERAL MILLS GLOBAL RESPONSIBILITY 69
Global Reporting Initiative index * Disclosure Location/comments GRI 102: General Disclosures Organizational profile 102-1 Name of the organization 2021 10-K 102-2 Activities, brands, products, and services Introduction, 2021 10-K 102-3 Location of headquarters 2021 10-K 102-4 Location of operations 2021 10-K 102-5 Ownership and legal form 2021 10-K 102-6 Markets served General Mills website 102-7 Scale of the organization 2021 Annual Report 102-8 Information on employees and other workers People 102-9 Supply chain Introduction, Planet 102-10 Significant changes to the organization and its supply chain 2021 Annual Report 102-11 Precautionary Principle or approach Planet 102-12 External initiatives Introduction, Planet, Community 102-13 Membership of associations Introduction, Planet, Community Strategy 102-14 Statement from senior decision-maker CEO letter, 2021 Annual Report 102-15 Key impacts, risks, and opportunities 2021 10-K Ethics and integrity 102-16 Values, principles, standards, and norms of behavior Introduction, People 102-17 Mechanisms for advice and concerns about ethics People Governance 102-18 Governance structure 2021 Proxy Statement 102-19 Delegating authority 2021 Proxy Statement 102-20 Executive-level responsibility for economic, environmental, and social topics 2021 Proxy Statement, Introduction Disclosure Location/comments GRI 102: General Disclosures (cont.) Governance (cont.) 102-21 Consulting stakeholders on economic, environmental, and social topics 2021 Proxy Statement 102-22 Composition of the highest governance body and its committees 2021 Proxy Statement 102-23 Chair of the highest governance body 2021 Proxy Statement 102-24 Nominating and selecting the highest governance body 2021 Proxy Statement 102-25 Conflicts of interest 2021 Proxy Statement 102-26 Role of highest governance body in setting purpose, values, and strategy 2021 Proxy Statement, Introduction 102-28 Evaluating the highest governance body's performance 2021 Proxy Statement 102-29 Identifying and managing economic, environmental, and social impacts 2021 Proxy Statement, Introduction 102-30 Effectiveness of risk management processes 2021 Proxy Statement, Introduction 102-31 Review of economic, environmental, and social topics 2021 Proxy Statement, Introduction 102-32 Highest governance body's role in sustainability reporting Introduction 102-33 Communicating critical concerns 2021 Proxy Statement 102-34 Nature and total number of critical concerns 2021 Proxy Statement 102-35 Remuneration policies 2021 Proxy Statement 102-36 Process for determining remuneration 2021 Proxy Statement 102-37 Stakeholders involvement in remuneration 2021 Proxy Statement Stakeholder engagement 102-40 List of stakeholder groups Introduction, Planet, Community 102-41 Collective bargaining agreements Approximately 35% of U.S. production employees are covered by CBAs. 102-42 Identifying and selecting stakeholders Introduction, Planet, Community *Using GRI 2016 Sustainability Reporting Standards. Reporting disclosures may not be applied fully for all Standards. GENERAL MILLS GLOBAL RESPONSIBILITY 70
Global Reporting Initiative index (cont.) Disclosure Location/comments GRI 102: General Disclosures (cont.) Stakeholder engagement (cont.) 102-43 Approach to stakeholder engagement Introduction, Planet, Community 102-44 Key topics and concerns raised Introduction, Food, Planet, Community Reporting practice 102-45 Entities included in the consolidated financial statements 2021 Annual Report 102-46 Defining report content and topic boundaries Introduction 102-47 List of material topics Introduction 102-48 Restatements of information Appendix - Environmental data summary 102-49 Changes in reporting Introduction 102-50 Reporting period Introduction 102-51 Date of most recent report Apr-20 102-52 Reporting cycle Annual 102-53 Contact point for questions regarding the report Introduction 102-54 Claims of reporting in accordance with the GRI Standards Introduction, Appendix - GRI Index 102-55 GRI content index Appendix - GRI I ndex 102-56 External assurance Introduction GRI 200 Economic Standards Series GRI 201: Economic Performance 201-1 Direct economic value generated and distributed Community, Planet, 2021 Annual Report, 2021 Proxy Statement Disclosure Location/comments GRI 200 Economic Standards Series (cont.) GRI 201: Economic Performance (cont.) 201-2 Financial implications and other risks and opportunities due to climate change Planet, CDP - Climate Change Disclosure 201-3 Defined benefit plan obligations and other retirement plans 2021 10-K GRI 203: Indirect Economic Impacts 203-1 Infrastructure investments and services supported Planet, Community 203-2 Significant indirect economic impacts Planet, Community GRI 204: Procurement Practices 204-1 Proportion of spending on local suppliers Planet GRI 205: Anti-corruption 205-1 Operations assessed for risks related to corruption People 205-2 Communication and training about anti- corruption policies and procedures People GRI 300 Environmental Standards Series GRI 301: Materials 301-2 Recycled input materials used Planet 301-3 Reclaimed products and their packaging materials Planet GRI 302: Energy 302-1 Energy consumption within the organization Planet, Appendix - Environmental data summary 302-2 Energy consumption outside of the organization CDP - Climate Change Disclosure 302-3 Energy intensity Planet, Appendix - Environmental data summary 302-4 Reduction of energy consumption Planet GENERAL MILLS GLOBAL RESPONSIBILITY 71
Global Reporting Initiative index (cont.) Disclosure Location/comments GRI 300 Environmental Standards Series (cont.) GRI 303: Water 303-1 Water withdrawal by source Planet, Appendix - Environmental data summary 303-2 Water sources significantly affected by withdrawal of water Planet 303-3 Water recycled and reused Planet GRI 304: Biodiversity 304-2 Significant impacts of activities, products, and services on biodiversity Planet 304-3 Habitats protected or restored Planet GRI 305: Emissions 305-1 Direct (Scope 1) GHG emissions Planet, Appendix - Environmental data summary 305-2 Energy indirect (Scope 2) GHG emissions Planet, Appendix - Environmental data summary 305-3 Other indirect (Scope 3) GHG emissions Planet, CDP - Climate Change Disclosure 305-4 GHG emissions intensity Planet, Appendix - Environmental data summary 305-5 Reduction of GHG emissions Planet 305-6 Emissions of ozone-depleting substances (ODS) Ozone-depleting substances (ODS) are most commonly used in small quantities for closed-loop refrigeration systems and occasional fumigation activities. ODS emissions are strictly regulated. 305-7 Nitrogen oxides (NOX), sulfur oxides (SOX), and other significant air emissions Air emissions primarily include particulate matter and organic compounds from ingredient handling, cooking and drying, as well as emissions associated with fuel combustion. Our production facilities are governed by applicable regulations as well as our compliance management program. Disclosure Location/comments GRI 300 Environmental Standards Series (cont.) GRI 306: Effluents and Waste 306-1 Water discharge by quality and destination We do not discharge untreated sanitary wastewater to land or surface waters at any of our locations. Wastewater discharges primarily consist of organic matter from ingredient handling, food production and cleaning processes. Our production facilities are governed by applicable regulations as well as our compliance management program. 306-2 Waste by type and disposal method Planet 306-3 Significant spills There were no significant spills at our manufacturing locations during the reporting period. 306-4 Transport of hazardous waste The quantity of hazardous waste produced and shipped is insignificant relative to the amount of solid waste generated at General Mills. Hazardous waste shipping and disposal is restricted by government regulations. 306-5 Water bodies affected by water discharges and/or runoff No water bodies are significantly affected by company discharges. Our production facilities are governed by applicable regulations as well as our compliance management program. GRI 307: Environmental Compliance 307-1 Noncompliance with environmental laws and regulations General Mills incurred 6 Notices of Violations (NOVs) and no significant fines during the reporting period. GRI 308: Supplier Environmental Assessment 308-1 New suppliers that were screened using environmental criteria Supplier Code of Conduct GENERAL MILLS GLOBAL RESPONSIBILITY 72
Global Reporting Initiative index (cont.) Disclosure Location/comments GRI 400 Social Standards Series GRI 401: Employment 401-2 Benefits provided to full-time employees that are not provided to temporary or part-time employees People GRI 403: Occupational Health and Safety 403-1 Workers representation in formal joint management-worker health and safety committees People 403-2 Types of injury and rates of injury, occupational diseases, lost days and absenteeism, and number of work-related fatalities People 403-4 Health and safety topics covered in formal agreements with trade unions People GRI 404: Training and Education 404-2 Programs for upgrading employee skills and transition assistance programs People 404-3 Percentage of employees receiving regular performance and career development reviews People GRI 405: Diversity and Equal Opportunity 405-1 Diversity of governance bodies and employees People, 2021 Proxy Statement GRI 407: Freedom of Association and Collective Bargaining 407-1 Operations and suppliers in which the right to freedom of association and collective bargaining may be at risk Planet GRI 408: Child Labor 408-1 Operations and suppliers at significant risk for incidents of child labor Planet Disclosure Location/comments GRI 400 Social Standards Series (cont.) GRI 409: Forced or Compulsory Labor 409-1 Operations and suppliers at significant risk for incidents of forced or compulsory labor Planet GRI 412: Human Rights Assessment 412-1 Operations that have been subject to human rights reviews or impact assessments Planet 412-3 Significant investment agreements and contracts that include human rights clauses or that underwent human rights screening Planet, Responsible sourcing Supplier Code of Conduct GRI 413: Local Communities 413-1 Operations with local community engagement, impact assessments, and development programs Planet, Community GRI 414: Supplier Social Assessment 414-1 New suppliers that were screened using social criteria Responsible sourcing Supplier Code of Conduct 414-2 Negative social impacts in the supply chain and actions taken Planet GRI 415: Public Policy 415-1 Political contributions Civic Involvement, Introduction GRI 416: Customer Health and Safety 416-1 Assessment of the health and safety impacts of product and service categories Food, People 416-2 Incidents of noncompliance concerning the health and safety impacts of products and services Food GRI 417: Marketing and Labeling 417-1 Requirements for product and service information and labeling Food GENERAL MILLS GLOBAL RESPONSIBILITY 73
Global Reporting Initiative index (cont.) Disclosure Location/comments Food Processing Sector Supplement Across All Aspects of Sourcing FP1 Percentage of purchased volume from suppliers compliant with company’s sourcing policy. Planet, Responsible sourcing Supplier Code of Conduct FP2 Percentage of purchased volume which is verified as being in accordance with credible, internationally recognized responsible production standards, broken down by standard. Planet Healthy and Affordable Food FP4 Nature, scope and effectiveness of any programs and practices that promote access to healthy lifestyles; the prevention of chronic disease; access to healthy, nutritious and affordable food; and improved welfare for communities in need. Food, Planet, Community Customer Health and Safety FP5 Percentage of production volume manufactured in sites certified by an independent third party according to internationally recognized food safety management system standards. Food FP6 Percentage of total sales volume of consumer products, by product category, that are lowered in saturated fat, trans fats, sodium and added sugars. Food FP7 Percentage of total sales volume of consumer products, by product category, that contain increased nutritious ingredients like fiber, vitamins, minerals, phytochemicals or functional food additives. Food Product and Service Labeling FP8 Policies and practices on communication to consumers about ingredients and nutritional information beyond legal requirements. Food AskGeneralMills.com SmartLabel.org Disclosure Location/comments Food Processing Sector Supplement (cont.) Product and Service Labeling (cont.) FP9 Percentage and total of animals raised and/or processed, by species and breed type. General Mills does not raise or process animals in its production operations. Meat that is used in our products is processed by our suppliers. For information on our approach to animal welfare, see our policy . Animal Husbandry FP10 Policies and practices, by species and breed type, related to physical alterations and the use of anaesthetic. General Mills does not physically alter animals or use anaesthetics. For information on our approach to animal welfare, see our policy . FP11 Percentage and total of animals raised and/or processed, by species and breed type, per housing type. Planet General Mills does not raise or process animals. For information on our approach to animal welfare, see our policy . FP12 Policies and practices on antibiotic, anti-inflammatory, hormone, and/ or growth promotion treatments, by species and breed type. Planet Animal welfare policy Transportation, Handling, and Slaughter FP13 Total number of incidents of noncompliance with laws and regulations, and adherence with voluntary standards related to transportation, handling, and slaughter practices for live terrestrial and aquatic animals. General Mills does not transport, handle or slaughter live terrestrial or aquatic animals. GENERAL MILLS GLOBAL RESPONSIBILITY 74
United Nations Global Compact Principles Principle Information in report Human rights Principle 1: Businesses should support and respect the protection of internationally proclaimed human rights; and Ethics and compliance Human rights Supplier Code of Conduct Principle 2: make sure that they are not complicit in human rights abuses. Ethics and compliance Human rights Labor Principle 3: Businesses should uphold the freedom of association and the effective recognition of the right to collective bargaining; Human rights Supplier Code of Conduct Principle 4: the elimination of all forms of forced and compulsory labor; Human rights Supplier Code of Conduct Principle 5: the effective abolition of child labor; and Human rights Supplier Code of Conduct Principle 6: the elimination of discrimination in respect to employment and occupation. Ethics and compliance Global inclusion Supplier Code of Conduct Environment Principle 7: Businesses should support a precautionary approach to environmental challenges; Climate change Ingredient sourcing Regenerative agriculture Water stewardship Principle 8: undertake initiatives to promote greater environmental responsibility; and Climate change Regenerative agriculture Responsible sourcing Sustainable operations Water stewardship Principle 9: encourage the development and diffusion of environmentally friendly technologies. Climate change Regenerative agriculture Sustainable operations Anti-corruption Principle 10: Businesses should work against corruption in all its forms, including extortion and bribery. Supplier Code of Conduct Code of Conduct GENERAL MILLS GLOBAL RESPONSIBILITY 75
The Sustainability Accounting Standards Board (SASB) is an independent, standards-setting organization that promotes disclosure of material sustainability information to meet investor needs. This table references the Standard for the Processed Foods industry as defined by SASB’s Sustainable Industry Classification System (SICS) and identifies how General Mills addresses each topic. Note that some responses may not be fully aligned with SASB’s definition, but represent the content most closely aligned with that indicator. Topic SASB indicator code General Mills response Energy Management FB-PF-130a.1 Total energy usage in FY21 for our owned production facilities was 10,201,111 gigajoules (GJ); 63% renewable electricity sourced for our global operations. Water Management FB-PF-140a.1 Total water consumption in FY21 in our owned production facilities was 13,607,000 cubic meters. Approximately 7% of our water withdrawals are from water-stressed areas. See CDP Water for details. FB-PF-140a.2 No incidents related to water quality and/or quality permits, standards or regulations in FY21. FB-PF-140a.3 Water issues are local, so we take a risk-based approach to address risks in priority watersheds across our global supply chain. Our goal is to champion the activation of water stewardship plans for the company’s most material and at-risk watersheds. See Water stewardship and CDP Water for details. Food Safety FB-PF-250a.1 96% of General Mills owned production facilities were Global Food Safety Initiative (GFSI) certified in FY21; there were zero critical nonconformances. FB-PF-250a.2 93% of our global co-production sites, 85% of our global ingredient suppliers and 97% of our North American ingredient vendor sites were GFSI certified in FY21. FB-PF-250a.3 No food safety violations were received in FY21. FB-PF-250a.4 We conducted one small voluntary product recall globally in fiscal 2021 for soup. Health and Nutrition FB-PF-260a.1 In FY21, 41% of General Mills’ global volume met our Nutrition-Forward criteria. FB-PF-260a.2 In FY19, we launched a new global health reporting system focused on Nutrition-Forward Foods that leverages established, transparent nutrition criteria grounded in regulations and dietary guidance and measures across our global portfolio. See Nutrition for details. Product Labeling and Marketing FB-PF-270a.2 We disclose the presence of bioengineered ingredients (GMOs) on our U.S. packages under the National Bioengineered Food Disclosure Standard for all applicable FDA and USDA regulated products. In FY21 almost all of our applicable product labels disclosed this information, with all products in compliance prior to the 2022 compliance deadline. We are also voluntarily labeling all products that contain highly refined BE ingredients, with expected completion by Summer 2023. FB-PF-270a.3 General Mills fully complies with all requirements of CFBAI and locally applicable programs. We are not aware of any instance of noncompliance by General Mills in the past several years, and CFBAI has confirmed this in its reports. Packaging Lifecycle Management FB-PF-410a.1 In FY21, 89% of our packaging was recyclable (by weight) and 48% of our packaging was made from recyclable content. FB-PF-410a.2 We continually work to reduce the environmental impact of packaging by increasing use of recycled and recyclable materials, innovating to make our materials better, and leading through external collaboration. See Packaging for details. Environmental and Social Impacts of Ingredient Supply Chain FB-PF-430a.1 In FY20, we achieved our goal to sustainably source our 10 priority ingredients (representing approximately 40% of our annual raw material purchases). FB-PF-430a.2 In FY21, 15 of our owned locations, 30 of our co-packers and 190 of our Tier 1 suppliers were audited. See Responsible sourcing for additional details. Ingredient Sourcing FB-PF-440a.1 Our footprint consists of approximately 60 key ingredient and manufacturing watersheds that are the most critical for operations. Of those, 10 are prioritized as high risk. See Water stewardship and CDP Water for details. FB-PF-440a.2 In FY20, we achieved our goal to sustainably source 10 priority ingredients: cocoa, vanilla, oats, U.S sugar beets, U.S. wheat, U.S. corn (dry milled), U.S dairy (raw fluid milk), fiber packaging, sugarcane and palm oil. We have now shifted our focus to programs that regenerate the planet and create positive outcomes for people. See Ingredient sourcing and Regenerative agriculture for details. Sustainability Accounting Standards Board reference table GENERAL MILLS GLOBAL RESPONSIBILITY 76